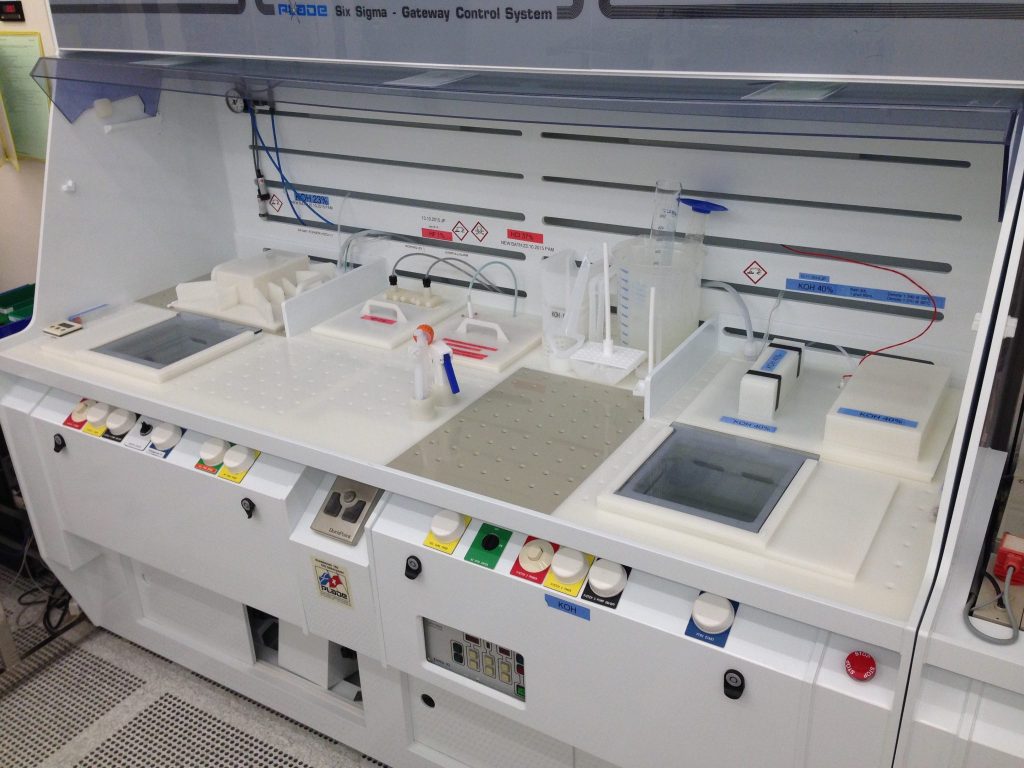
Preliminary and fundamental remarks:
- SAFETY OPERATOR MANUAL TO OPERATE ON CMi WETBENCHES (HERE)
- RESIST IS TOTALLY FORBIDDEN INTO THESE BATHS.
- THE KOH ETCH RATE VARY UPON USAGE: FOR ACCURATE ETCHING PLEASE CALIBRAT IT BEFORE PROCESSING LIVE WAFERS.
Contents
I. Introduction
The KOH is used to etch silicon. Since Si etch rate depends on crystallographic planes it can give an anisotropic etch. For example, <111> planes are etched 200 times slower than <100> planes.
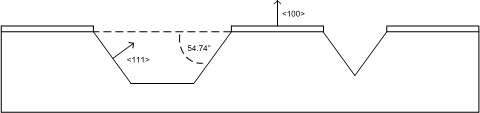
The silicon etch rate depends on crystallographic orientation (wafers/design), silicon doping and bath characteristics (KOH bath density and temperature).
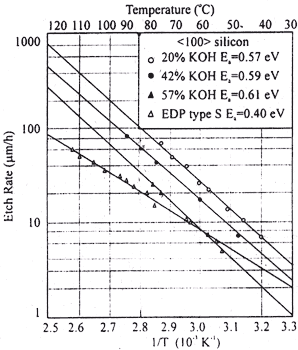
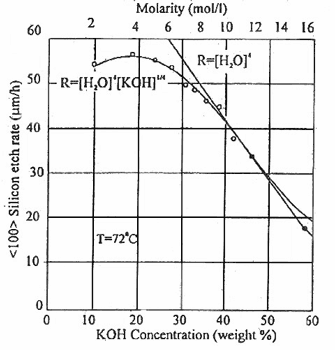
At CMi most of the processed wafers are <100> wafers with a resistivity between 0.1 and 100 Ω.cm, but different kind of silicon wafers can be etched.
II. System overview
Wetbench description:
- KOH bath with heating, circulating pumping and filtering systems.
- 1 dip HF bath (1% HF) to remove native oxide.
- 1 neutralization bath (HCl 37%) required if you have some more process to perform in the cleanroom.
- 2 DI water Fast Fill Rinsers (FFR).
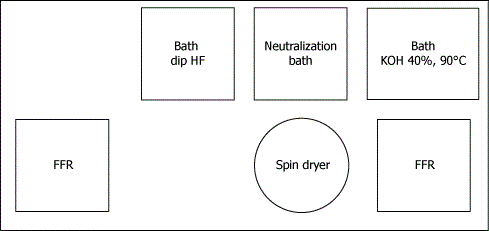
III. Standards at CMi
As explained previously KOH etching is strongly dependent on KOH density and bath temperature. At CMi these parameters have been selected to optimize etching with a minimum of roughness.
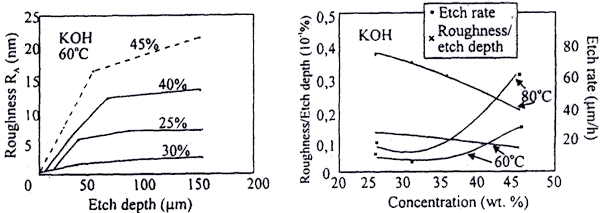
Next table gives the KOH etching bath performance at CMi.
Bath | T (°C) | Si etch rate (um/hour) | Selectivity SiO2/Si | Selectivity Si3N4/Si | Density |
40% | 60 | 21 (+/-2) | 290:1 | > 25000:1 For SiN PECVD Corial: 24 nm/h (SiN_fast) 11 nm/h (SiN_fast10) 26 nm/h (SiN_fast11) 4 nm/h (SiN_slow) | 1.39 1.37 |
IV. Safety
As for the other wetbenches you must respect CMi safety rules: HERE. KOH is a base and neutralization contains strong acid (HCl 37%). When you prepare it, you must be very careful to not spill HCl into KOH! Because of the HCl, it is totally forbidden to put metal into the neutralization bath including metallic chucks!
V. Modus operandi
Full individual protective equipment (PVC apron, face shield and long sleeves gloves) is required to operate on the wetbench.
- Login on Z19 computer (no login = no heating).
- Check the density at room temperature before starting pumping and heating :
- Use the dedicated labelled densimeter.
- The density should correspond with values indicated in previous tables.
- If the density is higher, you may add some water.
- Densimeter rinsing and drying is required once the control is completed.
- Start the circulating pump system.
- Start the heating power (that last ~1 hour for the 40% KOH bath to reach 60°C).
- Once the working temperature is reached :
- Use again the dedicated labelled densimeter.
- The density should correspond with values indicated in previous tables.
- If the density is higher, you may add some water.
- Densimeter rinsing and drying is required once the control is completed.
- You are ready to process your wafers. The etching starts when you see many bubbles coming from Si surfaces (it may take ~1 min to clear native SiO2) . If you really need to use chucks ask to CMi staff for additional information.
- If the processing time is long (hours) then label the bath mentioning your name, phone number and expected end time of the process.
- When the time is up, rinse your wafers and switch off the heating and the pumping systems.
- Neutralization to clear potassium residues is mandatory to continue the process in the clean room:
- Once your wafers / devices are etched and rinse in DI water, put your wafers into HCl 37% bath for 2 hours.
- Remove your wafers and rinse them.
- You may leave your wafers on the wetbench with a labeling to let them dry or you may blow with N2 gun.
- Logout out from zone 19 computer.
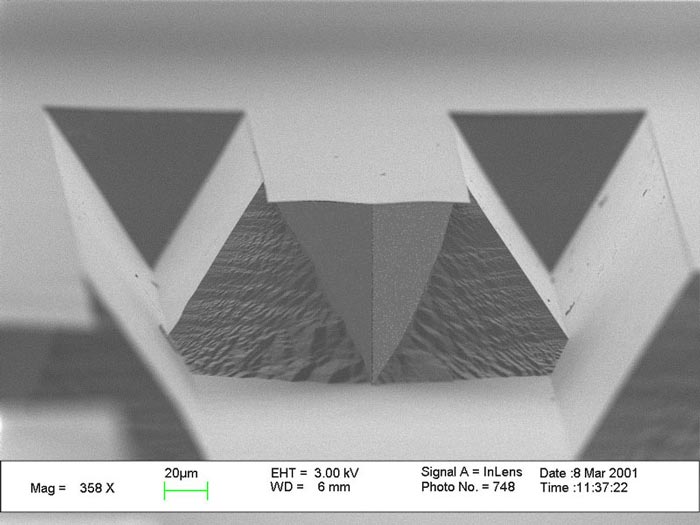
VI. Backside Protection
We have two different chucks to protect one side of the wafers:
- Stainless steel chucks: mechanical clamping to protect front side or back side of any 4” wafers (cf. Figure 7)
- Teflon chucks: mechanical clamping to protect back side of <100> wafers (cf. Figure 8)
If you need to use a chuck, please ask CMi staff for instruction.
You can also proceed with Protek layer spin coating.
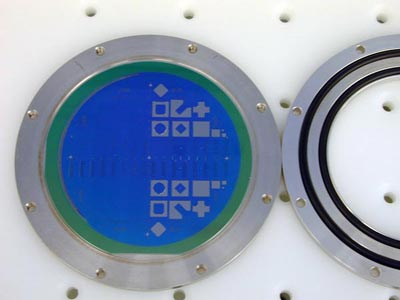
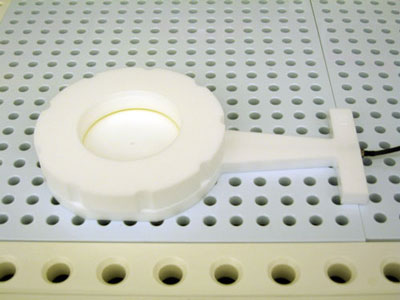
VII. References
M. Madou, “Fundamentals of microfabrication”, p. 168-182, 1997.