Contact: Andreas Schueler
Thermal solar collectors exhibit high energy conversion efficiencies and short energy pay back times. A temperature of 80°C is a commonly achieved by thermal solar collectors. According to the Stefan-Boltzmann law, a black body would emit under these conditions some 900 W/m2, which is already in the order of the incident solar energy at ground level. The ideal behavior of an absorber surface is a high absorptance in the solar spectral region and a low emittance in the range of thermal radiation, which implies a step-like reflectance spectrum with R = 0 in the solar region and R = 1 in the infrared range. A surface approaching this property is called optical selective. In addition to these optical requirements, a solar absorber coating has to withstand elevated temperatures and humidity inside the collector during a lifetime in the order of 25 years.
Advanced nanocomposite coatings are developed for glazed collectors aiming at high optical performance and superior aging stability. Promising novel highly durable materials are titanium containing amorphous hydrogenated silicon carbide films (a-Si:C:H/Ti) produced by a vacuum plasma process [OEL205](see Fig. 1), and nanocomposite ceramic coatings of the spinel type produced by low-cost sol‑gel dip-coating [KRA2022b](see Fig.2). Both materials are interesting alternatives to the traditional black chrome coating, which is still in use today, and whose production is based on a highly toxic Cr(VI) precursor.
A chromium-free black selective coating for durable selective solar thermal absorbers has been developed in the framework of Dr Martin Joly’s PhD thesis. As compared to the most durable solar absorber coatings today, the novel black selective nanocomposite coating has the advantage of a highly superior stability at elevated temperatures in air, combined with an improved corrosion resistance[JOL2013], [JOL2015]. Its remarkable properties make the novel nanocomposite coating especially interesting for solar thermal electricity generation in large-scale solar power plants and industrial process heat in the temperature range from 170°C to 600°C, using concentrating parabolic trough solar collectors (see Fig. 3).
Patent WO 2014045241 A2, published 27.3.2014 (Industrial partner Zettl GmbH, Munich, Germany) Method for hardening a coating of a solar collector element, and elements produced by means of said method
PhD thesis in this domain
Martin Joly, Développement et optimisation de revêtements nanostructurés pour capteurs solaires thermiques et modules photovoltaïques, EPFL PhD thesis 5541,2012 (thesis director Prof. J.-L. Scartezzini, codirector A. Schüler)
Publications
[JOL2013] Joly, M., Antonetti, Y., Python, M., Gonzalez, M., Gascou, T., Scartezzini, J.-L., Schüler, A., Novel black selective coating for tubular solar absorbers based on a sol–gel method, Solar Energy 94 (2013) 233–239
https://doi.org/10.1016/j.solener.2013.05.009
[KRA2022b] Krammer, A., Lagier, M., Schüler, A., In-line electronic and structural characterization of reactively sputtered Cu-Co-Mn black spinel oxides, Journal of Vacuum Science and Technology A: Vacuum, Surfaces and Films, 2021, 39(5), 053411. https://doi.org/10.1116/6.0001120
[OEL2005] P. Oelhafen, A. Schüler, Nanostructured Materials for Solar Energy Conversion,
Solar Energy 79, 110 (2005)
https://doi.org/10.1016/j.solener.2004.11.004
[JOL2015] Joly, M., Bouvard, O., Gascou, T., Antonetti, Y., Python, M., González Lazo, M.A., Loesch, P., Hessler-Wyser, A., Schüler, A., Optical and structural analysis of sol-gel derived Cu-Co-Mn-Si oxides for black selective solar nanocomposite multilayered coatings, Solar Energy Materials and Solar Cells, 143, pp. 573-580 (2015)
https://doi.org/10.1016/j.solmat.2015.06.058
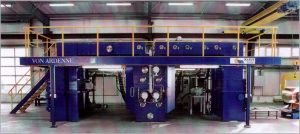
Fig. 1: Upscaling of vacuum/plasma deposited selective absorber coatings to industrial production. The vacuum deposition equipment has been dimensioned to an annual production of about 200 000 m2/yr of solar collector surface. (IKARUS Coatings, VIESSMANN) [OEL2005].
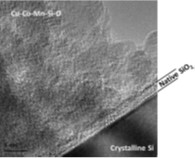

Fig. 2: Pollution-free low-cost sol-gel deposition of nanocomposite selective solar absorber coatings. The sol-gel process will be an interesting alternative to vacuum deposition processes, which require high initial investment costs (due to the expensive equipment as shown in Fig. 1, and traditional electroplating (“black chrome”), the latter based on highly toxic Cr(VI) compounds and today accused to heavily pollute the environment.
Top: High resolution transmission electron microscopy HRTEM of a spinel Cu–Co–Mn–Si spinel oxide thin film produced by pollution-free low-cost sol-gel dip-coating at EPFL/LESO-PB [JOL2015].
Bottom: The reflectivity of a trilayered spinel based sol-gel coating is low where the spectral intensity of the solar spectrum is high, and is increasing towards larger wavelengths in the infrared. Such a selective absorber coating has a high solar absorptance and a low thermal emittance [JOL2013].
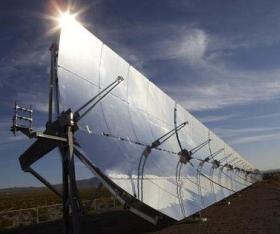
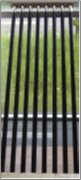
Fig. 3 : Thermoelectric power generation by combining parabolic trough mirrors with coated solar absorber tubes.
Top: The parabolic trough mirrors focus the incoming solar radiation onto the absorber tubes. Typical temperatures around 400°C are reached. The heat is used for steam generation and subsequent electricity production.
Bottom: Array of prototype receiver tubes produced at LESO-PB with the novel sol-gel process based on induction heating. The tubes measure 2m in length [JOL2013].