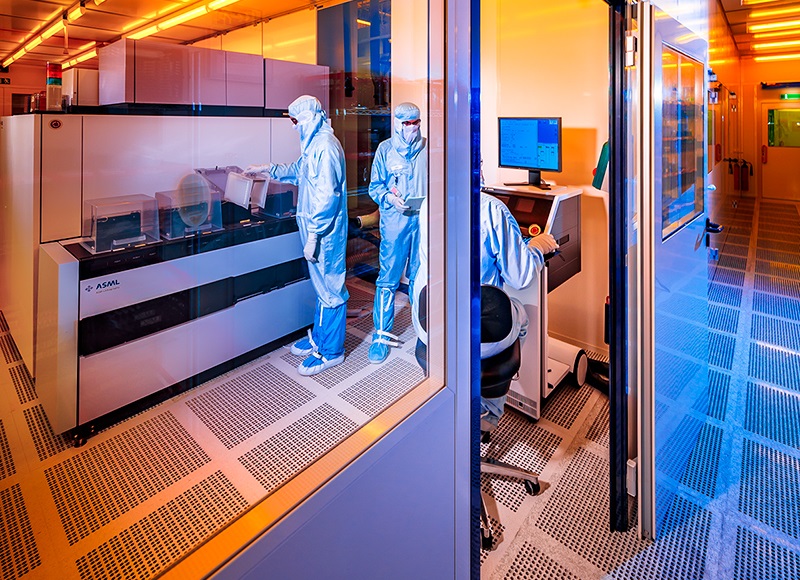
To be read first:
- For DUV lithography process steps with the ASML PAS 5500/350C stepper, CMi recommends to use wafers with the lowest possible total thickness variation (TTV<2 μm) to reduce the impact of of high local thickness variations.
- Wafers exposed on the stepper must have a clean backside. Immediately remove wafers with a contaminated or dirty backside from your batch! Small particles, although not visible by eye, can hinder printing of small features and/or contaminate wafer stage for the next batches. Wafer stage cleaning is a delicate and complex operation which is wearing, time-consuming, and needs re-calibration. Users liable of wafer stage contamination will be billed cleaning hours and may loose access to the machine.
- Projection reticles are sensitive to direct contamination (causing printing defects) and can transfer contamination to the lens top, causing irreversible degradation of printing performance. Do not hover on top of a reticle with hands or body. Use a mechanical pick (available in Z5) whenever possible, or at least chemistry double gloves. Except at load/unload operations, handling and all types of inspection are forbidden on production reticles. Reticles handled for showing, optical microscope check, SEM inspection, and everything else but entering/exiting reticle pods must be considered unusable for production and thus scrapped. For in-house reticle fabrication, users can optimize writing parameters (energy, focus, design bias, etc.) on a 5″ soda lime mask (film stack and resist are identical) that is easy to inspect and then blindly repeat on 6″ quartz plates on the same day.
RESERVATION RULES AND BOOKING FEES POLICY:
- Booking: No booking (CMi service).
- Billing: Job creation ~ 60 minutes, batch exposure ~ 15 minutes + processing time. Advanced jobs and special requirements may be subjected to extra charges.
Contents:
I. Introduction
The ASML PAS 5500/350C stepper is a photolithography equipment, using DUV light from a KrF laser source (248 nm) to expose photoresist through a mask, generally referred as the “reticle”. In opposition to a contact/proximity mask-aligner, a projection lens is interposed between the reticle and the wafer in order to reduce (usually by 4x or 5x) the image of the reticle onto the wafer. A shot through the reticle will expose a small part of the wafer, called the “field”. By stepping the exposure stage and repeating this process, full wafer coverage is obtained.
The ASML PAS 5500/350C was first introduced in the year 2000 and produced until 2010. Its high throughput (> 100 wafers/hour) made it very popular in major semiconductor fabs (Intel, Samsung, TSMC, etc…) producing integrated circuit (IC) chips. Along the years, technology nodes evolution was supported by more advanced technologies (scanners, ArF immersion lithography, EUV) pushing the resolution towards the nm range. KrF DUV steppers are being replaced in fabs, and are often refurbished by the original manufacturers to a second life in companies of the “More than Moore” market, as well as R&D and academic platforms.
The ASML PAS 500/350C installed in CMi can handle 100 mm (default), 150 mm and 200 mm (on request) SEMI standard wafers. It has options to handle transparent wafers, and can perform both topside (< 30 nm accuracy) and backside alignment. The equipment resolution, defined as the smallest line & space pattern that can be resolved and printed in a thin DUV photoresist, is <180 nm (single exposure); isolated lines can be printed with lower dimensions.
PAS 5500/350C is currently operated in service mode by the CMi staff. The jobs for all your alignment and exposure steps will be created and run by the staff under your supervision. Please contact the CMi staff directly to coordinate and prepare your jobs! This section will be updated in due time.
II. Equipment description
Machine overview
The PAS 5500/350C is a complex assembly of different subsystems interacting to shade light in a step-and-repeat way over wafers through one or more reticles. These subsystems include Wafer Handler, Wafer Stage, Level Sensor, Illumination and Projection, Advanced Reticle Management, are briefly described in the following.
- Wafer Handler (WH). This module is the entry/exit point for batches. It consists of four ports: the two left ones are dedicated to single-wafer exchange with an inline track for coating and development (not available). The two right ones are the direct output and the input to the stepper.
(Track IN) (Track OUT) Cassette OUT Cassette IN ↑ ↓ (Track Coater/Developer) Console The WH fetches wafers bottom-to-top, regardless of voids, and returns them in reverse order, filling the output cassette from the top. A shuttle robot is in charge of performing all the needed movement. Before reaching the Wafer Stage, the wafer undergoes centering at the Edge Sensor (an optical prealigner detecting the wafer edge, as well as flat(s)/notch); optionally, the Mark Sensor (camera with optics) can be used to find ASML-specific marks and further increase the accuracy of placement on the Wafer Stage. After exposure, Wafers unloaded from the stage are buffered on a discharge unit (equipped with a realigner) and then moved back to the output cassette.
- Wafer Stage (WS) and Level Sensor (LS). A special arm brings the wafer to the exposure (e-) pins. The arm, called “dipod”, is capable of simultaneously loading a wafer from the prealigner to the e-table and unloading a wafer from the e-table to the discharge unit for the sake of throughput. After loading, pins are lowered and the wafer vacuum-clamped. The WS is made of Zerodur, a material with negligible thermal expansion engineered to allow using multiple sub-nanometer interferometers to exactly know its position. The WS is capable of translation and rotation in the wafer plane (for both stepping and alignment), adjustment of height (wafer-to-lens distance) and tilts (bringing each field in the exact focal plane of the lens). These systems operate in closed loop following the inputs of several measurement system, the most important of which being the LS. By bouncing beams of red and white light between the wafer and the bottom lens, the LS allows wafer (3-points, global) and field (fine) leveling to ensure that the whole projected image hits in focus the resist. After each exposure, the WS smoothly hoovers ~10 μm above a massive granite stone (actively insulated from the rest of the machine) to the next field. The wafer stage can accept 4″, 6″, and 8″ wafers. At the corners of the stage there are the Fiducials (reference markers etched in silicon, allowing to align a reticle with respect to the WS), the Image Sensor (IS, used by the Image Quality Control – IQC to correct machine drifts), and the Spot Sensor (SS).
- Illumination and Projection. Light shot on each field comes from a high energy KrF pulsed laser made by Cymer. The laser cavity, connected to centralized gas distribution (Kr, F, He, Ne), is filled under the control of a computer triggering partial refills at need (even during a batch) and at least a full refill per week (depending on the number of pulses). The beam is generated in the sub-fab and is bent up to enter the stepper. Inside the machine, a group of shaping optics modifies the beam coherency to obtain specific illumination conditions (see Table: Effective σ ranges depend on NA setting; in addition, inner σ range also varies with the chosen outer σ, and cannot be bigger than outer σ).
Conventional Illumination NA: 0.40 … 0.63 σ: ~0.3 … ~0.9 (see note) Annular Illumination NA: 0.40 … 0.63 σout: 0.37 … 0.90 σin: ~0.10 … ~0.60 (see note) A small fraction of the shaped light is constantly collected by the Energy Sensor and used to adjust in real time the number of pulses per shot and hence the dose. Before reaching the reticle, the light goes through the Reticle Masking (REMA) unit. Thanks to four moving metal blades, REMA allows illuminating a specific portion of the reticle for a greater degree of freedom in design. Light passing REMA crosses the reticle down through the lens assembly, a set of more then 15 quartz lenses (height ~1 m, weight ~450 kg) in charge of reducing the image leaving the reticle by a factor 4. The lens, manufactured by Zeiss, features two moving elements used to fine-tune some exposure parameters (focus offset and magnification), also as a function of temperature, humidity, and barometric pressure. Periodically, the whole illumination system is autocalibrated via a test exposure on the Spot Sensor, located on the WS.
- Advanced Reticle Management System (ARMS). This unit is the input for the reticles, the masks for the stepper.
ARMS
Libraries
1, 2, 3
(Track IN) (Track OUT) Cassette OUT Cassette IN ↑ ↓ (Track Coater/Developer) Console ARMS features 3 independent libraries, capable of getting reticles (6″, square, 0.25″/0.15″/0.12″ thick) from exchangeable SMIF reticle pods. Each library can accept pods for single or multiple (6x) reticles, which can be loaded and unloaded anytime using Material Handler section in the PAS Software. ARMS is equipped with a prealigner (to match the reticle table placement accuracy requirements) and a barcode reader (to automatically load reticles needed by a batch). To increase the machine throughput, ARMS has two robots: in case multiple reticles are needed for exposure on a wafer, batch scheduler fetches the next reticle during exposure with the first one, and reticle swap occurs with almost no dead time. One reticle library
- Contamination and Temperature Control (CTC). This module provides all the machine parts with the proper media to keep the environment stable and controlled: forced water circulation for mechanical parts (including the lens jacket), class<10 filtered air with controlled temperature and humidity (air showers and extraction), amine and ammonia filtering (due to the presence of chemically-amplified resists), lens washing gas (N2/1% He).
Wafers:
- Wafer flatness specifications: To be able to print patterns at a resolution < 200nm, the ASML stepper uses a lens with a high numerical aperture (NA) tunable from 0,5 to 0,7. The disadvantage of working with such a lens is that the depth of focus is limited to about ~1um. This means that if, within the exposed field, the wafer surface is located higher or lower than +/- 500nm from the best plane of focus, the printing quality will be strongly degraded. Consequently, to reach optimal critical dimension uniformity (CDU) on wafers exposed with the ASML stepper, it is absolutely critical for wafers to be as flat as possible.
- Wafer back-side contamination: Wafers processed through the ASML stepper are clamped electrostatically to the exposure chuck. Because of this, the presence of particles on the wafer backside will locally deform the surface resulting in similar events to the ones described above (surface locally out of focus). To understand how bad it can be, please have a look at the picture gallery below. Worse: Contamination of the wafer stage can result in a machine downtime of several days. General recommendations to prevent backside contamination: 1) Please use clean wafer boxes / cassettes and do not mix wafers used on the stepper with wafer from other processes. 2) Use cassette to cassette wafer transfer when applicable.When using tweezers, prefer perfectly clean plastic or vacuum tweezers. 3) Make sure to rinse your wafers in DI water baths or SRD systems after each process steps. 4) Make sure to inspect the backside of your wafers after each process steps.
Reticles:
Reticles recommended for the system are the industry standard 6″x6″x0.25″ quartz (ultra-low thermal-expansion) Cr blanks, although 0.15″ and 0.12″ thick plates can also be used. Reticles can include an additional pellicule to protect the chromium side from dust and particles contamination. The reticles (without pellicle) can be manufactured in CMi using the standard mask fabrication flow with the VPG200 and Hamatech equipment, or outsourced to your preferred mask shop such as Compugraphics, Photronics, …
To get you started with the design of your reticle, please use the following documents:
- ASML 4x reticle template (.gds): click here
- CMi 4x reticle visual guide: click here
- ASML 4x reticle guide: click here
At any time, the CMi lithography staff can assist you for the preparation of the reticle layout, the generation of the barcode, and the writing on the VPG200 in case of in-house fabrication
Please read carefully the following design rules:
- The ASML marks (P and MA marks), the barcode and the human-readable code as they appear in the .gds template are with the chromium side of the reticle facing down, as it will be placed in the stepper.
- Your design(s) should fit in the central usable area of the template exactly as they will appear on the wafer, with the same polarity but with dimensions x4.
- The maximum square image size on the wafer is 2.2 * 2.2 cm2.
- In the case where your device unit cells are small, you may be able to place several images (corresponding to different process layers/steps or different designs) on a single reticle, as long as a >3mm Chromium band separates the images.
- The CMi lithography staff will generate the barcode for you.
- For in-house fabrication with the VPG200 and Hamatech equipment, do not forget to activate the “mirror at y” option during design conversion.
Zero-layer exposure:
To be able to reach optimal overlay accuracy (< 30nm) with the ASML stepper, it is necessary to write the zero/first level exposure (that include the ASML wafer alignment marks) on the stepper. Mix & Match with other lithography equipment (direct laser writing, Ebeam,…) is possible but the overlay accuracy specifications will not be guaranteed. Due to this, we recommend to expose the zero-layer (marks only) or first-layer (marks and 1st device layer) using the stepper.
CMi provides two reticles that contains all the alignment marks that are used with other CMi lithography equipment, as well as other designs. This includes:
- ASML stepper alignment marks (PM, XPA, x-SPM, y-SPM,…)
- Ebeam alignment marks, compatible with the Raith EBPG5000+ equipment
- Laser alignment marks (crosses), compatible with the MLA150 and VPG200 direct-writing equipment.
- Mask-aligner alignment marks
- Dicing marks
- Resolution test patterns
- EPFL, CMi logos
This means it is not necessary for you to include any of these marks in your device fields on the reticle. Exposure jobs on the stepper can use the CMi reticles to expose the marks that are needed for your process at the coordinates of your choice.
III. Advanced Alignment Options
The PAS5500/350C features two additional alignment options for advanced applications.
3DAlign (Back side alignment):
3DAlign is a method to perform front-to-back alignment. Backside aligment is widely used in double-side MEMS processing, as well as to overcome process-induced alignment issues in single-side fabrication.
ASML steppers can achieve high alignment using backside markers, which are made visible through a sophisticated periscope system embedded in the wafer table. Thanks to the 3DAlign option, backside alignment can be executed using the same hardware as frontside alignment (TTL).
Due to the working principle of 3DAlign, a maximum amount of 4 backside markers can be defined at fixed backside positions as detailed in the Table below.
Branch | Mark Type | X (mm) | Y (mm) |
B1 | PM (or XPA) | -26.8 | +30.6 |
B2 | PM (or XPA) | +26.8 | +30.6 |
B3 | PM (or XPA) | -26.8 | -30.6 |
B4 | PM (or XPA) | +26.8 | -30.6 |
A minimum of 2 markers is required to perform backside alignment. The Mark Sensor cannot be used with 3DAlign.
In order to maximize the signal used for alignment, markers must be etched 160 nm in silicon.
Technical specifications: 4″ and 6″ wafers only; back-to-back overlay 75nm, front-to-back overlay 200nm (3 sigma).
Athena (Off-axis alignment):
Athena placeholder
IV. User manuals
V. Links
- ASML PAS 5500/350C website
- Cymer website
- Reticle shops: Compugraphics , Photronics , Toppan .