HMDS priming on a Silicon, SiO2, Si3N4 or glass layer will deposit a monolayer of the priming agent with carbon atoms (methyl groups) pointing at the surface. Consequently the wettability of the surface is affected, and turns from hydrophilic to hydrophobic (see images below).
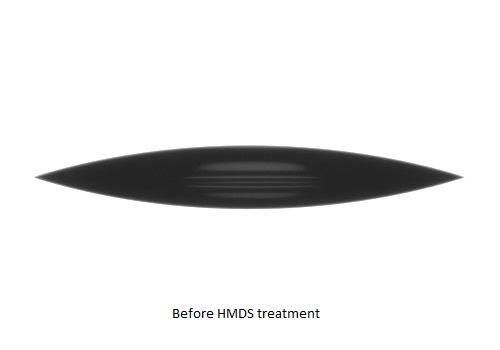
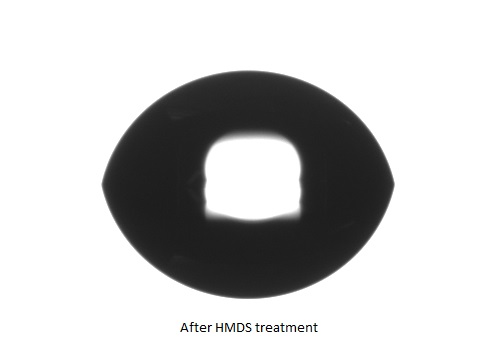
A correct application of the HMDS treatment before spin-coating will insure proper adhesion of the photoresist of the wafer (sillicon, glass).
The simple “droplet test” on the wafer will indicate if the HMDS treatment is effective. A quick video tutorial can be seen here:
Additionaly, the quality of the HMDS treatment can be controlled more accurately using the Krüss DSA-30E contact angle measurement system. After HMDS application, contact angle values between 65° and 75° are expected. Angles < 65° indicate that the HMDS bubbler should be refilled. Angles > 80° are measured after refilling.
HMDS Equipment
The ACS200 Gen 3 automatic coating system in Zone 1 and the Clear Track ACT8 in Z5 have a built-in HMDS hotplate module. For other coating equipments, please use the standalone HMDS primer systems listed here:
- Zone 1: YES III, HMDS primer oven
- Zone 13 : SSE VB20, HMDS primer hotplate
Rework of HMDS-treated wafers:
If you want to remove (strip, rework) the photoresist, use Remover 1165 (Z2 – UFT Remover) or SVC-14 (Z13 – Arias Solvent Wet Bench). ! Note that the standard solvent-based strippers (Remover 1165 [NMP], SVC-14 [DMSO], acetone, IPA) will not dissolve the HMDS monolayer ! To completely remove the HMDS monolayer and clean the surface, either perform an O2 plasma treatment or a short dummy development of the wafers using a standard developer (e.g. 30 sec. in AZ 400K). Alternatively, you can dissolve both the photoresist and the HMDS monolayer using alkaline solution based strippers such as Technistrip P1316.