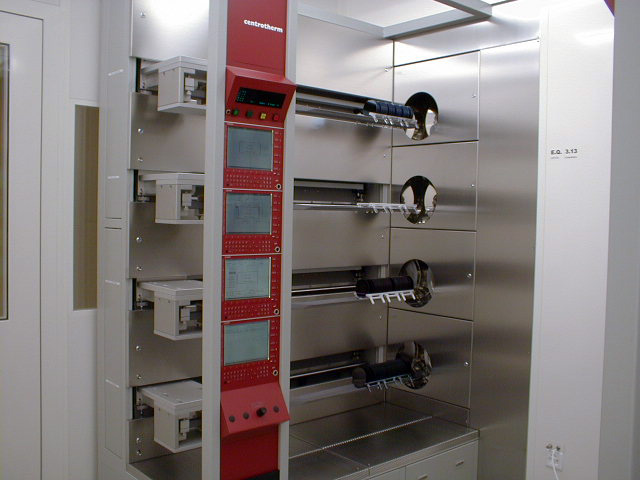
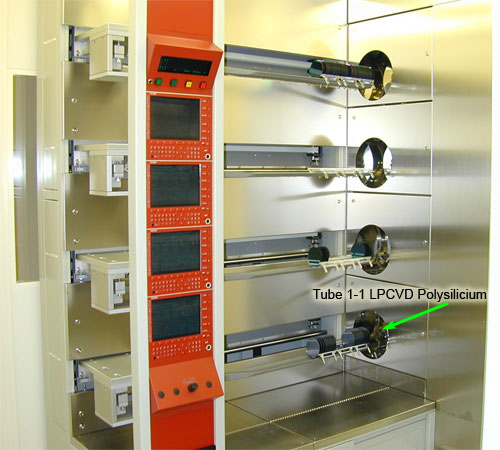
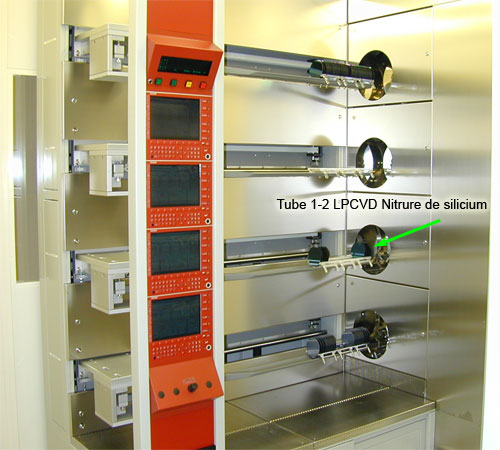
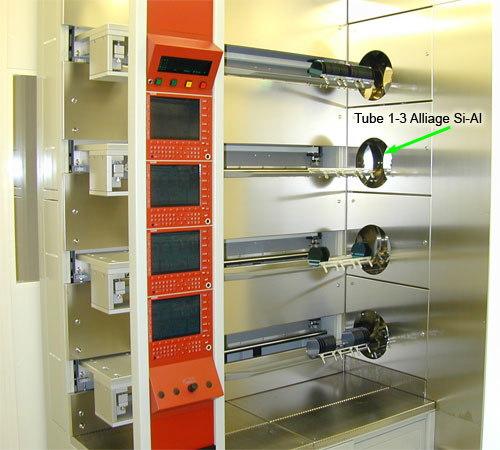
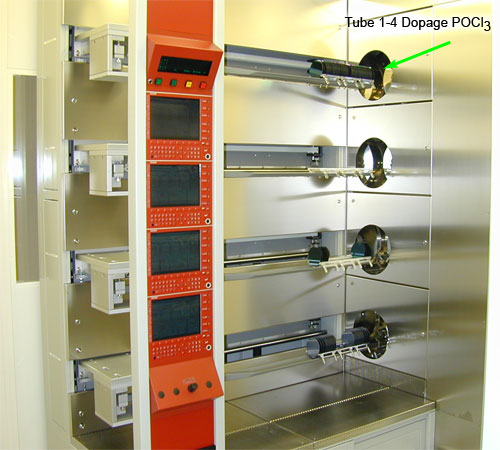
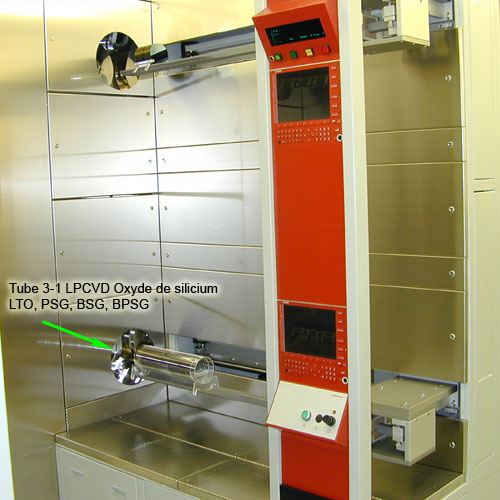

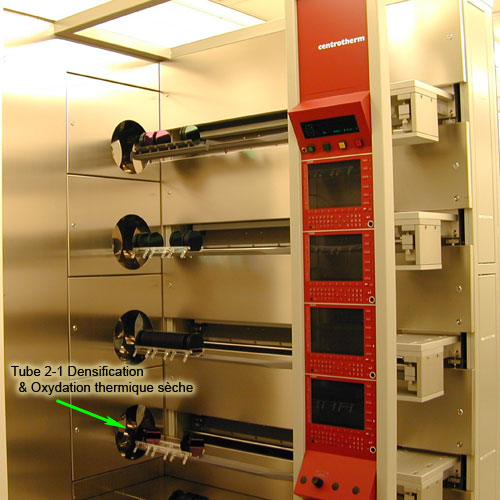
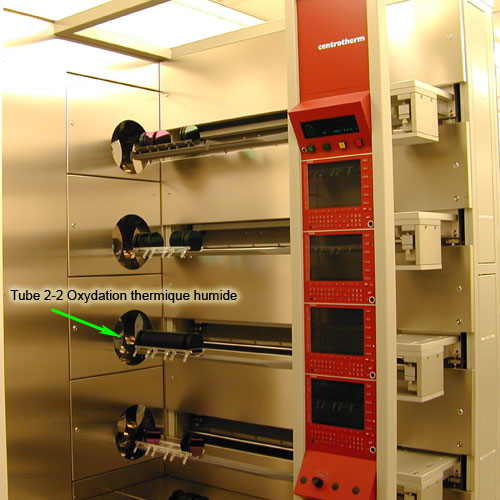
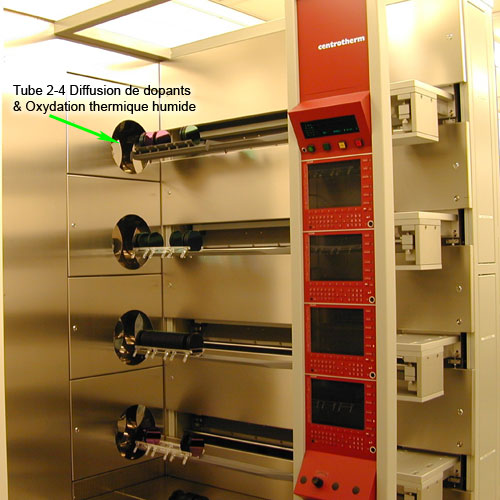
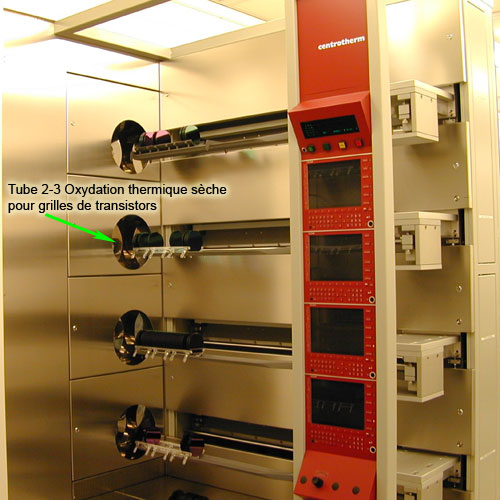
Preliminary and fundamental remarks:
- The Centrotherm equipment is composed of 4 stacks for a total of 15 tubes
- The access is in service mode ONLY, through the RCA cleaning request user interface
- 12/15 tubes are MICRO-ELECTRONIC compatible:
- No organic layers (Photoresist, Kapton, polyimide etc …)
- No metallic layers (Gold, Copper Titane ….etc)
- No float glass samples no pyrex samples
- 1/15 tube (LTO) is MICRO-ELECTRONIC compatible but metal layers (Ti, W, Ta, Al, … etc) are accepted :
- No organic layers (Photoresist, Kapton, polyimide etc …)
- No no microlectronic metallic layers (Gold, Copper … etc)
- No float glass samples no pyrex samples
- 2/15 tubes (Alloy and MEMS) are NOT MICRO-ELECTRONIC compatible but wafers with organic layers on it (Photoresist, Kapton, polyimide etc …) are not allowed
BILLING POLICY :
Billing : Processing time
Contents:
I. Equipement description (General)
IV. Links
V. Gallery
I. Equipment description (General)
The Centrotherm equipment is composed of 4 stacks for a total of 15 tubes. 13 MICRO-ELECTONIC compatible tubes distributed as follows:
- 6 LPCVD tubes (Low Pressure Chemical Vapor Deposition)
- Polysilicon : Tube 1_1
- Nitride : Tube 1_2
- LTO (Low Thermal Oxide) : Tube 3_1
- TEOS ( Tetra Ethyl Ortho Silicate) : Tube 3_2
- Nitride / HTO (High temperature oxide) : 4_1
- HTO (High temperature oxide) / Nitride : 4_2
- 7 atmospheric tubes
- POCL3 : Tube 1_4
- Densification : Tube 2_1
- Wet Oxidation : Tube 2_2
- Gate Oxidation : Tube 2_3
- Diffusion : Tube 2_4
- Wet Oxidation : Tube 4_3
- Diffusion : Tube 4_4
and 2 NOT MICRO-ELECTONIC compatible tubes distributed as follows:
- 2 atmospheric tubes
- Alloy : Tube 1_3
- MEMS : Tube 3_4
All of them are operated by CMi staff only. You can transmit your request through the RCA cleaning request user interface (Step By Step RCA Cleaning Request).
Each tube has 3 heating zones for a better control of the temperature uniformity. Each tube is compatible with 4” and 6” wafers. Samples larger than 1.5 x 1.5 cm2 are accepted but without guarantee regarding the thickness and the uniformity.
II. Presentation by stack
The 15 Centrotherm tubes are distributed in 4 stacks :
Stack 1 (4 tubes):
- LPCVD polysilicon tube (1_1) dedicated to the deposition of polysilicon layers and amorphous silicon layers.
- LPCVD nitride tube (1_2) dedicated to the deposition of nitride and nitride low stress layers.
- Alloy tube (1_3) dedicated to annealing in N2/H2 atmosphere.
- POCL3 tube (1_4) dedicated to the doping of silicon and polysilicon with phosphorous.
Stack 2 (4 tubes):
- Densification tube (2_1) dedicated to annealing of wafers in N2 or the dry oxidation of silicon or polysilicon wafers in O2.
- Wet oxidation tube (2_2) dedicated to the wet oxidation of silicon or polysilicon wafers in O2/H2.
- Gate oxidation tube (2_3) dedicated to the dry oxidation of silicon or polysilicon wafers in O2 with or without DCE for the growth of silicon oxide (SiO2) with a high electrical quality and the annealing of wafers in N2.
- Diffusion tube (2_4) dedicated to high temperature annealing of wafers (above 1050°C and up 1250°C) in N2 or very thick wet oxide (higher than 2.0um) for silicon or polysilicon wafers in O2/H2.
Stack 3 (3 tubes):
- LPCVD LTO (Low Temperature Oxide) tube (3_1) dedicated to the deposition of oxide layers doped (BSG, PSG or BPSG) or undoped oxide (LTO) at 425°C.
- LPCVD TEOS (Tetra Ethyl Oxide Silicon) tube (3_2) dedicated to the deposition of oxide layers at 725°C.
- MEMS tube (3_4) dedicated to oxidation of silicon or polysilicon wafers in O2 or diluted O2 in N2 or in O2/H2 and annealing of wafers and samples in N2 or N2/H2.
Stack 4 (4 tubes):
- LPCVD nitride tube (4_1) dedicated to the deposition of nitride and nitride low stress layers. (Backup tube of HTO tube)
- LPCVD High temeperature Oxide tube (4_2) dedicated to the deposition of oxide layer at 900°C. (Backup tube of nitride tube)
- Wet oxidation tube (4_3) dedicated to the wet oxidation of silicon or polysilicon wafers in O2/H2.
- Diffusion tube (4_4) dedicated to high temperature annealing of wafers (above 1050°C and up 1250°C) in N2.
III. Presentation by process
The Centrothem furnaces are used for the following processes :
- Thermal growth of silicon oxide (SiO2)
- Thermal annealing
- Doping with phosphorous atoms
- Deposition of silicon oxide (SiO2)
- Deposition of Silicon (Si)
- Deposition of Nitride (Si3N4)
Thermal growth of silicon oxide (SiO2)
The thermal growth of silicon oxide (SiO2) can done by 2 techniques, the dry and the wet oxidation. For the dry oxidation, we injectes only pure O2 in the tube at high temperature. For the wet oxidation, we injecte a controlled mixture of O2/H2. The wet oxidation is generally dedicated to thick layer (2000 A or more) because the process is faster (lien process oxidation). The dry oxidation is generally dedicated to thin oxide between 100 to 2000 A for a better thickness control .
At CMi, a dry oxidation can be done in the tubes 2_1, 2_3, 2_4 and 3_4 with a temperature ranging from 800°C to 1050°C depending on the oxide thickness requested but in most of the cases, we use the tube 2_1.
If you need a high dielectric quality oxide for electronic applications, we use the tube 2_3 which is equipped with at DCE bubbler.
If you need a very thick dry oxide, we use the tube 2_4 which is equipped with a set of SiC allowing process temperatures higher than 1050°C and up to 1250°C.
If you need an oxide growth at low temperature, we use the tube 3_4 which has a standby temperature at 200°C and a library of recipes with process temperatures ranging from 120°C to 1050°C. (This tube is not MICROELECTRONIC compatible).
If you need a diluted O2 atmosphere, we use the tube 3_4 which has a library of recipes with O2/N2 1:1 and 1:3. (This tube is not MICROELECTRONIC compatible).
If you need to oxidize a metallic layer in pure O2, we use the tube 3_4 which is not MICROELECTRONIC compatible.
At CMi, a wet oxidation can be done in the tubes 2_2, 2_4, 3_4 and 4_3 with a temperature ranging from 800C to 1050C depending on the oxide thickness requested but in most of the cases, we use the tube 2_2.
If you need a very thick wet oxide, we use the tube 2_4 which is equipped with a set of SiC allowing process temperatures higher than 1050°C and up to 1250°C.
If you need to oxidize a metallic layer in wet O2/H2 atmosphere or in diluted O2 atmosphere, we use the tube 3_4 which is not MICROELECTRONIC compatible.
Thermal annealing
Annealing is a thermal treatment at high temperature under neutral atmosphere as for example nitrogen (N2) or Argon (Ar). At CMi, we use nitrogen and the tubes compatible with temperatures ranging from 700°C to 1050°C are the tubes 2_1, 2_4, 3_4 and 4_4, but in most of the cases, we use the tube 2_1.
If you need an annealing at lower temperature than 700°C, we use the tube 3_4 which has a standby temperature at 200°C and a library of recipes with process temperatures ranging from 120°C to 1050°C. (This tube is not MICROELECTRONIC compatible).
If you need an annealing a higher temperature than 1050°C, we use the tube 4_4 which is equipped with a set of SiC allowing process temperatures higher than 1050°C and up to 1250°C.
If you need an annealing in forming gas N2/H2, we use the tube 3_4 for the process temperatures ranging from 120°C to 1050°C (This tube is not MICROELECTRONIC compatible) or the tube 1_3 for a temperature of 425°C only.
Doping for phosphorous atoms
The tube 1_4 is dedicated to the doping of silicon or polysilicon thanks to the POCL3 process so called because it uses a Phosphoryl Chloride (POCL3) chemistry. The process temperature ranges from 800°C to 1100°C.
Deposition of silicon Oxide (SiO2)
The deposition of silicon oxide (SiO2) is done by LPCVD (Low Pressure Vapor Deposition). At CMi, we have 3 tubes 3_1, 3_2 and 4_2 with 3 different chemistries and to 3 different process temperatures. For some applications, it can be interesting to have doped oxide. This type of deposition can be done in the tube 3_1 (LTO) only.
In the tube 3_1 (LTO), we use silane (SiH4) and oxygen (O2) at 425°C. The additional chemistries are TMB (Trimethylborate) for the deposition of BSG (Boron Silica Glass) and BPSG (Boron Phosphorous Silica Glass) and Phosphine (PH3) for PSG (Phosphorous Silica Glass) and BPSG. The tube is compatible with MICROELECTRONIC metals.
In the tube 3_2 (TEOS), we use Tetra Ethyl Oxide Silicon (TEOS) and oxygen (O2) for the deposition at 725°C. Thanks to a higher temeprature, the conformality of the deposition is better than the LTO one.
In the tube 4_2 (HTO), we use DiChloroSilane (DCS) and nitrogen protoxide (N2O) for the deposition at 900°C. Thanks to a higher temeprature, the conformality of the deposition is better than the LTO one.
Deposition of silicon (Si)
The deposition of silicon (Si) is done by LPCVD (Low Pressure Vapor Deposition) in the tube 1_1. The amorphous silicon is deposted at 550°C and the polysilicon at 625°C from silane (SiH4).
Deposition of silicon nitride (Si3N4)
The deposition of silicon nitride (Si3N4) is done by LPCVD (Low Pressure Vapor Deposition) in the tube 1_2 or in the tube 4_1 with DiChloroSilane (DCS) and Ammonia (NH3). There are 2 qualities of nitride avalaible. The standard Silicon Nitride or stoechiometric Nitride (nit – Si3N4), deposited at 770°C with a ratio DCS/NH3 at 1:6, has a stress around 1150 MPa. The low Stess Silicon Nitride (lsnit – SixNy), deposited at 825°C with a ratio DCS/NH3 at 4:1, has a stress around 250 MPa.
IV. Links
- Available Processes In The Centrotherm Tubes
- CVD Processes In Centrotherm Tubes
- Thermal Processes In Centrotherm Tubes
- Dry Oxidation Curves
V. Gallery
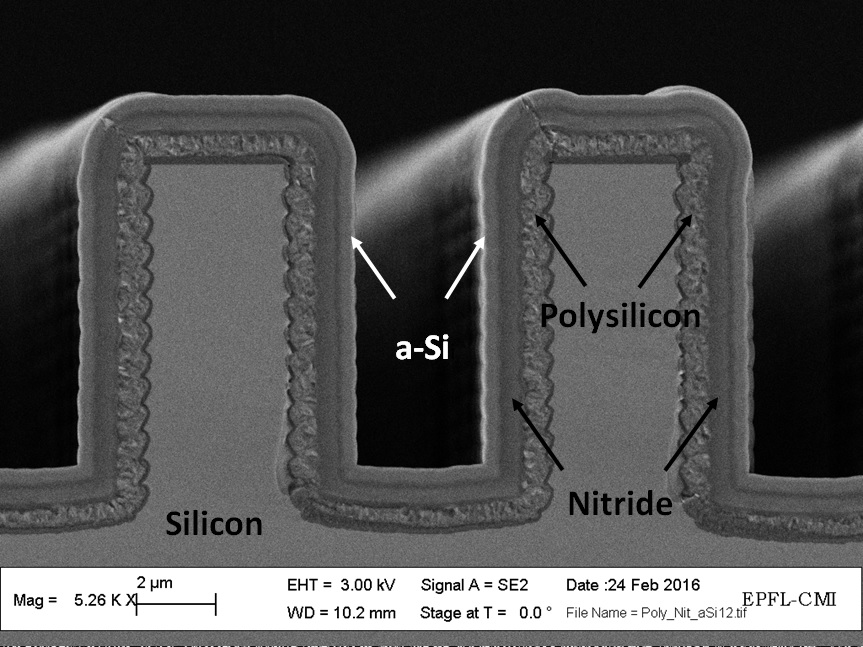
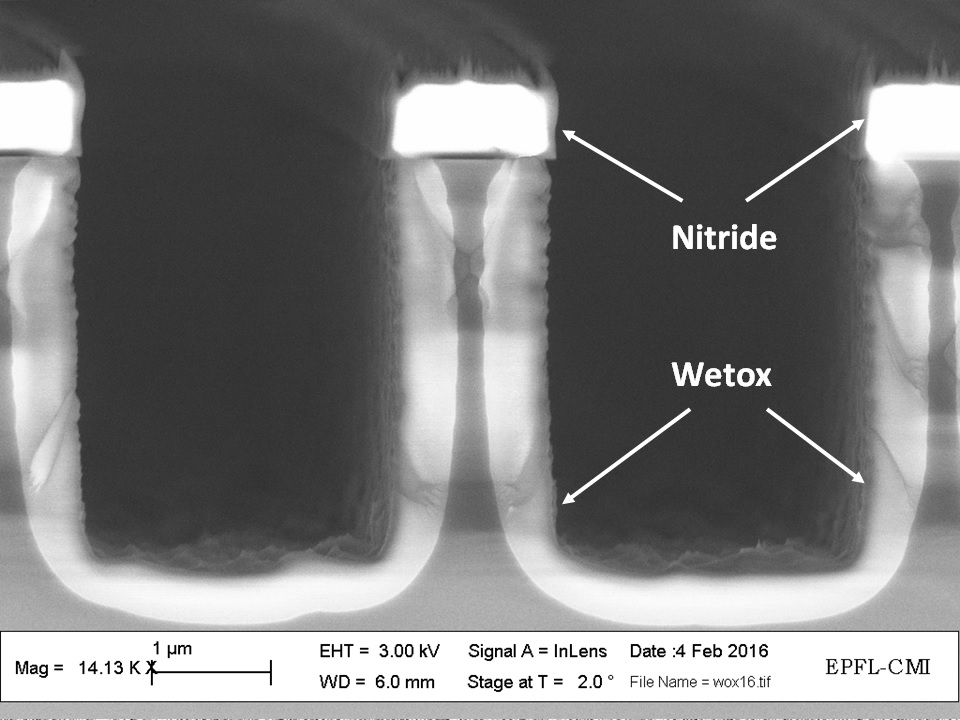
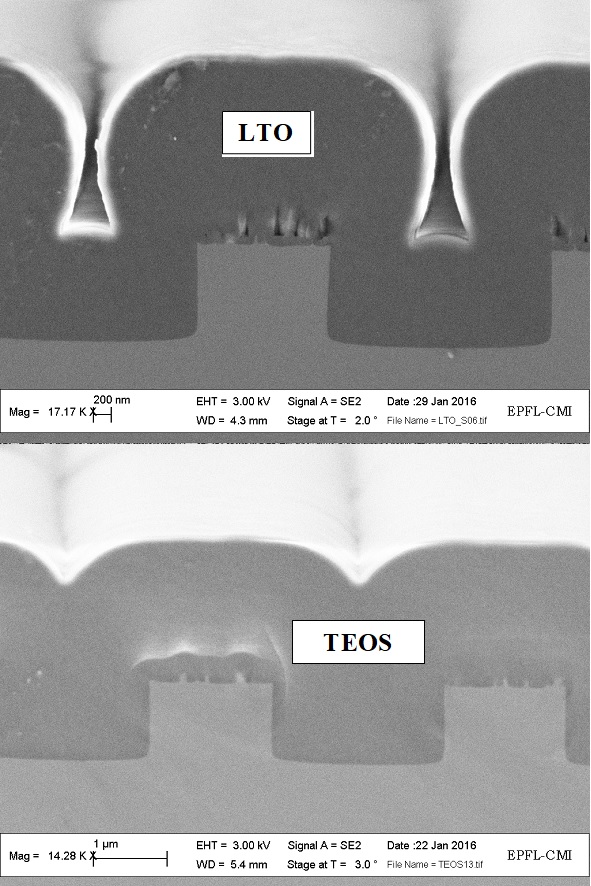
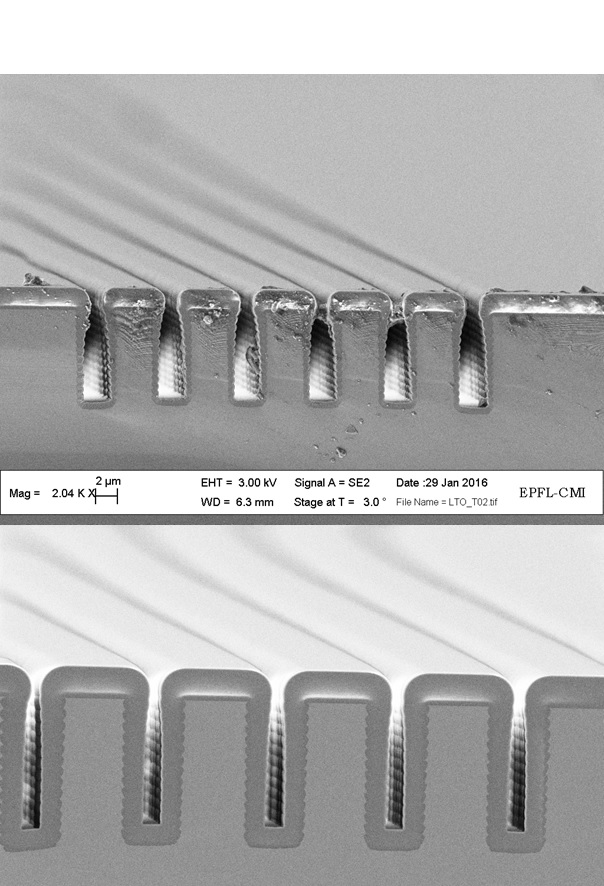
