Fiber pumps
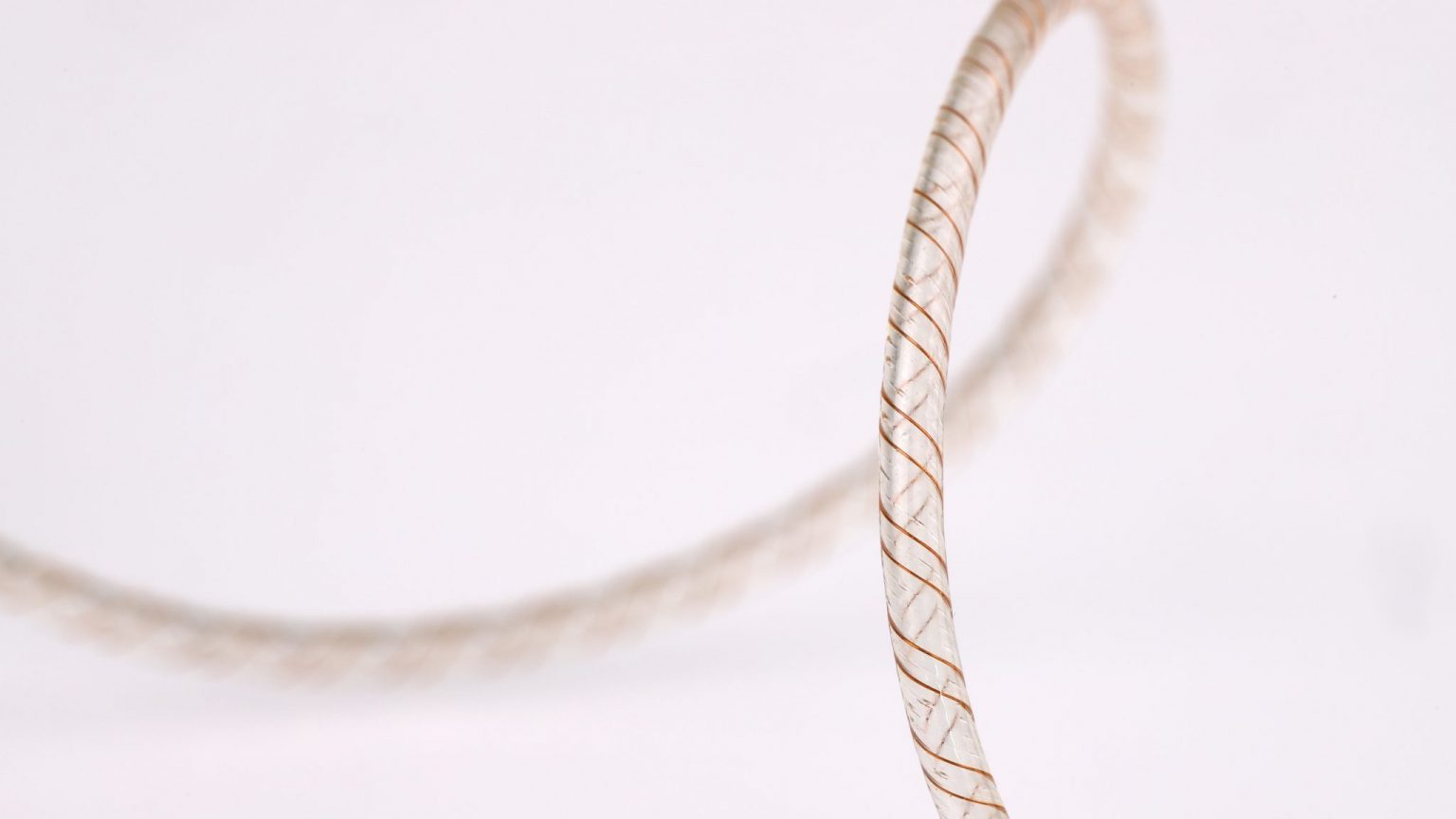
LMTS, in collaboration with researchers at Politecnico di Bari (Italy), have developed a fluidic pump in the form of a stretchable and flexible fiber.
These pumps allow high pressure fluidic circuits to be seamlessly integrated into textiles and clothing, enabling devices like thermoregulatory clothing and soft supportive exosuits.
The research was published in Science in March 2023.
Fiber pumps for wearable fluidic systems
When it comes to creating wearable devices, fiber-based technology has many advantages. Fibers are flexible, scalable and are already compatible with conventional textile production techniques like weaving, knitting and sewing.
Fiber-based versions of many electrical and mechanical components already exist, but before this work, there were no fiber-based fluidic components beyond basic tubing and connectors.
This was a limitation, since fluidic systems can be very useful for wearable devices – devices like clothing that can actively regulate temperature, or medical orthoses that adapt to the users’ form to provide compression and muscular assistance when necessary.
Previously, these devices were reliant on a large, rigid and un-wearable compressors. With the fiber pumps, we can sew the pump directly into the fabric of these devices, leaving the rigid pumps behind.
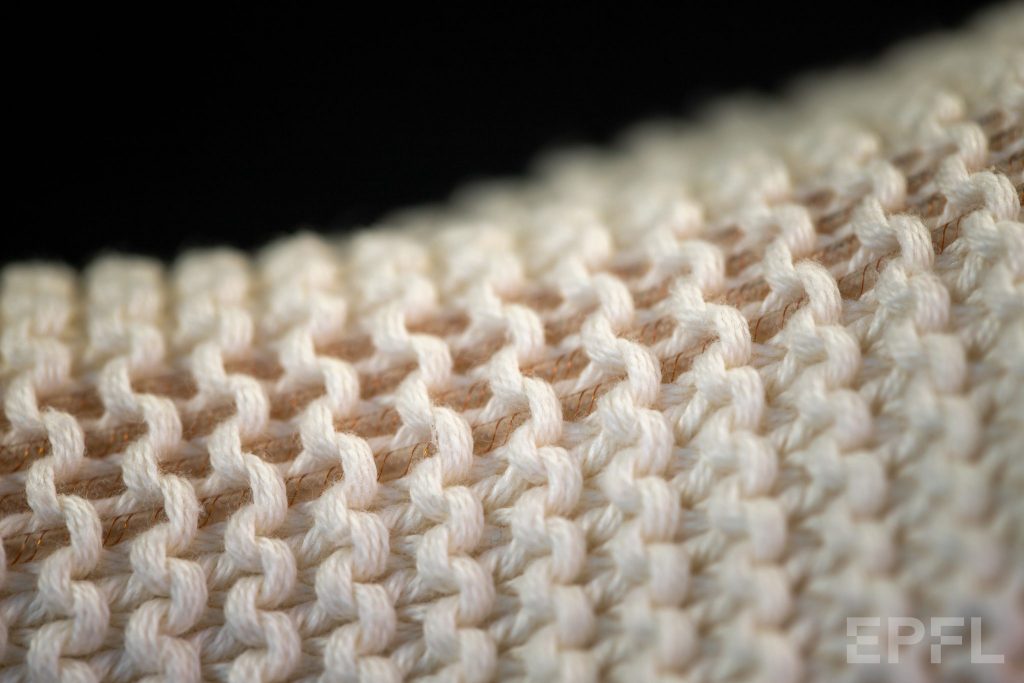
What are fiber pumps? How do they work?
The fiber pumps consist of a thin elastomer tube, about 2 mm in diameter, with two helical copper electrodes winding around the inside walls. Applying a high voltage between these electrodes ionises and accelerates the dielectric liquid within the tube, creating a net flow of fluid.
This pumping mechanism is referred to as charge-injection electrohydrodynamics (EHD). It is an established technique, but had never before been realised in a thin, flexible fiber.
The output of the pumps scales with their length. Need twice the pressure? Use twice the length! Each meter of pump generates 1 atmosphere of pressure (100 kPa), and flowrates exceeding 50 ml/min are also possible. Given that each meter of fiber weighs only 1 g, the pumps deliver exceptional performance per unit weight – within a factor of two of class-leading rigid micropumps.
This performance is maintained even as the pumps are stretched and bent – and even washed!
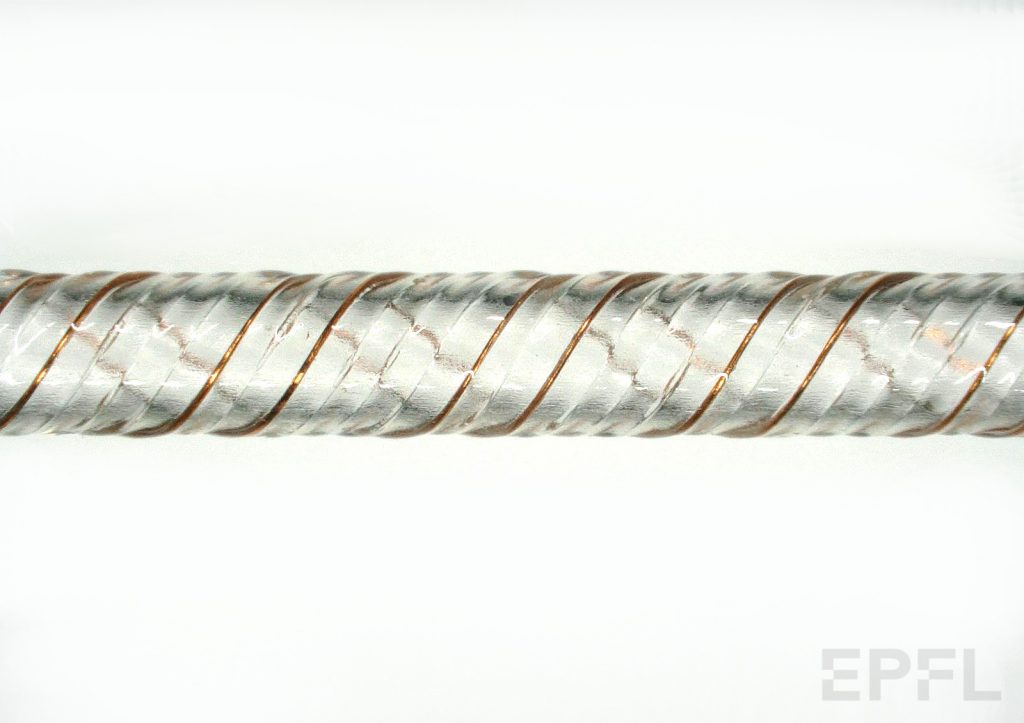
How are fiber pumps made?
Fiber pumps are made using a filament winding method. This creates the pump body and electrodes at the same time, and ensures that the electrodes remain exposed along the inside wall of the tube. This is crucial to allow the injection and collection of charge required for charge-injection electrohydrodynamics to operate.
The process involves twisting together copper wires and polyurethane threads, and then fusing the structure together with heat. The video below gives a brief overview of the process. More details can be found in the paper and supporting movies (link below).
Temperature regulation with fiber pumps
Fluidic systems are often used for thermal management. Fiber pumps allow liquid cooling systems to be seamlessly and efficiently integrated into clothing. These kinds of cooling systems require long lengths of tubing to act as a heat exchange. With fiber pumps, the tubing is the pump! This leads to very simple fluidic circuits without the need for external pumps.
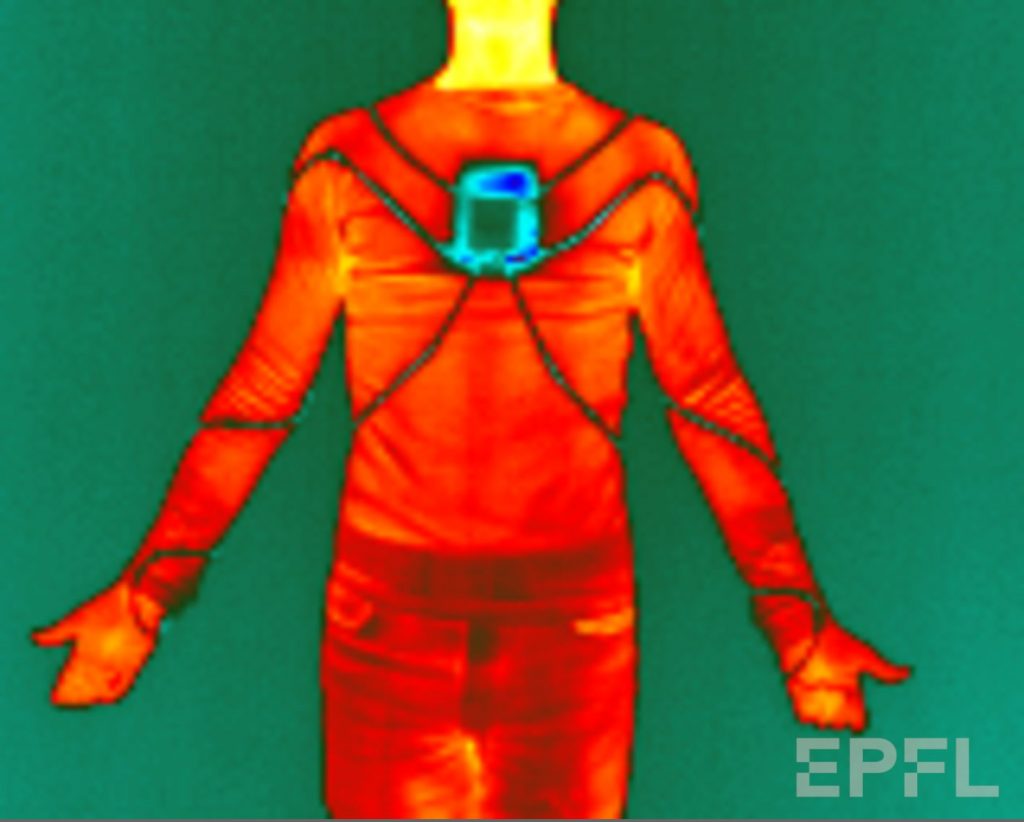
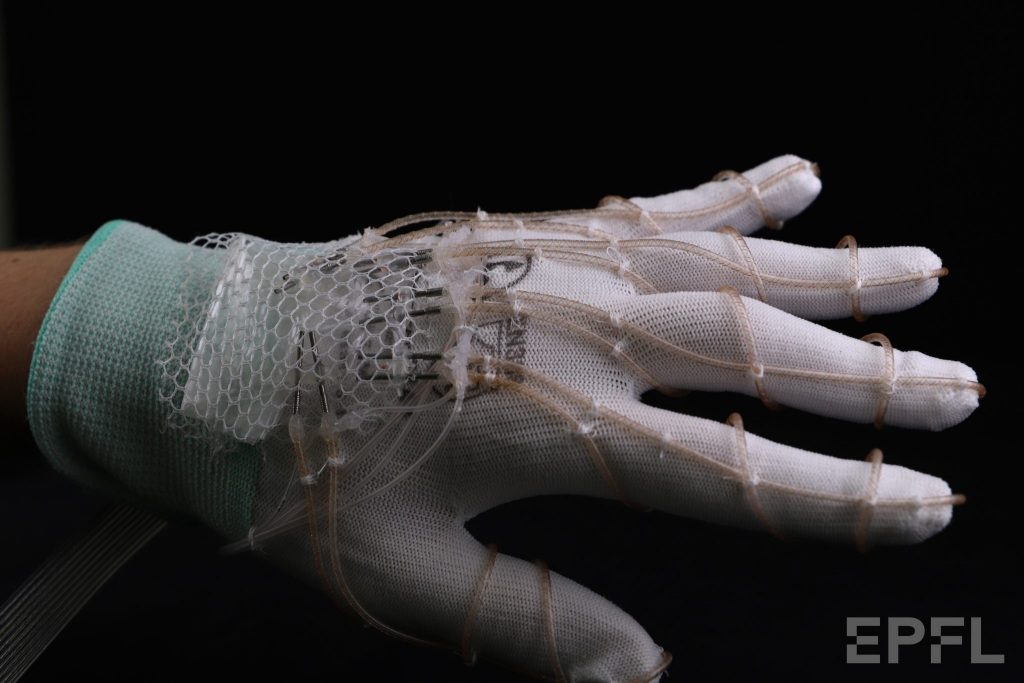
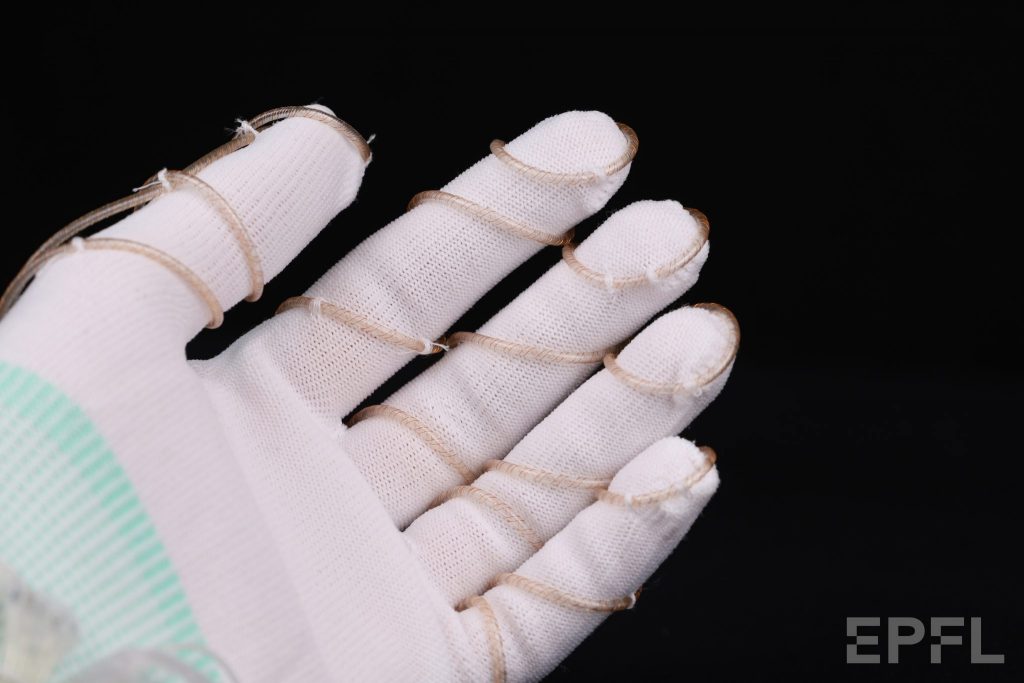
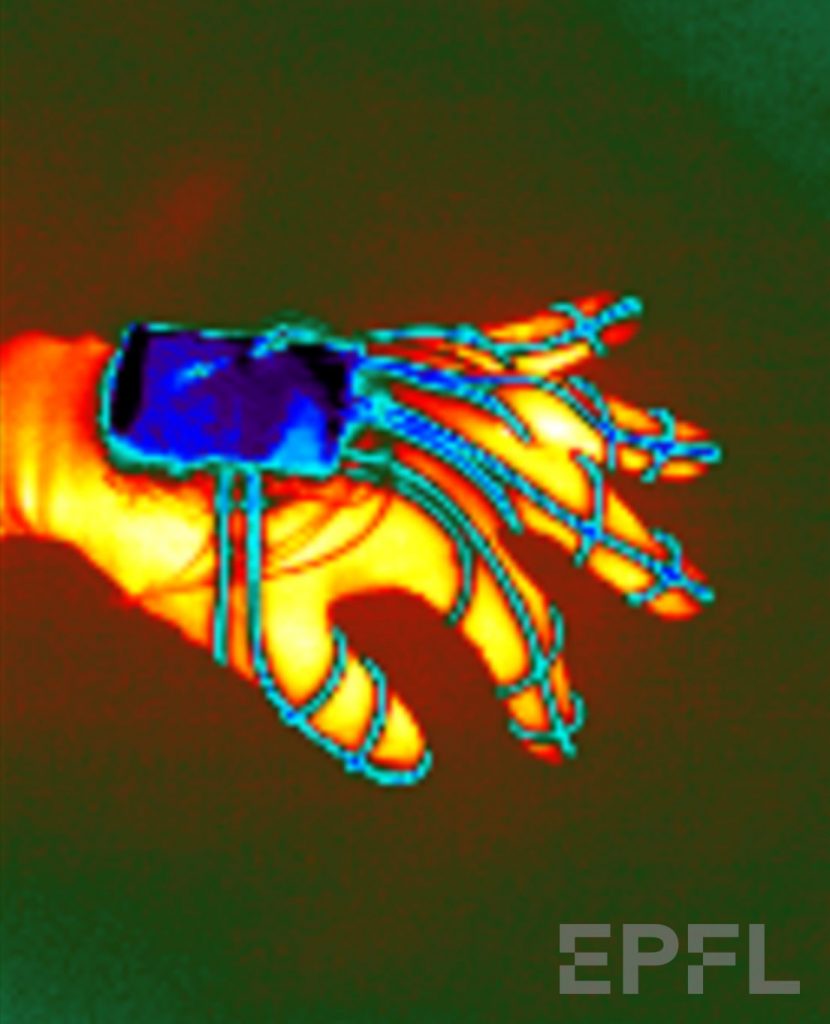
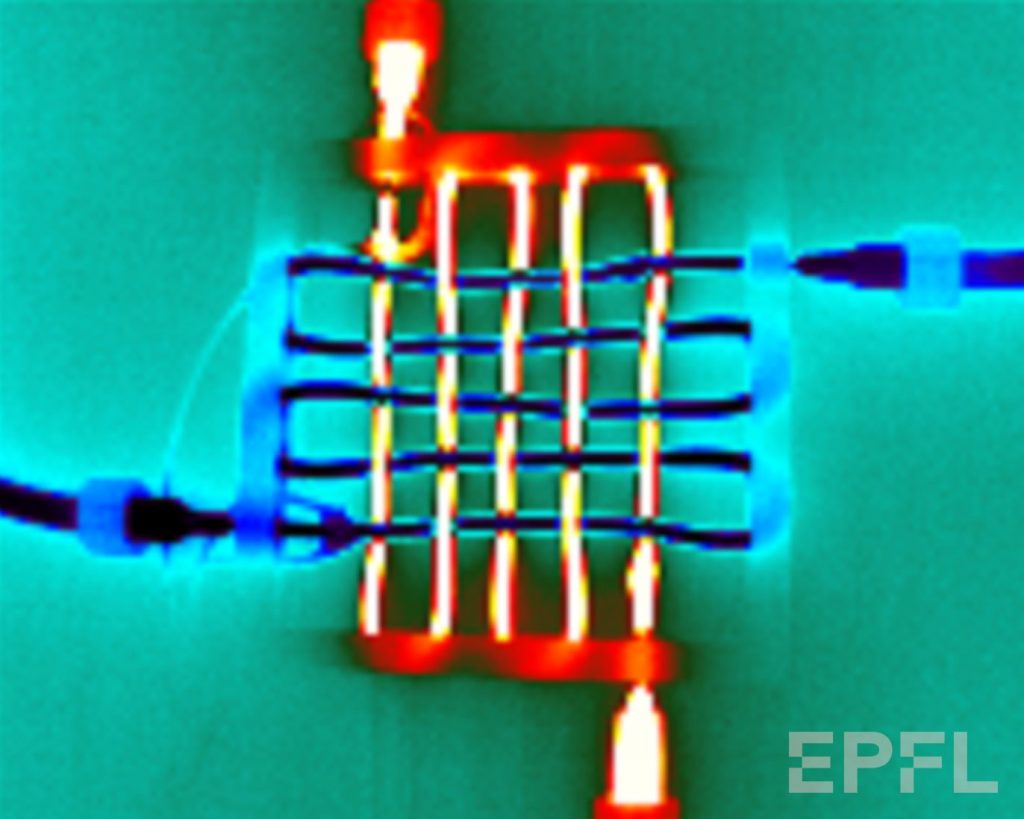
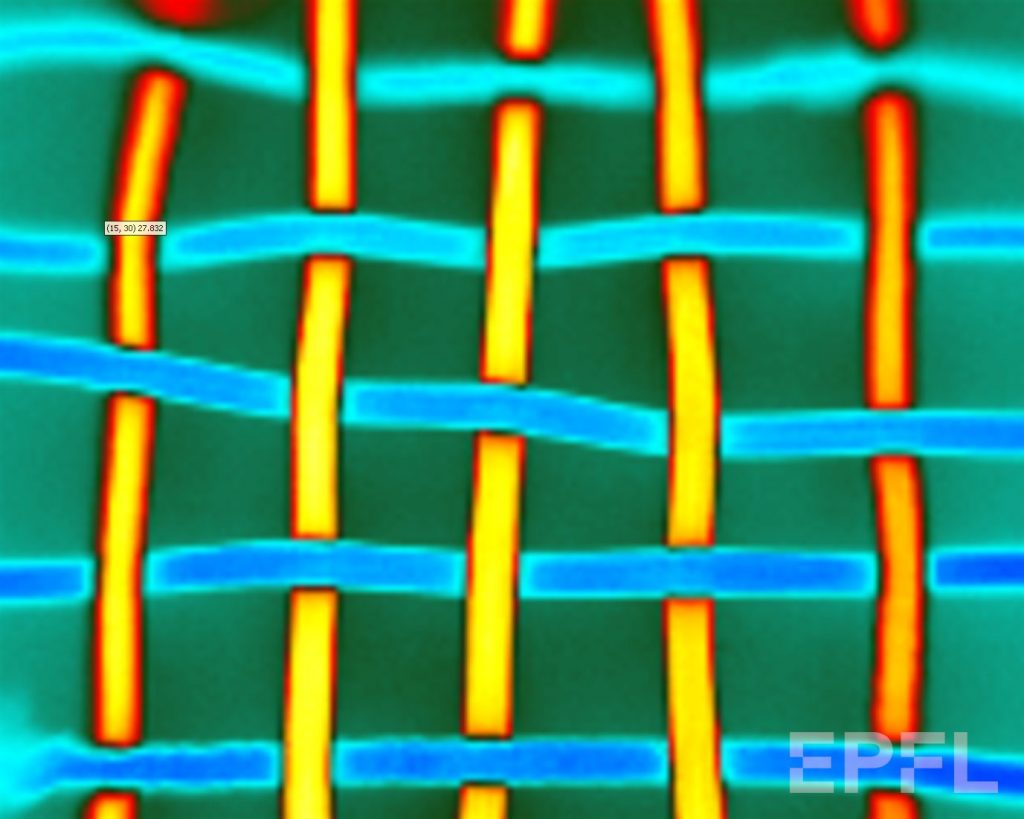
Actuation with fiber pumps
Fiber pumps can be combined with textiles to create fabric-based artificial muscles. A silicone bladder sewn between two pieces of cotton fabric expands and contracts under the pressure supplied by the embedded fiber pump. When used in a garment, these kinds of actuators can be used to provide compression or muscular assistance.
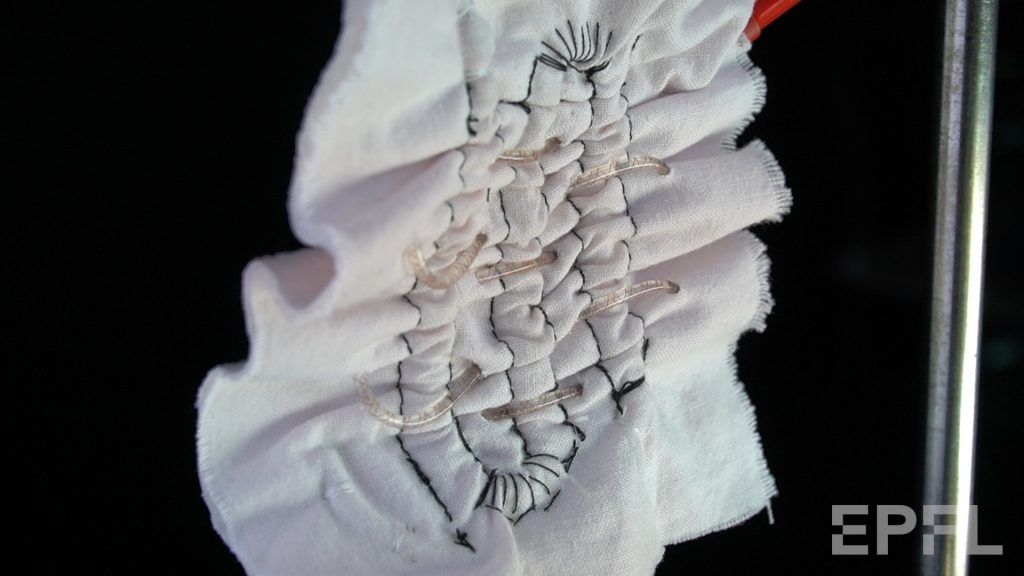
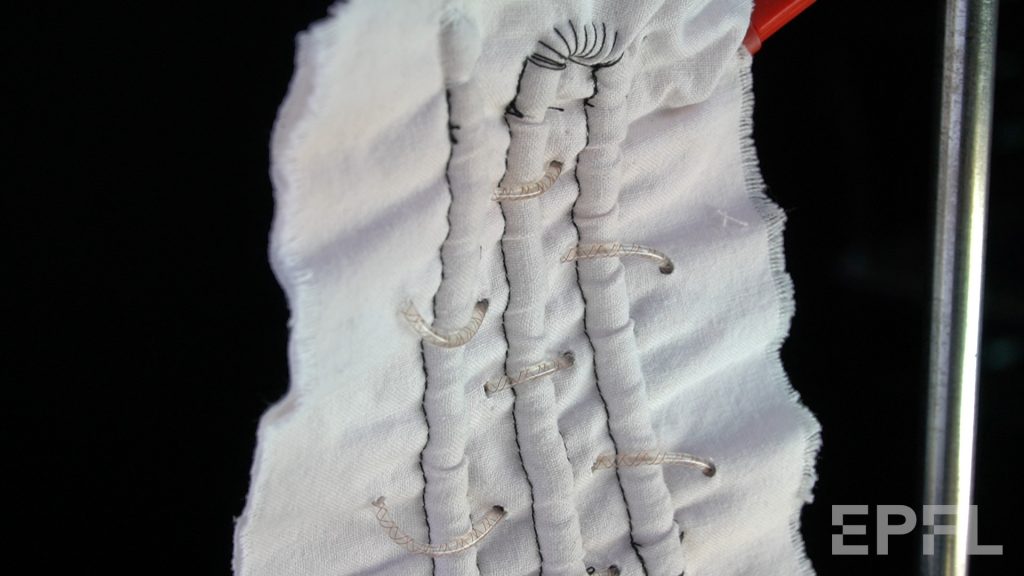
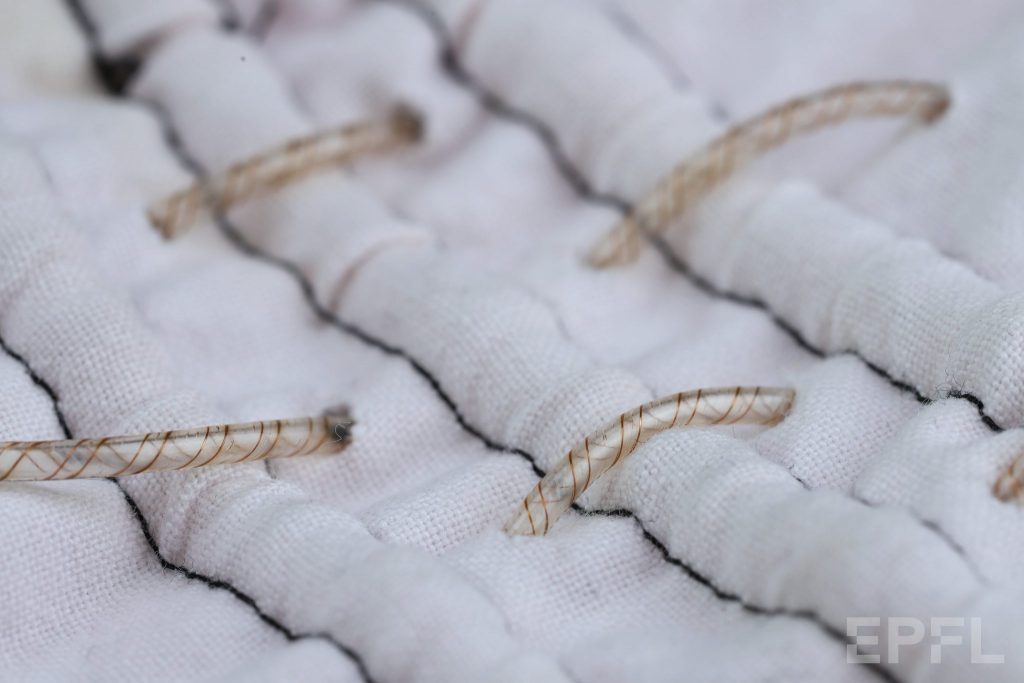
More information
For more information please refer to the published paper:
M. Smith, V. Cacucciolo, H. Shea, Fiber pumps for wearable fluidic systems. Science. 379, 1327–1332 (2023). Link.
Click here for an open access version of the manuscript.
See the coverage of our paper from EPFL STI news: Link
Funding
We are grateful to the Swiss National Science Foundation for funding this work under project IZLJZ2_183656.
Acknowledgements
A lot of people have helped to make this work possible. From LMTS we would especially like to thank V. Py and M. Benbedda for assistance with the high voltage electronics used in this work, as well as J. La Scala for developing the automated fabrication system used to make the fiber pumps. Further thanks to F. Hartmann for very helpful discussions and R. Hennig for assistance with videography and video editing.
Outside of LMTS we would like to thank S. Maeda for helpful discussions, as well as L. Caillaud for help in creating the textile based demonstrations used in this work. We are indebted to E. Valicka for help with the wearable demonstrations shown in this work as well as assistance with videography and video editing.