Dielectric Elastomer actuators consists of a soft elastomer membrane sandwiched between two compliant electrodes. When a voltage is applied between the electrodes, the electrostatic force squeezes the membrane, leading to a thickness decrease and an increase in surface.
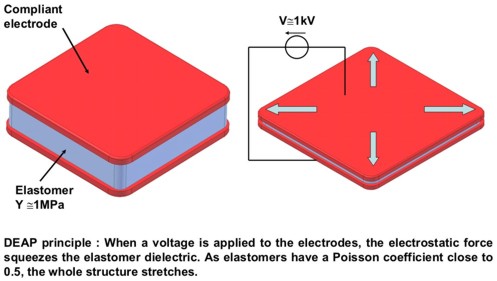
Main components of Dielectric elastomer Actuators
![]() |
![]() |
The elastomer membrane (click for more info) |
The compliant electrodes (click for more info) |
Fabrication Process of Silicone-based Dielectric Elastomer Actuators
The following video article describes our fabrication process: the fabrication of silicone membranes and patterning of compliant electrodes
Fabrication Process of Silicone-based Dielectric Elastomer Actuators
Rosset, S., Araromi, O. A., Schlatter, S., Shea, H. R. Fabrication Process of Silicone-based Dielectric Elastomer Actuators. J. Vis. Exp. (108), e53423, doi:10.3791/53423 (2016).
Low-voltage printed actuators
Dielectric elastomer actuators with silicone membranes are driven with electric field up to 150 v/um. For a 20 um-thick membranes, this corresponds to an actuation voltage of 3kV. High driving voltages are one of the main drawbacks of DEAs. It leads to bulky and expensive power sources and control electronics, not to mention safety issues that limit their usability in consummer products.
One way to decrease the driving voltage is to reduce the thickness of the membrane, ideally below 5 um. The fabrication process described above is not suitable in that case: it is difficult to manufacture very thin membranes by blade casting, and pad printing on very thin suspended membrane is impossible without damaging/tearing the membrane.
We have demonstrated a fabrication process to produce fully-printed DEAs. The membrane is applied by pad-printing — the same technique that we use for electrodes. The process is shown on the picture on the left:
1) The process starts with a PET foil covered with a water-soluble sacrificial layer.
2) A thin layer of PDMS is applied on the substrate by pad-printing and cured in an oven at 80° for 1h.
3) An electrode is applied by pad-printing on the PDMS layer and cured at 80° for 30min.
4) The substratr is immersed in warm water to dissolve the sacrificial layer. Onced detached, the thin silicone layer with electrode floats on the surface of the water bath (see also inset c).
5) After release, the membrane is dried, stretched, and fixed to a rigid Poly(methyl methacrylate) (PMMA) frame. Step 1-5 are repeated a second time to have two membranes stretched on frames
6) Two membranes are placed back to back to form a DEA (electrode/membrane/electrode). A drop of ethanol is used at the interface to allow for alignment and to ensure good conformal contact of the two membranes.
b) After adding electrical connection to the electrodes, the actuator is ready to be used. When a voltage is applied, the central active area (zone where the two electrodes overlap) expands.
d) Picture of an assembled device, ready to be tested
The typical thickness of pad-printed membranes is typically around 1.5 um, thus leading to 3um-thick actuators, once the two membranes are placed together.
Up to 7.5% linear strain has been obtained for a driving voltage of 245 V. As a comparison, the same actuator made on a 30 um-thick membrane requires a voltage ten times higher to reach the same strain level.
Printing low-voltage dielectric elastomer actuators, in Applied Physics Letters, vol. 107, num. 24, p. 244104, 2015.
Journal articles about our fabrication processes
Please note that the publication lists from Infoscience integrated into the EPFL website, lab or people pages are frozen following the launch of the new version of platform. The owners of these pages are invited to recreate their publication list from Infoscience. For any assistance, please consult the Infoscience help or contact support.