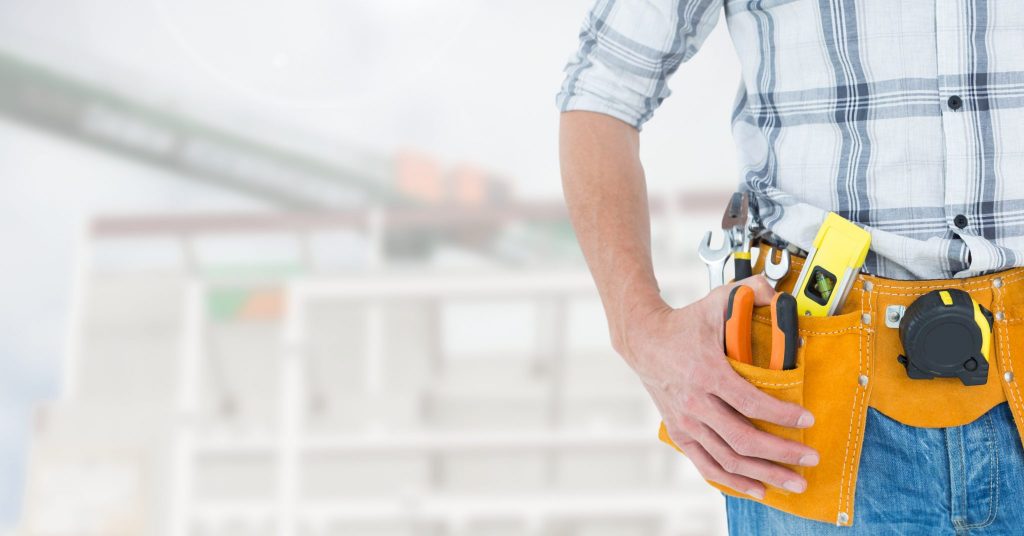
When choosing and acquiring the different common laboratory equipment, according to the list below, all SV units are required to contact our technical support through the workshop’s ServiceNow form, before any order request is placed. This procedure allows to homogenize the equipment of the School, optimize maintenance, obtain the best after-sales service, reduce costs for the research laboratories, as well as to use more environmentally friendly equipment.
Standard equipment requiring validation by the technical referent for their acquisition
- 4°C Refrigerators
- -20°C and -80°C Freezers
- Liquid nitrogen tanks
- Ice machines
- Incubators and C02 incubators
- Climatic chambers
- Ovens
- Autoclaves
- Shakers/incubators
- Washers
- H2O purifiers
- Air treatment equipment
- Biological safety cabinets, laminar flow hoods, gloveboxes
- Chemical chambers
- Centrifuges
- Scales
- pH meters
- Cell counters
- Cell crushers
- Spectrophotometers
- PCR equipment
- Electrophoresis gel imaging equipment
- Benchtop equipment (vortex, shakers, etc.)
- Basic microscopes
Once the chosen equipment is validated by our services, the unit forwards the necessary information for the purchase to the administrative team of the SV Infrastructures, according to the procedures concerning the purchase of scientific equipment which can be found on this page.