CSAR 62 is a positive tone ebeam resist. Main components of the resist are poly(α-methylstyrene-co-methyl chloroacrylate), an acid generator and the solvent anisole. CSAR 62 is used in ebeam mostly as a dry etch mask because it’s more dry etch resistant than PMMA. Its etch resistance, processing and exposure dose is very similar to that of ZEP and as such it can be used as a ZEP alternative.
Polarity
Positive
Doses
Higher sensitivity means lower dose. Typical doses for CSAR 62 are between 160 and 400µC/cm2.
Resolution
CSAR 62 is a very high contrast resist enabling a reasonably high aspect ratio (>15). Resolution should be down to 10nm for isolated features.
Chemical capabilities
For Si CSAR 62 has very good dry etch selectivity with the Si-Opto process on the AMS. For large features you can expect ≈16:1 Si:CSAR62. For SiO2 the selectivity is ≈4:1 with the SiO2 5:1 process. CSAR 26’s wet etch selectivity is similar to PMMA.
WARNING: CSAR 62 tends to leave slightly more residue in large exposed areas after develop than ZEP and typically needs to be slightly more overexposed than ZEP to clear properly (this implies that possibly a slightly larger data bias may be needed if printing to correct size is of importance). Quick oxygen plasma de-scum prior to etching is advisable.
Quick process
There are a few choices but we use n-amyl-acetate for 1-2min for films less than around 300nm, for thicker films it’s best to develop for 2-3mins for make sure you have cleared the resist completely. We use 90:10 MiBK:IPA to rinse immediately after development. This MiBK:IPA solution is also a developer for both ZEP and CSAR 62 so you should be careful when rinsing that you always use the same time for the rinse. Blow dry with Nitrogen.
Before processing choose 2 beakers from the CSAR shelf in the dry cabinet. Rinse one with a small amount of developer (Amyl-Acetate) and the 2nd with the “ZEP rinse solution” (90:10 MiBK:IPA) – we use the same developer and rinse solution for both ZEP and CSAR 62.
Step | Description | Program/Parameters |
---|---|---|
1 | substrate dehydration | 5min of O2 plasma at high power or alternatively 5mins at 180°C on the hotplate |
2 | substrate cooling | 1min |
3 | CSAR 62 coating | see curves below |
4 | CSAR 62 baking | 5min at 180°C on the hotplate |
5 | resists exposure | between 160 and 400µC/cm2 |
6 | resists development | 1-3min into developer Amyl-Acetate on the solvents wet bench |
7 | substrate rinsing and drying | 1min 90:10 MiBK:IPA rinse solution and dry with nitrogen |
When you have finish empty beakers into the solvent waste in the solvent wet bench, rinse the beakers with Acetone and IPA and put them into the ZEP recycle tray at the back of the solvents wet bench.
Spin curves
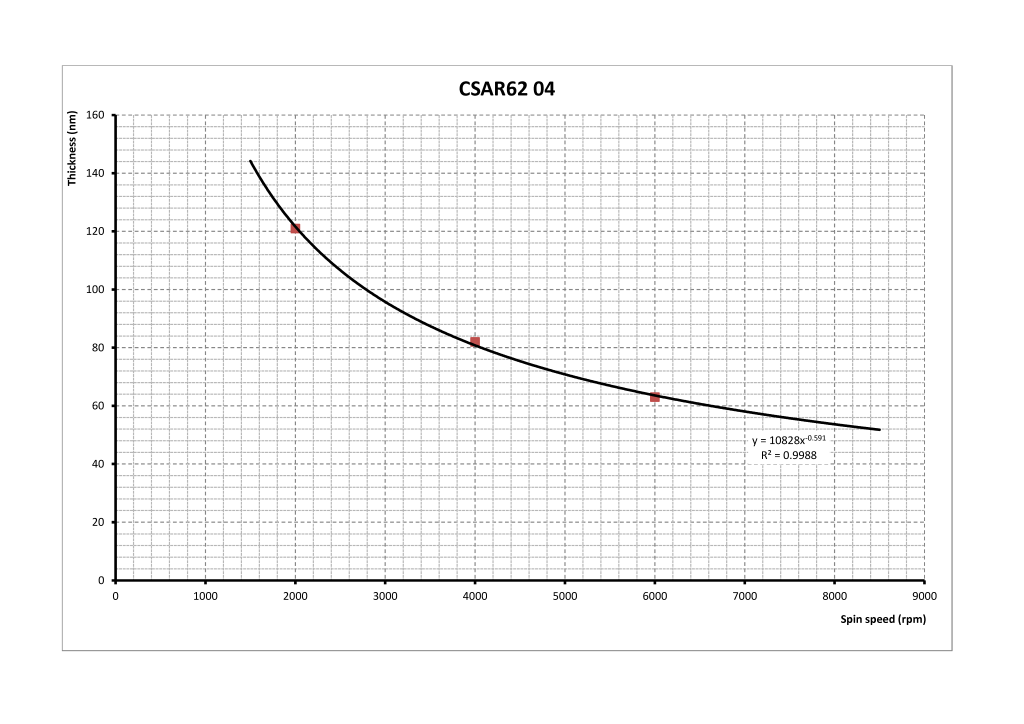
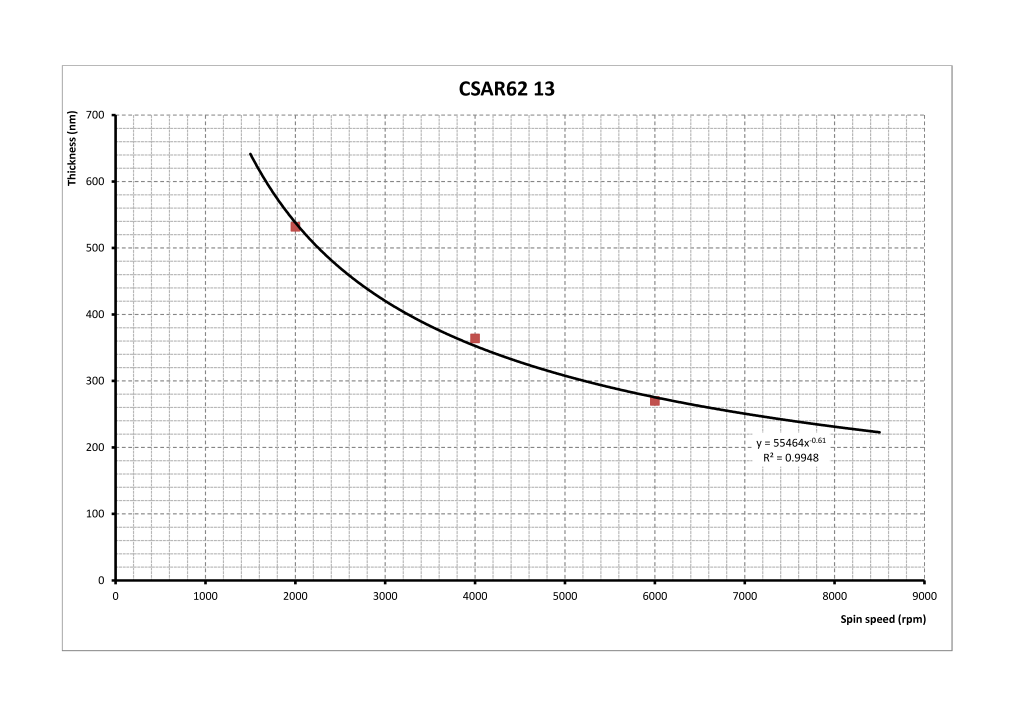