DLL Molecular – Chemical engineering
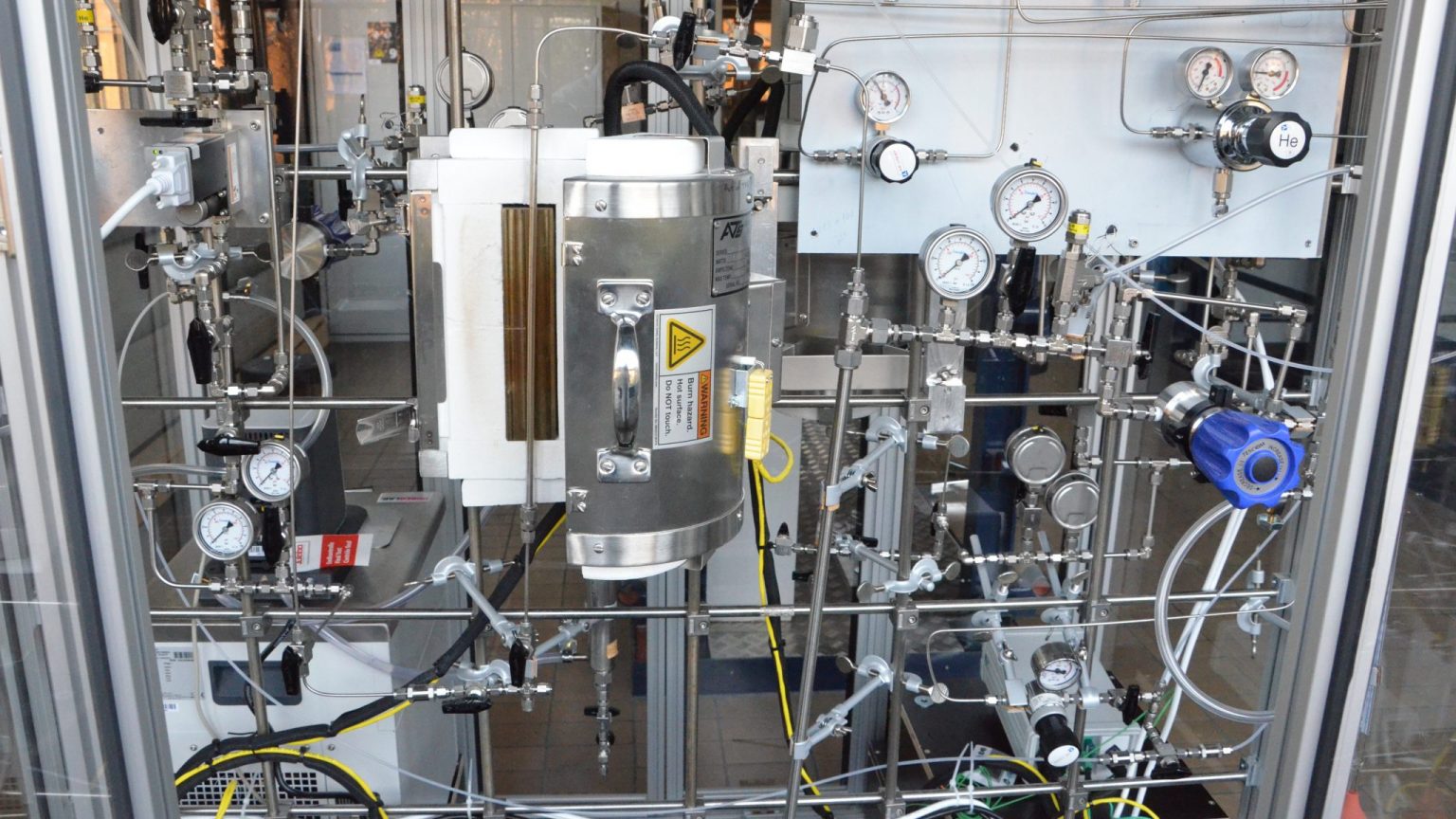
Flow reactor
By definition, chemical engineering -or physico-chemical process engineering- refers to the application of physical and synthetic chemistry on an industrial scale.
In this chemical engineering laboratory you can find the main facilities that can be found in industry but on a smaller scale. These allow the operation of the various fundamental processes of chemical engineering to be explored and understood.
These facilities are located in a three-storey hall and can be classified in the following categories:
- Energy Conversion (fuel cell, photovoltaic, heat pump)
- Separation (crystallisation, filtration, continuous distillation, liquid-liquid extraction, double-effect evaporation)
- Continuous Reactors (Catalytic flow reactor, Residence Time Distribution, Microreactors)
- Batch reactors (parametric sensitivity)
- Heat transfer (heat exchanger, conduction, free and forced convection)
- Mass transfer (oxygenation of water)
- Fluid mechanics (hydraulic pressure drop)
- Process control (level control of a tank)
Facilities
Gas chromatography (GC) is a technique for separating molecules from a mixture that may be very complex and of a wide variety of natures. It is mainly applied to compounds that are gaseous or can be vaporised by heating without decomposition.
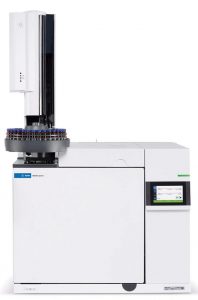
This system is used to determine the distribution of crystal sizes.
Available: 10 sieves with different opening widths
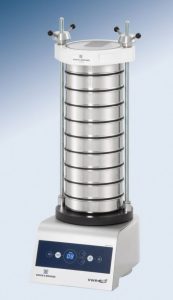
Coupled with a computer with software for the acquisition and processing of spectra. In addition, 4 glass and 2 quartz cells (optical path = 10 mm).
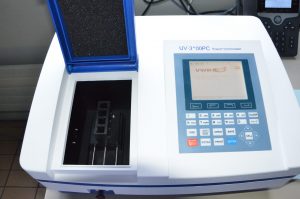
Heat exchangers (tubular, double tube, plate) are an essential component of industrial chemical plants and commercial appliances.
This module consists of a base unit that will supply heated water at controlled flow rates to each of three heat exchangers, all equipped with temperature sensors.
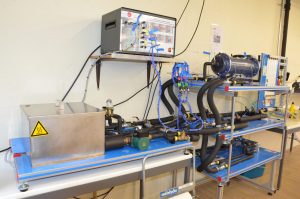
One of the fundamental concepts in chemical engineering is the flow of a fluid between two points. When a real fluid (with non-zero viscosity) moves through a pipe, frictional forces arise. These can only be evaluated by empirical methods.
In this installation, the flow can be visualised using a coloured tracer as a function of the fluid velocity in metres per second. The pipe has an internal diameter of 16 mm and a length of 1710 mm. The flow rate can be set between 50 and 250 L/h. Using this data, the Reynolds number can be calculated and the type of flow determined:
– Laminar (a): The liquid moves with a parabolic shape and a maximum velocity is reached in the centre of the tube.
– turbulent (b): the liquid swirls and moves at almost the same speed over the entire cross-section of the tube.
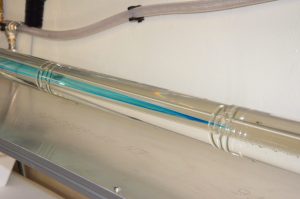
This equipment consists of a hermetic compressor connected to a condenser and an evaporator designed to work as a heat pump. It consists of a heat transfer fluid that passes from a condenser to an evaporator in a closed circuit and a compressor that provides work to the fluid. In the condenser, the fluid condenses and releases heat that can be used to heat water. In the evaporator, the heat transfer fluid evaporates and absorbs heat, thus cooling the water.

Understanding how the energy from our largest renewable energy source, the Sun, can be converted and used is essential for a modern chemical engineering programme.
This test bench offers measurement possibilities on two solar panels of 0.45 m2 each. It will also be possible to produce an operating voltage of 20 Volt in parallel and 40 Volt in series.
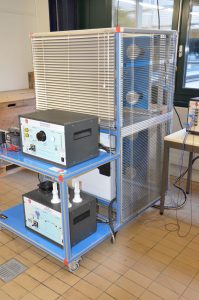
Continuous chemical reactors are the basis of chemical engineering and examples are numerous in biochemical engineering, pharmaceutical and fine chemical industries. The hydrolysis reaction of ethyl acetate in the presence of sodium hydroxide can be studied. However, the system is also suitable for studying other reactions, such as those of acetic anhydride hydrolysis.
The first reactor is a continuous stirred tank reactor
The first reactor is an isothermal stirred tank reactor (CSTR), while the second is a tubular reactor (ISF). The third reactor system is a serial CSTR.
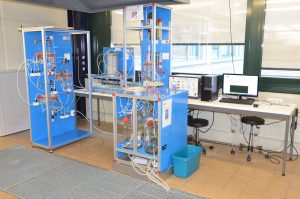
Fuel cell, which converts hydrogen and oxygen to water while converting excess energy into electricity, is an important device in a free fossil energy economy.
This device can quantify the change in enthalpy and entropy.
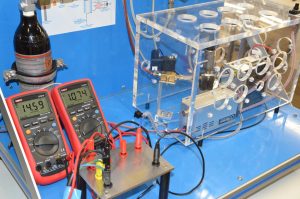
Crystallisation is a solid-liquid separation technique that consists of isolating a product in the form of crystals.
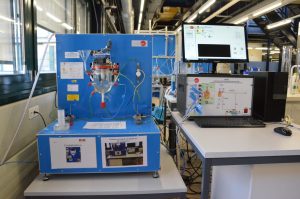
Conduction is another way of dominating heat transfer. This is material specifically designed to demonstrate the principle of heat transfer by conduction rather than by convection or radiation.
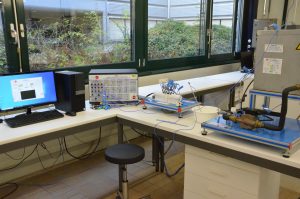
In this installation, a fluidised bed is formed with glass beads of different diameters in a 44 mm diameter Plexiglas tube. The introduction of a fluid into the tube will create a solid/liquid mixture that will behave like a fluid. The resulting phenomenon is called fluidisation.
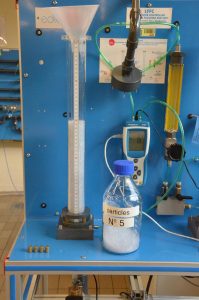
A wet film absorption column (or wet wall gas) consists of a vertical tube through which a liquid descends, while a gas rises, both separated by an interfacial film. This process is usually used to study mass transfer between two components in two different phases.
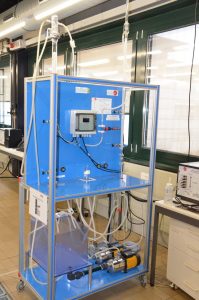
The equipment, which consists of a computer controlling a tank filled with water, allows process control.
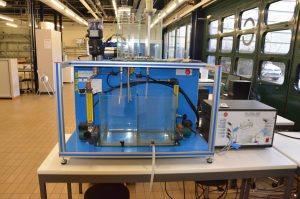
Filtration is a common solid-liquid separation operation used in industry that requires empirical data to make performance predictions. The filtration module allows the study of the filtration process on a vertical plate filter, composed of 0.5 micron diameter nylon plates. This finally allows the filtration of CaCO3 from the suspension of known concentration.
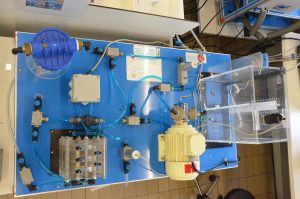
Heat transfer at a solid-liquid interface occurs not only by conduction, but also by convection. The design of heat exchangers is driven by an understanding of these two phenomena.
The system consists of a stainless steel tunnel with a rectangular cross-section supported by an anodised aluminium structure that allows it to be adjusted on a worktable. In the tunnel, the blade exchanger will be used.
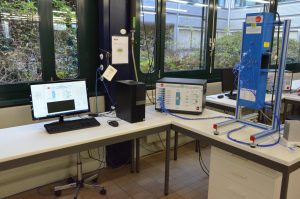
Continuous distillation is a separation constant in which a mixture is continuously introduced into the process and the separated fractions are continuously removed as output streams.
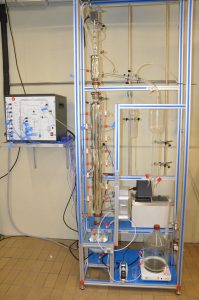
The multi-effect evaporator is a device for the efficient use of heat from water vapour.
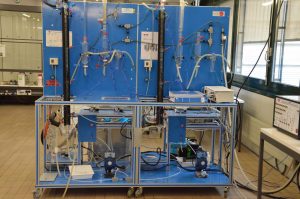
This experiment measures the residence time of a chemical component on 3 different systems:
– 3 tubular reactors
– 1 reactor of 3 L
– 3 reactors of 1800 mL arranged in series
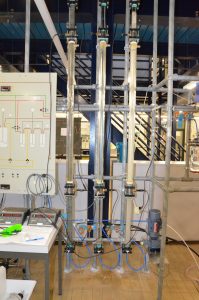
The main interest of micromixers lies in their high transfer capacity. By adapting the geometric dimensions of the reactor to the transfer requirements of the reactions, micromixers allow particularly demanding reactions (fast reaction rates, high exothermicity, hazardous chemicals) to be carried out safely. They also open up new synthesis routes and improve the sustainability of processes.
This installation consists of the following elements
– double syringe pump with pressure measurement
– 3 different micromixers
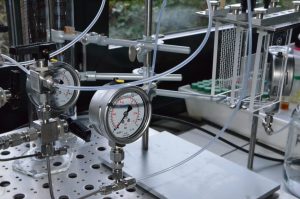
Location and safety regulations
These facilities are located in a three-storey hall in the CH building:
CH C0 396, CH C1 396, CH C2 396
Anyone who wants to handle chemicals needs to be instructed according to the safety regulations of EPFL, DSPS and the internal regulations of ISIC/SCGC.
Training and bookings
Julien Andres, +41 21 693 74 55
Activities and courses
Course | Description |
ChE-203 | TP-1, TP-2, TP-3, TP-4, TP-5, TP-6 |
ChE-309 | TP-1, TP-2, TP-3, TP-4, TP-5, TP-6, TP-7, TP-8 |
Master 1 | Distillation en continu |
Master 2 | Extraction liquide |
Master 3 | Evaporateur à double effet |
Master 4 | Temps de résidence dans un réacteur |
Master 5 | Micro mélangeurs |