We have developed HAXELs: hydraulically amplified zipping electrostatic actuators, less than one millimeter in thickness, designed for seamless integration in textile-based haptic interfaces for Virtual Reality (VR) and Augmented Reality (AR) scenarios.
For virtual reality (VR) to be truly immersive, the sense of touch must be stimulated. Our “HAXELs” can deliver a rich sense of touch on fingers, or anywhere on our skin. Our initial version of HAXELS, published published in Advanced Materials in 2020, was less than 1 mm thick, changes in thickness by 60% in under 5 milliseconds, and generates 0.5 N of force. They are very lightweight, only 90 mg each, and can easily be incorporated in clothing. We now have fully printed versions (Advanced Functional Materials 2023) that are fully stretchable, that can be wrapped around a fingertip. We can scale the HAXELS from 2mm up to 20 mm on a side, with forces of up to 4 N.
HAXELs are capable of both of out-of-plane and in-plane motion, thus providing normal and shear forces to the user’s fingertip, hand or arm, with high spatial resolution.
Combined with our textile brake, we develop thin and low-power haptic gloves that make virtual objects feel real, yet allow for complete freedom motion of the hand.
Row-column addressing can be used to address arrays
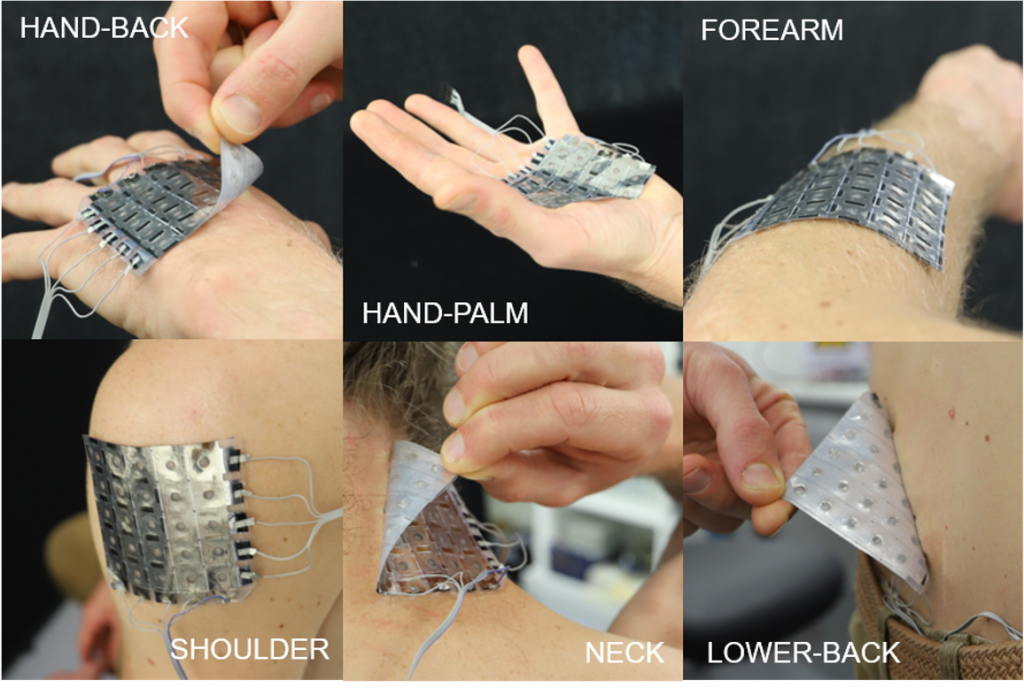
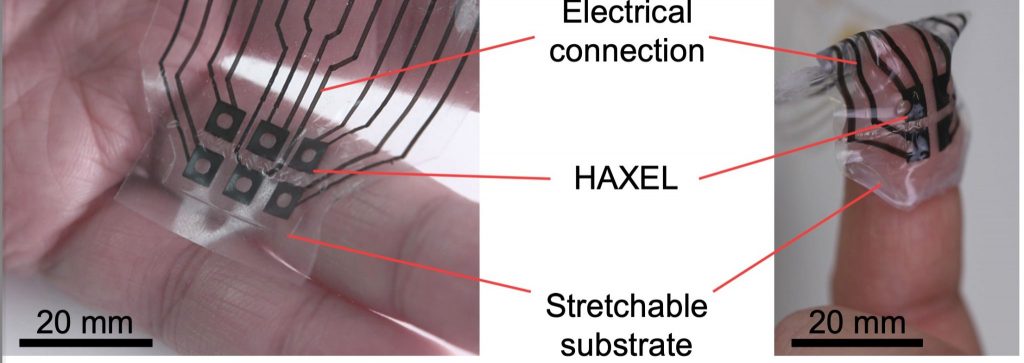
How do HAXELs work?
Each HAXEL consists of a fluid-filled cavity whose shell is made of a non-stretchable polymer in the outer regions and of a stretchable elastomer for the central region. Electrodes are patterned on both the top and bottom polymer shells. When a voltage is applied to the annular electrodes, they are pulled together by Maxwell pressure, starting to zip at the outer regions where the electric field is highest. As the top and bottom polymer regions are pulled together, the fluid is rapidly forced into the central stretchable region, forming a raised bump. We obtain very high power density (>100 W/kg) and very high force density (3300 N/kg).
HAXELS are electrically controlled. No compressor or pressurized air source is needed, greatly adding to device portability, and enabling completely silent operation.
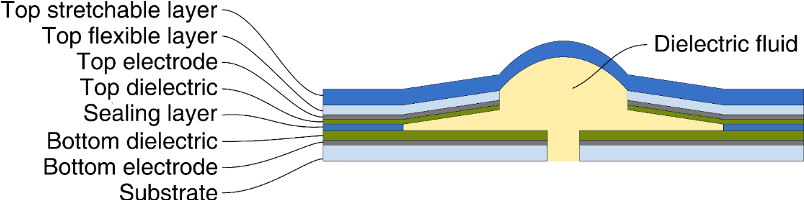
Shear force and normal force
We use our fingers to identify objects by sliding our fingertips over them. We can tell if if a glass is about to slip out of our hand by sensing shear forces. Simulate this in VR requires being able to generate normal and shear forces with high spatial resolution.
By segmenting the HAXEL electrodes, we can make the central bubble not only pop out of plane, but also move side to round, around, up and down… This enables us to use only one HAXEL to provide rich range of haptic feelings.
Testing on volunteers showed that both the normal and in-plane motion was easily felt and correctly identified. The device can generate static strain as well as vibro-tactile signals up to several hundred Hz.
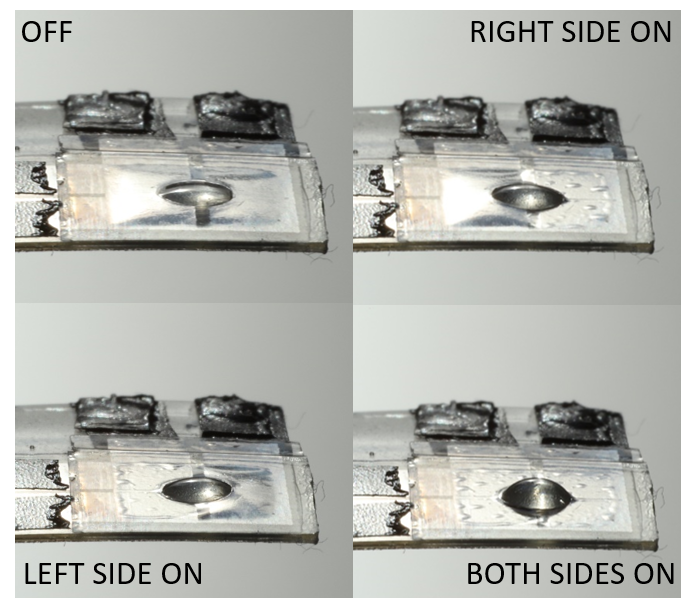