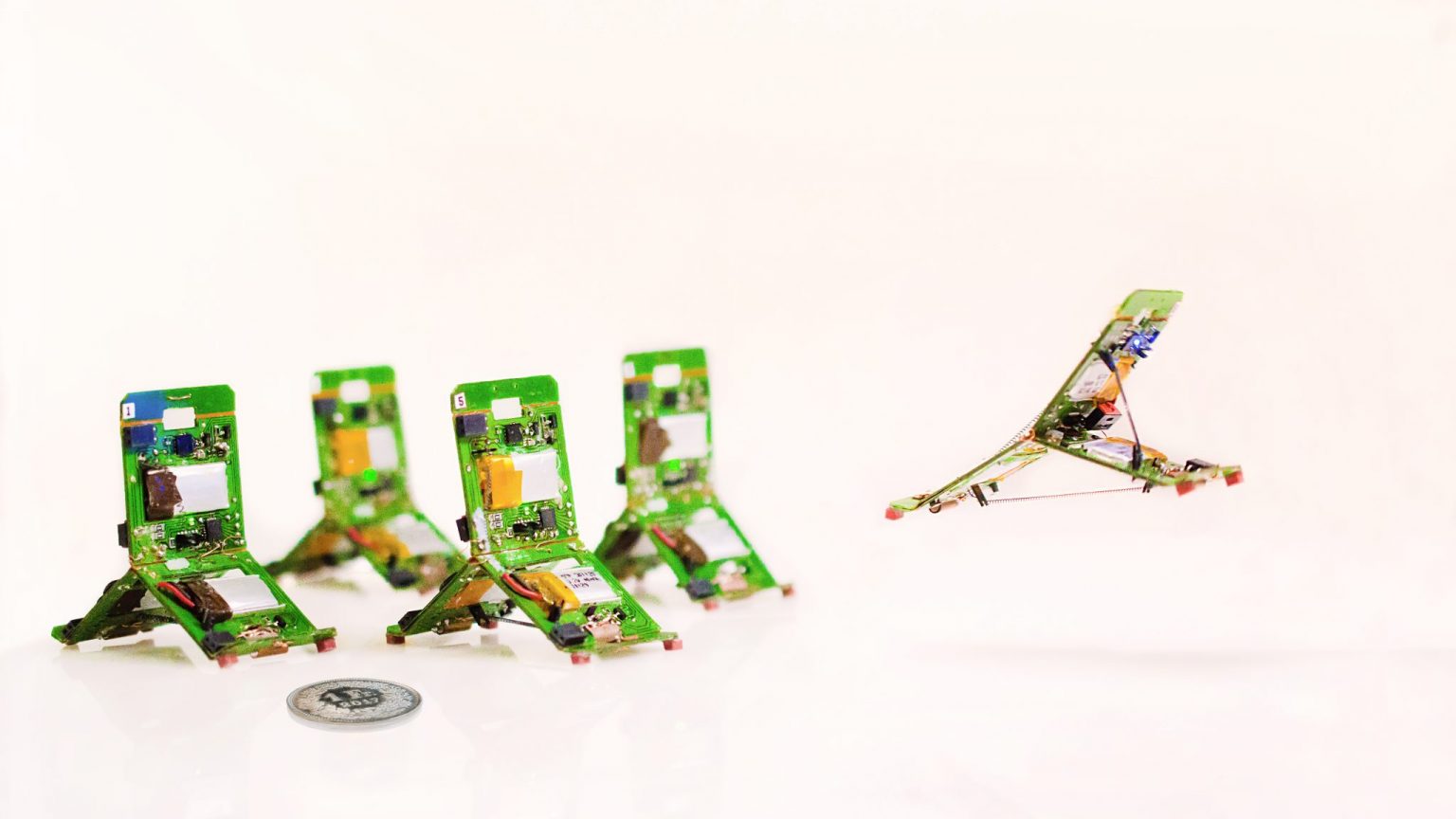
(c) Zhenishbek Zhakypov
- Freedom of Movement
- Tribot is an autonomous multi-locomotion insect-scale robot (millirobot) inspired by trap-jaw ants that addresses the design and scalability challenges of small-scale terrestrial robots. The robot’s compact locomotion mechanism is constructed with minimal components and assembly steps, has tunable power requirements, and realizes five distinct gaits: vertical jumping for height, horizontal jumping for distance, somersault jumping to clear obstacles, walking on textured terrain and crawling on flat surfaces. The untethered, battery-powered millirobot can selectively switch gaits to traverse diverse terrain types, and groups of millirobots can operate collectively to manipulate objects and overcome obstacles. We constructed the ten-gram palm-sized prototype—the smallest and lightest self-contained multi-locomotion robot reported so far—by folding a quasi-two-dimensional metamaterial sandwich formed of easily integrated mechanical, material and electronic layers, which will enable assembly-free mass-manufacturing of robots with high task efficiency, flexibility and disposability.
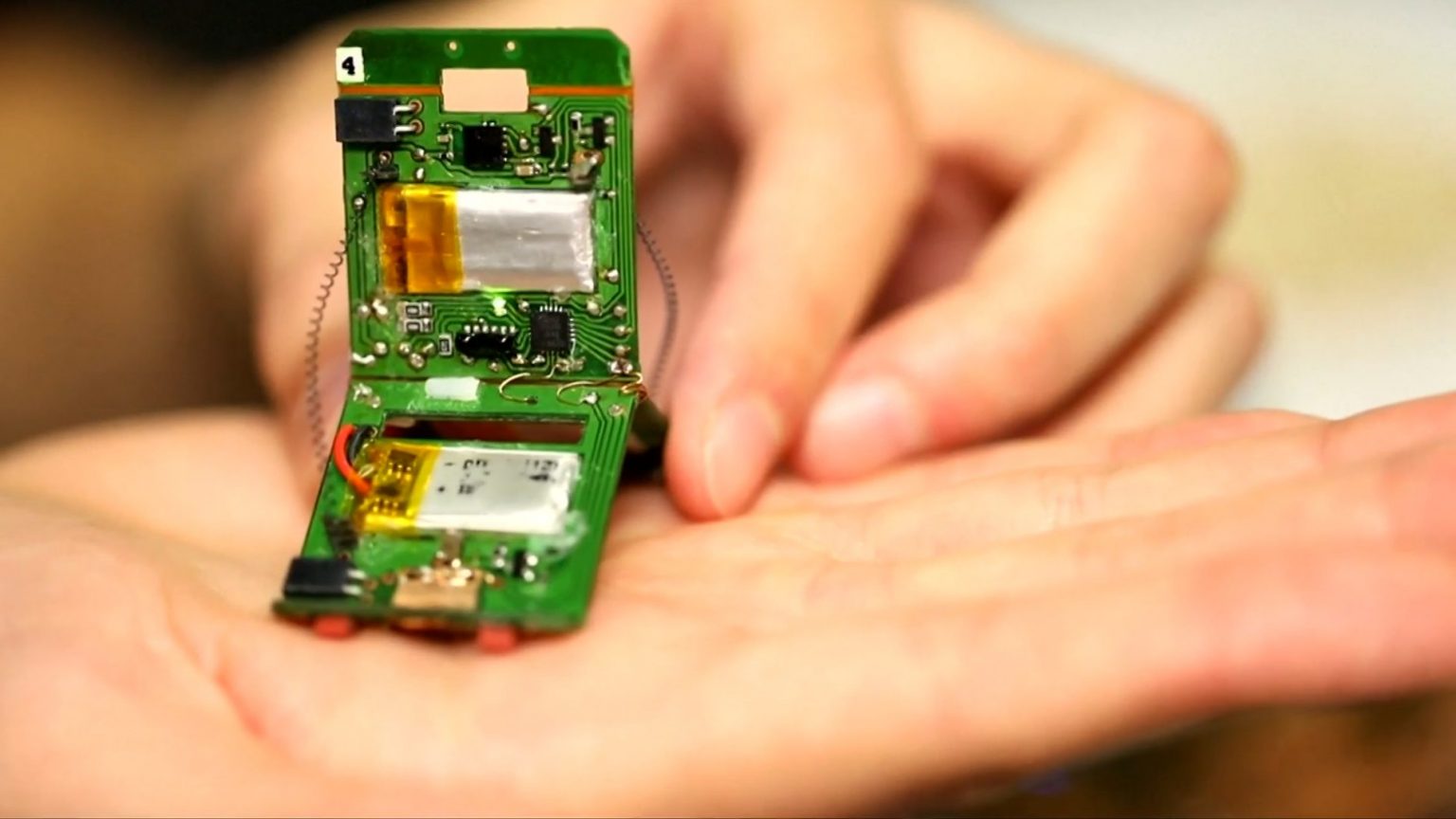
Tribot with mechanical and electronic components embedded by folding
- Robogami Design
- Robogami is foldable quasi-2D crease patterned machines and robots composed of functional material layers that can reconstruct various 3D shapes and mechanisms, theoretically, with infinite degrees-of-freedom. While traditional robot mechanical parts are manufactured in 3D, low profile bodies and functional material components for actuation, sensing, and other interfaces are processed in 2D, followed by composition and folding assembly to 3D allowing rapid, customized and inexpensive mass-fabrication. Using novel manufacturing processes and material combinations with great precision and compactness, a great variety of functional features can be introduced to robot design, like smart and adaptable locomotion.
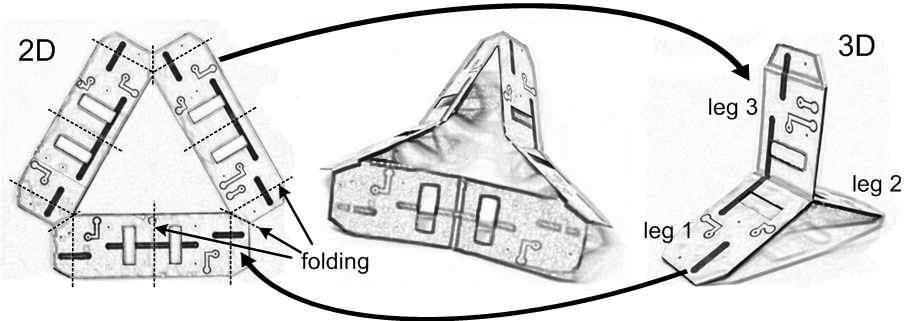
Folding design and assembly
- Origin
- The first versions of Tribot were tethered, weigh 4 g and jump seven times their height repeatedly. We studied two different approaches to build the prototypes. For one of them, we used the traditional, monolithic, layer-by-layer robogami fabrication method and the second, we printed out most parts using a multi-material 3D printer. The embedded sensors allow Tribot’s crawling gait pattern and jumping height to be modulated with a closed loop control.
Embed of video is only possible from Mediaspace, Vimeo or Youtube
- Versatility
- To address downsizing and repeatable operation adapted for uneven terrains, we designed and fabricated the foldable, deployable and self-righting version of multi-locomotion origami robot Tribot. The 4 g robot can jump high as 215 mm, 5x its height, and roll on any two edges with 55 mm steps using a single mechanism by selective actuation. The robot deploys 9x of its size when released and self-rights onto two legs after a jump or drop, making it an ideal candidate for search, environmental monitoring and space exploration.
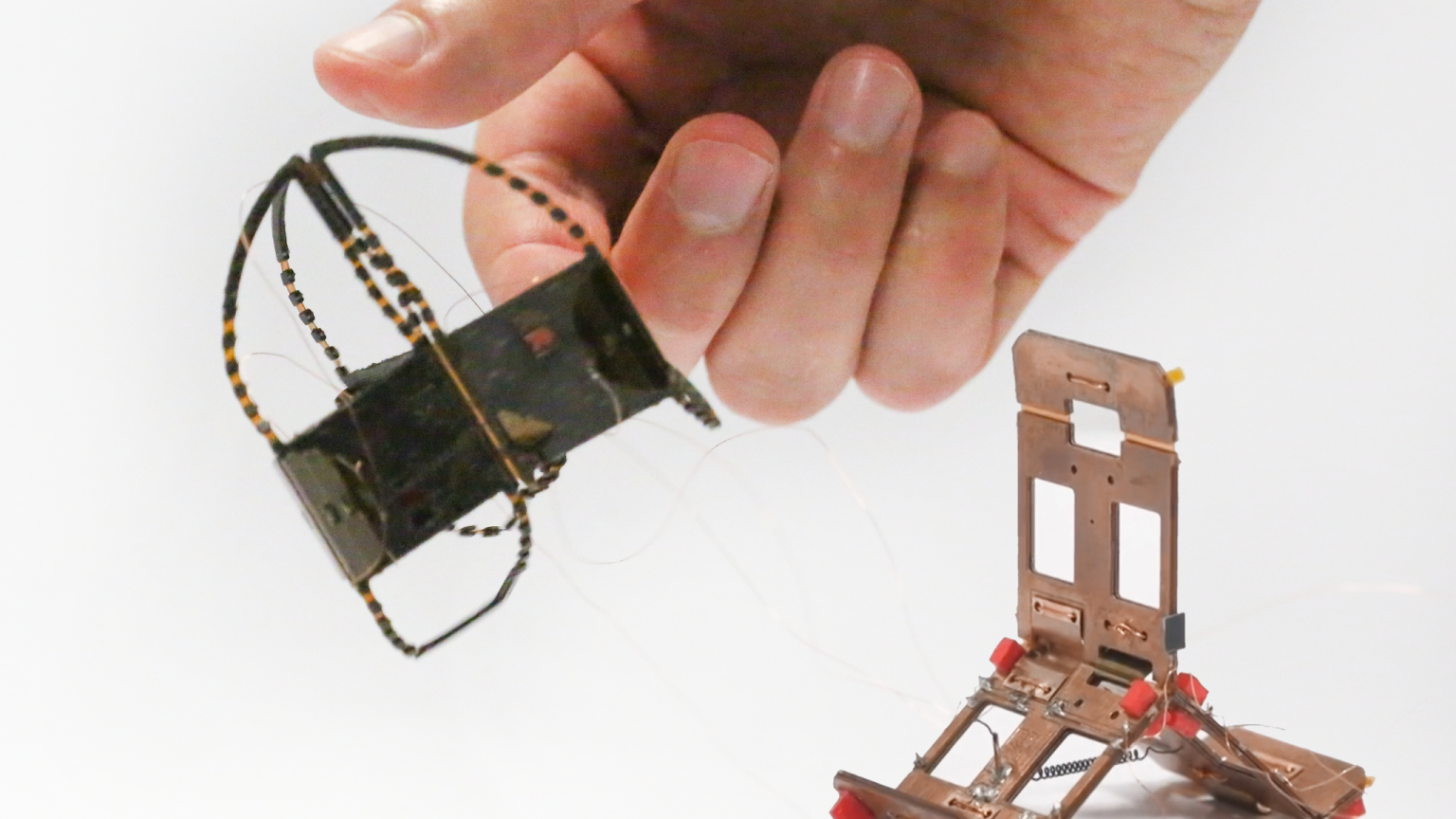
Earlier versions of Tribot
Embed of video is only possible from Mediaspace, Vimeo or Youtube
Got questions or ideas? Please contact Zhenishbek Zhakypov.
References
Please note that the publication lists from Infoscience integrated into the EPFL website, lab or people pages are frozen following the launch of the new version of platform. The owners of these pages are invited to recreate their publication list from Infoscience. For any assistance, please consult the Infoscience help or contact support.
Designing Minimal and Scalable Insect-Inspired Multi-Locomotion Millirobots
Nature. 2019-07-10. Vol. 571, p. 381–386. DOI : 10.1038/s41586-019-1388-8.Please note that the publication lists from Infoscience integrated into the EPFL website, lab or people pages are frozen following the launch of the new version of platform. The owners of these pages are invited to recreate their publication list from Infoscience. For any assistance, please consult the Infoscience help or contact support.
Design Methodology for Constructing Multimaterial Origami Robots and Machines
IEEE Transactions on Robotics. 2018. Vol. 34, num. 1, p. 151-165. DOI : 10.1109/TRO.2017.2775655.Please note that the publication lists from Infoscience integrated into the EPFL website, lab or people pages are frozen following the launch of the new version of platform. The owners of these pages are invited to recreate their publication list from Infoscience. For any assistance, please consult the Infoscience help or contact support.
Tribot: A Deployable, Self-Righting and Multi-Locomotive Origami Robot
2017. IEEE International Conference on Intelligent Robots and Systems (IROS), Vancouver, BC, September 24-28. DOI : 10.1109/IROS.2017.8206445.Please note that the publication lists from Infoscience integrated into the EPFL website, lab or people pages are frozen following the launch of the new version of platform. The owners of these pages are invited to recreate their publication list from Infoscience. For any assistance, please consult the Infoscience help or contact support.