Below is a list of currently available research project at RRL. If you are interested in carrying out one of the projects please contact the person responsible.
You can check the previous projects here.
These master’s projects are exclusively offered for the upcoming Spring 2024 semester. We are pleased to welcome Prof. Daniel Aukes, Associate Professor from Arizona State University, who will be visiting RRL, EPFL, and providing co-advisory support for the following master’s projects.
Kinematic analysis and structure design for spatial origami reconfigurable modular robotic platform (ori-pixel)
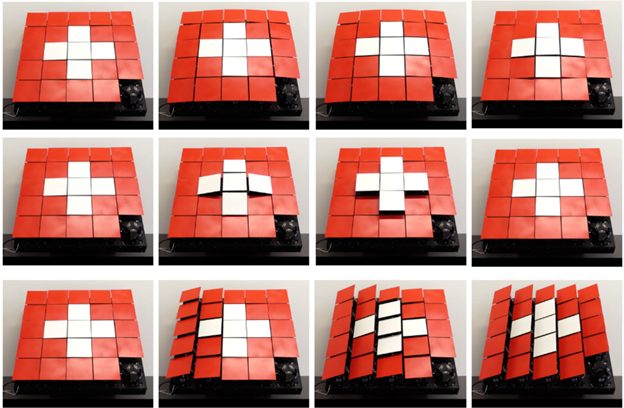
Section: Mechanical Engineering
Supervisors: Dr. Yuhao Jiang, Ziqiao Wang, Prof. Daniel Aukes (ASU), Prof. Jamie Paik (EPFL)
Number of Credits: 10-12 ECTS (300 hours) or Master Thesis
Timeline: Spring 2024
Intro: This project involves the mechanism design, kinematic analysis, and prototyping of the ori-pixel platform. The result will be utilized to develop a spatial hierarchical ori-pixel platform, facilitating the implementation of 2.5D configurations within the existing platform.
Keywords: Kinematic analysis, prototyping, mechanism design, modeling and testing
Deliverables: Kinematic models for the robotic platform, Dynamic simulations, and working prototypes;
Requirement: Python, microcontroller, CAD(Solidworks, Fusion 360);
Contact: Dr. Yuhao Jiang: [email protected]
Locomotion design and control using surface wave change generated by ori-pixel platform
Section: Mechanical Engineering
Supervisors: Dr. Yuhao Jiang, Dr. Hwayeong Jeong, Dr. Xiaoyang Zheng, Prof. Daniel Aukes (ASU), Prof. Jamie Paik (EPFL)
Number of Credits: 10-12 ECTS (300 hours) or Master Thesis
Timeline: Spring 2024
Intro: This project studies the dynamic geometry change and wave propagation that can be used for robotic locomotions. This project employs simulation tools to analyze advantageous surface geometries suitable for locomoting and interacting with the environment..
Keywords: Dynamic surface manipulation, dynamic simulation, control;
Deliverables: Control strategies for generating locomotions, Dynamic simulation of the working prototype, Prototype tests for validation;
Requirements: Python, CAD, Dynamic modeling, Control;
Contact: Dr. Yuhao Jiang: [email protected]
Study on soft metamaterials for object sensing and geometry generation
Section: Mechanical Engineering
Supervisors: Dr. Yuhao Jiang, Dr. Hwayeong Jeong, Dr. Xiaoyang Zheng, Prof. Daniel Aukes (ASU), Prof. Jamie Paik (EPFL)
Number of Credits: 10-12 ECTS (300 hours) or Master Thesis
Timeline: Spring 2024
Intro: This study focuses on exploring novel materials and structures that can be applied to ori-pixel modules for surface object detection and manipulation. This project involves exploring soft meta-materials and their electromagnetic behaviors for object sensing and dynamic geometry generation.
Keywords: Metamaterial analysis, FEA, mechanism design, prototyping, testing.
Deliverables: Soft sensors for contact detection, 3D printing metamaterials design and prototyping;
Requirement: Matlab, CAD, FEA, 3D printing
Contact: Dr. Yuhao Jiang: [email protected]
Programmable surface using bistable structure
Section: Mechanical Engineering
Supervisors: Dr. Hwayeong Jeong, Dr. Xiaoyang Zheng, Prof. Daniel Aukes (ASU), Prof. Jamie Paik (EPFL)
Number of Credits: 10-12 ECTS (300 hours) or Master Thesis
Timeline: Spring 2024
Intro: Develop a novel modeling method for soft programmable surfaces using bistable or multi-stable structures.
Implement the dynamics from the material and geometric design of bistable structures to obtain multimodal locomotion.
Create an algorithm to determine the global shape or movement based on the state of each individual bistable joint.
Integrate it with the pneumatic pouch actuator to automate the shape change.
Keywords: Programmable surface, bistable structure, material and geometric design
Deliverables: Working prototypes of the bistable structure for shape actuations;
Requirement
Experience in CAD, Mechanical modeling, Dynamic modeling, and prototyping. Nice to have FEM simulation.
Contact: Dr. Hwayeong Jeong: [email protected]
Multi-scale & Modular Interactive Robotic Surface
Section: Mechanical Engineering, Microengineering
Supervisors: Alihan Bakır, Fabio Zuliani, Prof. Jamie Paik (EPFL)
Number of Credits: 10-12 ECTS (300 hours) or Master Thesis
Type: 20% theory, 40% modeling, 20% design, 20% testing
Timeline: Spring 2024
Description: Redefine living spaces through smart and adaptive surface that can create interactive and physically immmersive setups.
Expected work:
- Different projects are available with various focus depending on the student interest and prior experience.
- Physical modeling and mechanical iteration of the human-scale modules to create a room-size surface.
- Human-in-the-loop interactive control of a set of robots.
- Control and powering electronics of human-scale robots.
- Virtual environment interactive development.
All positions are filled for Multi-scale & Modular Interactive Robotic Surface project. Thank you for your interest.
Contact: [email protected], [email protected]