- Student projects in LMIS1
- We offer a variety of projects for students for both semester and master projects in the field of Micro- & Nanoengineering. Mostly, the proposed projects are linked to our ongoing research topics for PhD projects, postdocs or senior scientist, that are funded by EPFL or third party funds (SNF, CTI/KTI, EU, etc). In that way, the student is involved in real-life topics with clearly assigned tasks that are complementary but in collaboration with the laboratory’s research staff. Alternatively, we also invite Master students to propose their own idea on the realization of a new technology or device in the field of Micro- & Nanoengineering. If you have a concrete idea, please don’t hesitate to talk to Prof. J. Brugger and Dr. G. Boero directly or to one of the staff members to see if a Semester or Master project can be defined around the idea generated by you.
- Download all the available projects here
- All student projects are also listed on IS-academia
Grayscale nanolithography for 2D nanoelectronics
While nanolithography has historically focused on downscaling, there is now a growing interest in grayscale nanolithography for introducing or enhancing functionality in micro-nanodevices applied to optics and fluidics. Grayscale thermal scanning probe lithography (t-SPL) achieves single-digit nanometer spatial resolution and sub-nanometer depth control. In t-SPL, a heated nanotip is used to pattern a temperature-sensitive resist. The fine control over the indentation depth of the tip via an electrostatic potential between the tip and the substrate allows the fabrication of grayscale patterns with high precision.
Grayscale topography engineering for 2D nanoelectronics
Type : Semester project / Master project
Section : Microengineering, Electrical Engineering, Materials Science
While nanolithography has historically focused on downscaling, there is now a growing interest in grayscale nanolithography for introducing or enhancing functionality in micro-nanodevices applied for optics and fluidics. Grayscale thermal scanning probe lithography (t-SPL) achieves single-digit nanometer spatial resolution and sub-nanometer depth control, but it has limited scalability. We combine t-SPL with nanoimprint lithography to replicate high-resolution grayscale nanostructures on large surfaces by step-and-repeat process [1, 2]. For the next generation of nanoelectronics, we use these deterministic grayscale topographies for strain engineering of 2D materials as they hold the potential to replace silicon in transistors with sub-10 nm channel lengths.
Figure 1: a AFM images and amplitude comparison of a sinusoidal pattern before (Line 1) and after (Line 2) dry etch transfer. b Fourier transforms of the measured topographies after t-SPL on PPA and transferred into SiO2. c Fabrication process flow of grayscale dielectric nanostructures for 2D materials strain.
The main tasks in the project will be:
- Grayscale stamp fabrication by combining t-SPL and dry etching
- Nanoimprint lithography and metrology characterization (In case of semester project only)
- 2D material strain characterization
Desired Skills:
- Autonomy
- Knowledge in cleanroom processes is a plus
References:
[1] Howell, Samuel Tobias, et al. “Thermal scanning probe lithography—A review.” Microsystems & nanoengineering 6.1 (2020): 1-24.
[2] Erbas, B. et al. Combining thermal scanning probe lithography and dry etching for grayscale nanopattern amplification. doi:10.1038/s41378-024-00655-y.
Contact: Berke Erbas ([email protected])
Nanostencil for Single Ion Doping
At LMIS1 we are also taking part on the research for new quantum technologies by using nanostencils (consisting into a very thin Si3N4 membrane with nanoapertures patterned into it) as masks for the precise placement of single ions into silicon in order to use their nuclear or electronic spins as quantum entities to be utilized as qubits for quantum computing. We are currently exploring different strategies such as ion implantation or ion diffusion to achieve single ion doping and improve the state-of-the-art.
Unfortunately, no specific student project is currently available on this topic. Nevertheless, LMIS1 strongly encourages proactive students, interested in our research, to get in contact with us for eventually discussing about “out-of-the-box” intuitions and ideas. In the case you are motivated to carry out a student project, please, directly contact Pol Torres Vila ([email protected]) or Prof. Jürgen Brugger ([email protected]).
The ROSE project
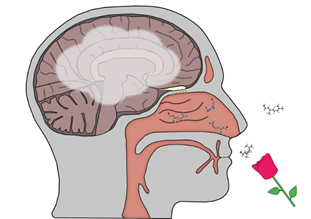
If you have no olfactory impairment, perhaps you are unaware of the importance of your sense of smell. Odors are sources of both pleasure and social bonding, they contribute to our emotional wellbeing, with reduced or absent olfaction being linked to depression. Loss of smell also increases the risk of household accidents (detection of noxious gases and smoke). It is estimated that partial or total loss of smell arising from a variety of causes (trauma, congenital deficits, age, viral infection and other pathologies) concerns about 20% of the population. Restoring olfaction – completely or even partially – is important for society, but a difficult challenge for science: a technological device capable of restoring odorant detection and recognition is currently being developed at LMIS1.
Development of an olfactory prosthesis for people suffering from anosmia
Type : Master/Semester Project or lab immersion
Section : Microengineering, Physics, Electric Engineering, Life Science
Sensory deficits are a major source of handicap in people’s lives. Scientists have already developed prostheses and implants for hearing impairments and are developing those for vision. Partial and total loss of smell (hyposmia / anosmia) impacts 20% of the world-wide population with deleterious effects on quality of life. However, we have yet to develop such devices to restore the sense of smell, primarily because scientific knowledge linking artificial systems to human biological olfaction is still lacking. The ROSE project is composed of a European consortium working together to push the limit of artificial olfactory sensations. The project will be held in close collaboration with the European partners and may include travels to meet with them.
At the LMIS1, we are currently investigating new ways of generating sensations in the nasal cavity using different methodologies, such as electrical stimulation. The project is evolving quickly and is highly multidisciplinary, involving aspects of physiology electronics, cleanroom microfabrication and materials science: the focus can be adjusted depending on the student’s preferential interests, best knowledge, previous experience and motivation.
Figure 1 : (a) schematic showing the olfactory system (b) Paradigm of the ROSE project for the restauration of olfaction in anosmic people
Possible tasks:
- Cleanroom work
- Microfluidics
- Electronics design
- Experimental characterization
- 3D printing
Contact: Biranche Tandon ([email protected])
Arnaud Bertsch ([email protected])
Additive Manufacturing for Therapeutic Delivery Devices
In LMIS1 we are currently developing therapeutic delivery devices that encapsulate various therapeutic cargos using additive manufacturing technology. The high degree of freedom in design and materials in additive manufacturing technology (AM) enables device adaptation for personalized therapeutic. Further incorporation of biodegradable materials and active release methods into our device will expand the technique’s applicability.
Fabrication of lipid microneedle by Inkjet printing for prolonged drug delivery
Type : Master/Semester project
Section : Microengineering, Mechanical Engineering, Bio engineering, Materials Science
The project focuses on the development of lipid microneedles using inkjet printing for prolonged drug delivery. Microneedles represent a huge advancement in transdermal drug delivery systems, offering a minimally invasive and efficient method for administering medications over extended periods. Co-administration of poorly water-soluble drugs with lipid formulations can enhance the bioavailability of these drugs. Administration of drugs encapsulated lipid formulations can be the one way of achieving this. Recently fabricating the various design of drug-lipid formulations enabled by the development of additive manufacturing techniques. However, fabrication and utilization of lipid microneedle has many challenges due to intrinsic characteristics of lipid. The primary goal of this project is to develop core-shell lipid micro needle using inkjet printing for precise dimensions and drug-loading capacities. The plan involves a detailed investigation of suitable lipid materials, optimization of the inkjet printing parameters, and thorough evaluation of its mechanical and chemical characteristics, microneedles’ structural integrity, drug release profiles.
Figure SEM image of fabricated lipid microneedle by IJP
Work description :
- Fabrication of lipid mold in CMI
- Fabrication of lipid micro needle using IJP
- Characterization of microneedle (mechanical and chemical)
- In vitro drug release measurement from microneedle
Contact : Jongeon Park ([email protected])
Additive Manufacturing for Biomedical Applications
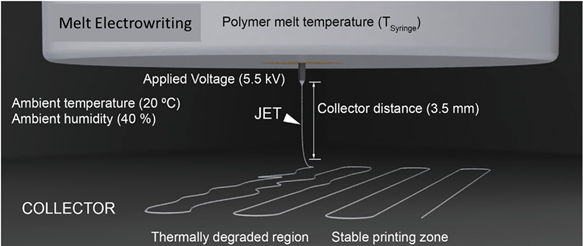
At LMIS1, we are expanding our capabilities in micro manufacturing of biomaterials using 3D printing. Melt electrowriting (MEW) is an electrohydrodynamic 3D printing technique which involves processing of polymer melts into micron sized fibers (5-100 µm) using high voltage as the driving force. The fibers can be deposited in a layer-by-layer manner to make 3D printed constructs. The 3D printing can be done in desired patterns to produce a wide range of mechanical properties.
Investigation of simple parameters on the fibre diameter in melt electrowriting (MEW)
Type : Semester Project
Section : Microengineering, Materials Science, Electric Engineering
Over the last two decades, additive manufacturing (3D printing) has been gaining significant attention in tissue engineering and biofabrication research as a versatile class of manufacturing technologies. This primarily stems from its ability to fabricate unique patient-specific designs as well as fabricate structures from a wide range of biomaterials.1 For biomedical applications, high resolution 3D printing techniques, such as melt electrowriting (MEW) have been favoured for their exceptional ability to replicate the fine features and complex microarchitecture of native tissues to mimic both their structure and function.2 To date MEW research often utilises pressure-driven extrusion methods on custom devices built by individual research groups, processing the most common polymer in MEW poly(caprolactone) (PCL).
At the LMIS1, we are currently investigating a novel filament-based extrusion system, which has many advantages over the current standard due to the possibilities in processing a wider variety of polymers.3 A current gap is in the understanding of the jet and the influence of different parameters such as the nozzle diameter and extrusion rate on it and the resulting fibres. This student project will contribute to the understanding of how these different parameters interact and result in a printed fibre. This can allow for more control over the jet and the resulting structures for future applications.
The topic is highly multidisciplinary, involving aspects of engineering, computer and materials science: the focus can be adjusted depending on the student’s preferential interests, best knowledge, previous experience and motivation.

Figure 1 : (left) schematic showing the principles behind melt electrowriting (MEW), (right) scaffold printed with MEW.
Possible tasks:
- Analysis of the influence of the nozzle diameter (150 – 400 µm) on the fibre diameter.
- Design of experiments to be performed on our five printers to
- verify their extrusion rates,
- evaluate the reproducibility of experiments,
- assess the validity of theoretical predictions on different polymers (no chemical knowledge required!).
- SEM characterisation of finalised scaffolds on modern instruments.
References:
[1] B.P. Chan, K.W. Leong, Eur Spine J, 2008, 17, 467-479;
[2] J.C. Kade, P.D. Dalton, Adv Healthcare Mater, 2021, 10, 2001232;
[3] A. Reizabal, et al., Addit Manuf, 2023, 71, 103604.
Contact: Sönke Menke ([email protected])
Biranche Tandon ([email protected])
Implementation of machine learning (i.e. Bayesian Optimisation) and computer vision for melt electrowriting (MEW)
Type : Master Project
Section : Computer Science, Materials Science, Software Engineering
Over the last two decades, additive manufacturing (3D printing) has been gaining significant attention in tissue engineering and biofabrication research as a versatile class of manufacturing technologies. This primarily stems from its ability to fabricate unique patient-specific designs as well as fabricate structures from a wide range of biomaterials.1 For biomedical applications, high resolution 3D printing techniques, such as melt electrowriting (MEW) have been favoured for their exceptional ability to replicate the fine features and complex microarchitecture of native tissues to mimic both their structure and function.2 To date MEW research often utilises pressure-driven extrusion methods on custom devices built by individual research groups, processing the most common polymer in MEW poly(caprolactone) (PCL).
At the LMIS1, we are currently investigating a novel filament-based extrusion system, which has many advantages over the current standard due to the possibilities in modification and customisation.3 A current research gap is in the control of the print on-the-fly, while monitoring it, and reacting to environmental factors. This thesis will contribute to the implementation of a visual system, linked to Bayesian optimisation (BO4) for on-the-fly corrections of the print and precision control over the resulting fibres.
The topic is highly multidisciplinary, involving aspects of engineering, computer and materials science: the focus can be adjusted depending on the student’s preferential interests, best knowledge, previous experience and motivation. (Fundamental) knowledge of BO is a must, but can be expanded upon with literature study.

Figure 1 : (left) schematic showing the principles behind melt electrowriting (MEW), (right) graphical overview of Bayesian optimisation, taken from ref 4.
Possible tasks:
- Improvement of a computer vision system for the printer (Raspberry pi based)
- Implementation of BO analysis of manufactured fibres (further development of previous study)
- Implementation of on-the-fly adaptation of parameters of MEW (such as extrusion rate, voltage and printing speed……)
- SEM characterisation of finalised scaffolds on modern instruments
References:
[1] B.P. Chan, K.W. Leong, Eur Spine J, 2008, 17, 467-479.
[2] J.C. Kade, P.D. Dalton, Adv Healthcare Mater, 2021, 10, 2001232.
[3] A. Reizabal, et al., Addit Manuf, 2023, 71, 103604.
[4] B.J. Shields, et al., Nature, 2021, 590, 89.
Contact: Sönke Menke ([email protected])
Biranche Tandon ([email protected])
3D printing (fused deposition modelling) of metallic tubes with complex geometries
Type : Master/Semester Project
Section : Microengineering, Bio Engineering, Materials Science, Robotics
Fused deposition modelling (FDM) or fused filament fabrication is a 3D printing technique where a polymer melt is extruded through a nozzle onto a temperature-controlled build platform. A three-dimensional structure is successfully created by stacking the extruded polymer layer-by-layer. For most applications and structures, a flat build plate is usually sufficient. However, it can be limiting in some cases where fine features are required as overhangs and some post processing techniques like sintering are to be employed on the printed object.

Figure 1. a) Schematic of the idea of tubular collector on FDM printer. b) Sample fibre printed using metal filled filament. c) Potential design ideas for printing.
A FDM printer usually uses a standard polymer filament with 1.75/2.85 mm diameter. A large variety of polymers have been processed using this technique with poly lactic acid (PLA) being the most utilized due to the ease in processability. Other materials such as Nylon, flexible thermoplastic urethane and fiber reinforced polymers have also been used and are available commercially. There is increasing interest in composite materials, specifically metal filled and ceramic filled polymers which can be used in FDM. The printed parts from these materials can be sintered (high temperature treatment) to obtain fully metallic and ceramic components.
This student project will involve improving and upgrading the tubular collector on a Voron FDM printer. The next part of the project will involve printing of metal/ceramic filled polymer filaments with minimum resolution feasible. The printed parts will be sintered and analyzed to further optimize the FDM approach to obtain fully metallic/ceramic tubular constructs. The project can be expanded to test the feasibility of printing composite filaments using melt electrowriting (MEW) technique which involves application of an additional high voltage to the FDM setup in order to reduce the minimum feature size which can be obtained.
Possible tasks:
- Incorporating heating on tubular collector on Voron 0
- Software control for printing complex geometries with minimum resolution on tubes
- Testing composite materials to print functional constructs (metal or ceramic filled FDM filaments)
- MEW of composite materials
Useful readings:
[1] Hong et al, Open5x: Accessible 5-axis 3D printing and conformal slicing (https://dl.acm.org/doi/10.1145/3491101.3519782)
Contact: Sönke Menke ([email protected])
Biranche Tandon ([email protected])
3D printer upgrade to enable successful melt electrowriting of tubular structures with various sizes and geometries
Type : Master/Semester Project
Section : Microengineering, Materials Science, Robotics, Bio Engineering
Over the last two decades, additive manufacturing (3D printing) has been gaining significant attention in tissue engineering and biofabrication research as a versatile class of manufacturing technologies. This primarily stems from its ability to fabricate unique patient-specific designs as well as fabricate structures from a wide range of biomaterials. For biomedical applications, high resolution 3D printing techniques, such as melt electrowriting (MEW) have been favoured for their exceptional ability to replicate the fine features and complex microarchitecture of native tissues to mimic both their structure and function. To date MEW research often utilises pressure-driven extrusion methods on custom devices built by individual research groups, processing the most common polymer in MEW polycaprolactone (PCL).
At the LMIS1, we are currently investigating a novel filament-based extrusion system for MEW, which has many advantages over the current standard due to the possibilities in processing a wider variety of polymers. The printer has two different collector configurations, flat and tubular (cylindrical) collector, which can be used for printing structures. A current limitation of the tubular system is the availability of a single diameter mandrel (3 mm). This student project will contribute to upgrading the printer and interchangeable upgrades to enable successful printing on mandrels with diameter in range of 1 – 5 mm (cylindrical and polygonal). There will be an additional software component in the project which will aim at designing the codes to enable successful MEW on these mandrels.
The topic is highly multidisciplinary, involving aspects of engineering, computer and materials science: the focus can be adjusted depending on the student’s preferential interests, best knowledge, previous experience and motivation.

Figure 1. a) Schematic of the idea of tubular collector on MEW printer. b) Sample wrap around tubular designs printed using MEW (2mm scale). c) Theta tubular design for printing using collectors of various diameters.
Figure 1. a) Schematic of the idea of tubular collector on MEW printer. b) Sample wrap around tubular designs printed using MEW (2mm scale). c) Theta tubular design for printing using collectors of various diameters.
Possible tasks:
- Modification of the printer for successful processing on various collector sizes/designs
- Software control for printing complex geometries.
- Assessment of mechanical properties of the printed tubes
Useful readings:
[1] Hong et al, Open5x: Accessible 5-axis 3D printing and conformal slicing (https://dl.acm.org/doi/10.1145/3491101.3519782)
Contact: Sönke Menke ([email protected])
Biranche Tandon ([email protected])
Transient electronics made by stencil lithography
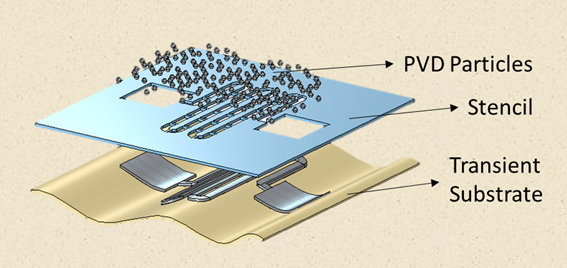
At LMIS1, our research efforts in stencil lithography have yielded significant advancements. The recent invention of the bridge stencil has allowed us to pattern a wider range of shapes with greater precision. Expanding on this success, we are now shifting our focus to materials. Leveraging the resistless nature of stencil lithography and its ability to avoid liquid processes, we aim to utilize transient materials like magnesium and zinc for patterning. Our ultimate objective is to establish an electronic library in transient form, showcasing the potential of stencil lithography in the patterning of more kinds of materials.
Designing and Validating Bridges on Stencils: Calculation, Simulation, and Verification
Type: Master/Semester Project
Section: Microengineering – Physics – Materials Science
Stencil lithography is a resistless micro-fabrication method using a silicon nitride film stencil for pattern deposition or etching.[1] It enables sub-nanometer scale patterns without the need for photoresist or liquid environments. However, challenges include the inability to pattern closed-loop designs due to film detachment, and the risk of stencil curvature or breakage caused by inner stress. Researchers have explored stencil movement during deposition and other approaches to address these issues.
At LMIS1, a new solution was proposed, incorporating auxiliary bridges in stencils. These bridges serve dual purposes: securing the suspended part of the stencil and preventing membrane curvature. By maintaining a specific gap between stencil and substrate, blurring effects during deposition ensure continuous pattern coverage beneath the bridges. Extensive measurements of morphology and electrical properties have validated the effectiveness of the bridge stencil.
The focus of this student project will be on optimizing the design parameters of the bridge stencil. This includes investigating the width and density of bridges, determining their optimal placement, and establishing the ideal gap between the stencil and substrate. The ultimate goal of the project is to develop a set of guidelines for the automated design tool for bridge stencils.
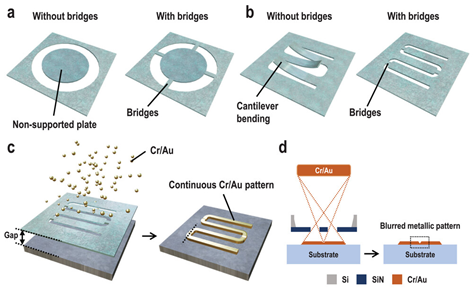
Figure 1 : The concept of bridge stencils and the blurring effect. a,b) Schematic drawings showing the use of bridges for a) realizing unfeasible geometries on stencils (e.g., close-loop circular apertures), and b) suppressing the bending of cantilevers for meandering apertures. c,d) Schematic drawing showing the beneficial use of the blurring effect. [2]
Possible tasks:
- Conduct stress calculations in simple models to analyze the relationship between bridge parameters and stress levels.
- Simulate stress distribution in complex patterns (e.g., circles, serpentines) to guide optimal bridge placement.
- Verify the concept of bridge placement in the clean room.
References:
[1] O. Vazquez-Mena et al, vol. 132, pp. 236–254, Jan. 2015.
[2] Y.-C. Sun et al, Adv. Mater. Technol., vol. n/a, no. n/a, p. 2201119.
Contact: Chenxiang Zhang ([email protected])
Droplet Microfluidics for Advanced Additive Manufacturing
Under the umbrella of multi-material 4D printing, at LMIS1, we are developing an innovative microfluidic-based additive manufacturing technique that can deposit polymerizable microdroplets encapsulating multiple materials with variable space resolutions. This technological advancement offers flexibility and accuracy in constructing complex structures and objects with enhanced functionalities while maintaining a similar production rate to existing AM techniques.
Droplet Microfluidics for Advanced Additive Manufacturing
Type: Semester Project
Section: Material Science, Microengineering
Droplet microfluidics is a cutting-edge technology that encapsulates fluids and materials into micron-scale droplets, which can serve as fundamental units for constructing 3D objects1. This enables the assembly of 3D objects voxel by voxel during the printing process. Recent achievements have been made on developing voxelated printheads to produce parts with multi-material compositions2,3. However, material combinations with dissimilar properties remain limited in current techniques.
The objective of this project is to develop a novel microfluidic-based additive manufacturing (AM) technique that can deposit polymerizable microdroplets. By utilizing droplet microfluidic chips as printheads, we aim to generate droplets of active and passive resins in controllable sizes. This project will investigate the generation and polymerization of droplets within a compressed gas flow (such as air or Argon) to eliminate the need for a secondary liquid medium. These droplets will be solidified within microfluidic channels using UV light or heat before being ejected. Additionally, we will explore the strategies for ejecting these polymerized beads and accurately depositing them onto a printing bed.
Figure 1: (a) schematic drawing of key steps in this project; (b) an optical image of PEGDA250 (clear) droplet formation in an aqueous phase (red) on a flow-focusing microfluidic chip; (c) an SEM image of PEGDA250 beads which were in-flow polymerized under UV light.
Possible tasks:
- Characterization of the influence of compressed gas flow rate on droplet size, generation frequency and polymerization.
- Generation of droplets of viscous resins (viscosity >1 Pa.s) or resins containing nanoparticles via a phase inversion method.
References:
[1] Zhang, Pengfei, et al. “Printhead on a chip: empowering droplet-based bioprinting with microfluidics.” Trends in Biotechnology (2023).
[2] Skylar-Scott, Mark A., et al. “Voxelated soft matter via multimaterial multinozzle 3D printing.” Nature 575.7782 (2019): 330-335.
[3] Buchner, Thomas JK, et al. “Vision-controlled jetting for composite systems and robots.” Nature 623.7987 (2023): 522-530.
Contact: Tao Zhang (tao.zhang@epfl.ch)
Dr. Arnaud Bertsch (arnaud.bertsch@epfl.ch)
Mixed reality learning for microfabrication practical
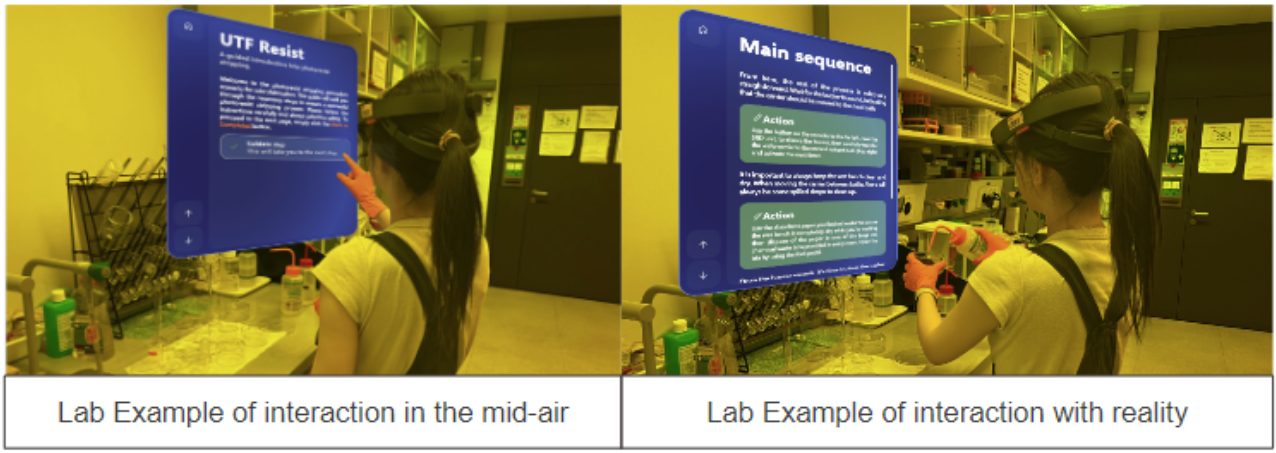
At LMIS1, we are currently embarking on a novel journey to integrate mixed reality into learning methods for microfabrication processes. This approach presents a promising avenue as it allows hands-free interaction and diminishes cognitive load during learning. Our research is dedicated to creating interactive mixed-reality content to revolutionize microfabrication and cleanroom training practices. As we scrutinize the effectiveness and feasibility of multimodal learning within a mixed reality framework, we are embracing various learning strategies including gamification, scaffolding, and multimodal interaction.
Unfortunately, no specific student project is currently available on this topic. Nevertheless, LMIS1 strongly encourages proactive students, interested in our research, to get in contact with us for eventually discussing about “out-of-the-box” intuitions and ideas. In the case you are motivated to carry out a student project, please, directly contact Qinglan Shan (qinglan.shan @epfl.ch) or Prof. Jürgen Brugger ([email protected]).
Cryogenic Microwave Thermometry
At LMIS1 we are currently assessing possible alternatives to state-of-the-art 4-wires thermistors for cryogenic thermometry in ultra-low temperature systems (i.e. < 90 K). High quality factor superconducting resonators are investigated in order to explore the fundamental T-variations properties related to Cooper pairs kinetic inductance changes, with the final goal to sense cryogenic temperatures by means of resonance frequency shifts.
Characterization of NbTi Superconducting Thin Film Non-Linear Devices for Quantum Superconducting Circuits
Type: Semester Project
Section: Microengineering, Physics, Electronic Engineering
Nowadays, quantum technologies based on superconducting materials are becoming of primary importance for the development of new computational paradigms, as well as for designing a new generation of ultra-sensitive cryogenic sensors. The possibility to exploit nonlinear effects, such as the Josephson one, is crucial for the implementation of detection mechanisms relying on the quantization of physical parameters, like, for instance, the magnetic flux in Superconducting Quantum Interference Devices (SQUIDs) [1] and the frequency-to-voltage conversion based on the Shapiro steps phenomenon [2].
At LMIS1, we are currently investigating new possibilities of realizing alternatives to standard SIS or SNS Josephson junctions at cryogenic environments (T < 90 K). We are developing new ways of inducing the Josephson junction behavior on a localized region of the superconducting circuits by simple fabrication methods. The strategy consists of exploiting some of the quantum properties of the superconductors at the micro-nano-scale.
This student project will contribute to investigate the electronic transport of specific structure realized in superconducting NbTi thin films, eventually demonstrating the possibility to exploit them for realizing more complex structures based on nonlinear Josephson junctions (i.e. SQUIDs and Shapiro steps). The topic is highly multidisciplinary, involving aspects of condensed matter and low temperature physics, as well as DC/RF electronics design and test: the focus can be adjusted depending on the student’s preferential interests, best knowledge, previous experience and motivation.
Figure 1 : (a) schematic showing the working principle of a SQUID magnetometer; (b) Photograph of a chip containing superconducting structures in NbTi to be characterized in cryogenic environments (< 10 K).
Possible tasks:
- Implementation of measurement apparatuses for cryogenic DC/RF testing
- Cryogenic characterization of NbTi thin film structures, either in liquid He or in a dry cryomagnet:
- Temperature or magnetically induced effects in DC structures or RF resonators;
- Sub-uT magnetic field detection based on our alternative SQUIDs;
- Frequency-to-voltage conversion based on Shapiro steps phenomenon.
References:
[1] F. Qu et al. (2012) Scientific Reports 2:339, https://doi.org/10.1038/srep00339
[2] X. Bi et al., (2024) Quantum Frontiers 3:6, https://doi.org/10.1007/s44214-024-00053-5
Contact: André Chatel (andre.chatel @epfl.ch)
Hernán Furci ([email protected])
Giovanni Boero ([email protected])
ESR and NMR Spectroscopy
Electron Spin Resonance (ESR) spectroscopy is a widely used technique for the recognition of chemical radicals and species. At LMIS1 we are currently working on the optimization of ESR sensors’ sensitivity, especially for samples in the nanoliter and sub-nanoliter range, through the use of superconducting resonating structures.
Unfortunately, no specific student project is currently available on this topic. Nevertheless, LMIS1 strongly encourages proactive students, interested in our research, to get in contact with us for eventually discussing about “out-of-the-box” intuitions and ideas. In the case you are motivated to carry out a student project, please, directly contact Reza Farsi (reza.farsi@epfl.ch), Roberto Russo ([email protected]) or Prof. Giovanni Boero ([email protected]).
Reconfigurable Photonic Integrated Circuits
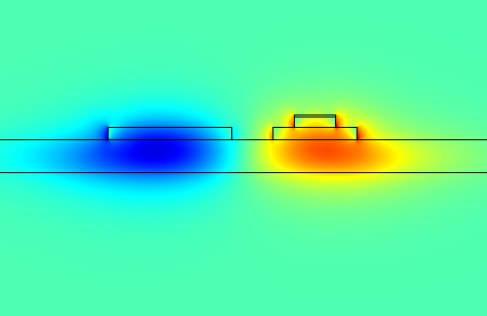
Photonic equivalent of FPGA, Reconfigurable PICs can be implemented by using different physical mechanisms at nanoscale. We focus on the integration of Phase Change Materials on the standard silicon photonics platform to provide non-volatile components and on-chip photonic functions and systems.
Unfortunately, no specific student project is currently available on this topic. Nevertheless, LMIS1 strongly encourages proactive students, interested in our research, to get in contact with us for eventually discussing about “out-of-the-box” intuitions and ideas. In the case you are motivated to carry out a student project, please, directly contact Dr. Hernan Furci ([email protected]).