Numerical simulations of the Laser Powder Bed Fusion (LPBF) process are performed with a dedicated in-house finite element (FEM) code by Dr. Eric Boillat. The heat transfer is described by the evolution of two fields: the enthalpy per unit mass and the temperature.
The laser beam is modelled as a surface heat source for bulk and liquid and a volume heat source for powders. The powder bed is considered as a homogeneous medium with averaged (so-called effective) properties such as absorptivity, thermal conductivity, optical penetration depth, density.
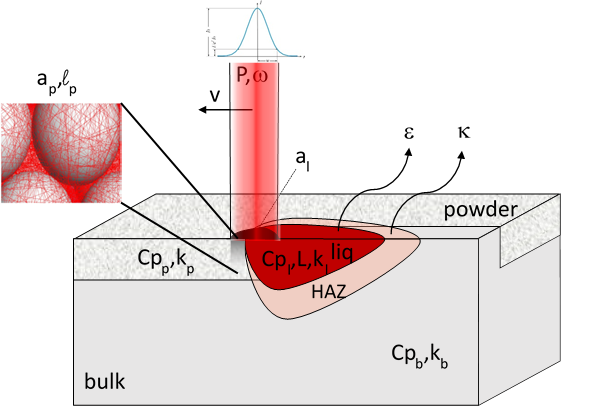
The mesh consists of a fixed coarse mesh on the whole domain and a refined moving mesh around the laser spot to get the needed accuracy for the computation of thermal conduction within the powder and at the interface between the powder and the bulk solid or liquid.
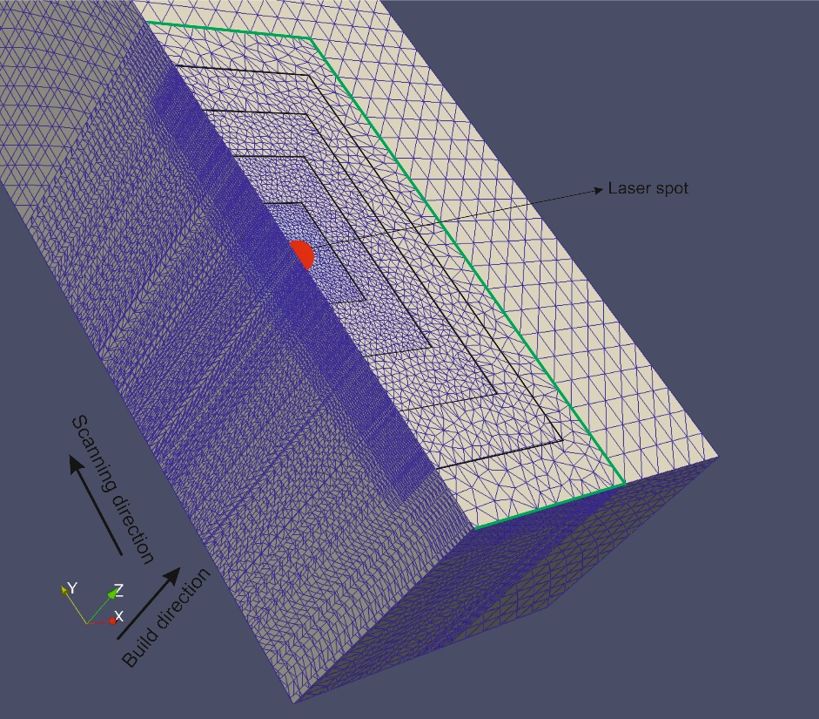
For a precise description of the LPBF process a new field is introduced. This field is called sintering potential and contains the information about the state of the material during LPBF. Its value is 0 in loose powder; 1 corresponds to a fully dense bulk material.
The effective thermal conductivity k depends on the sintering potential: k=k(Φ). During LPBF the effective thermal conductivity of a medium evolves from the value kp of a loose powder to the value kb corresponding to a bulk material and can be connected to the sintering potential Φ by interpolating between kp and kb :
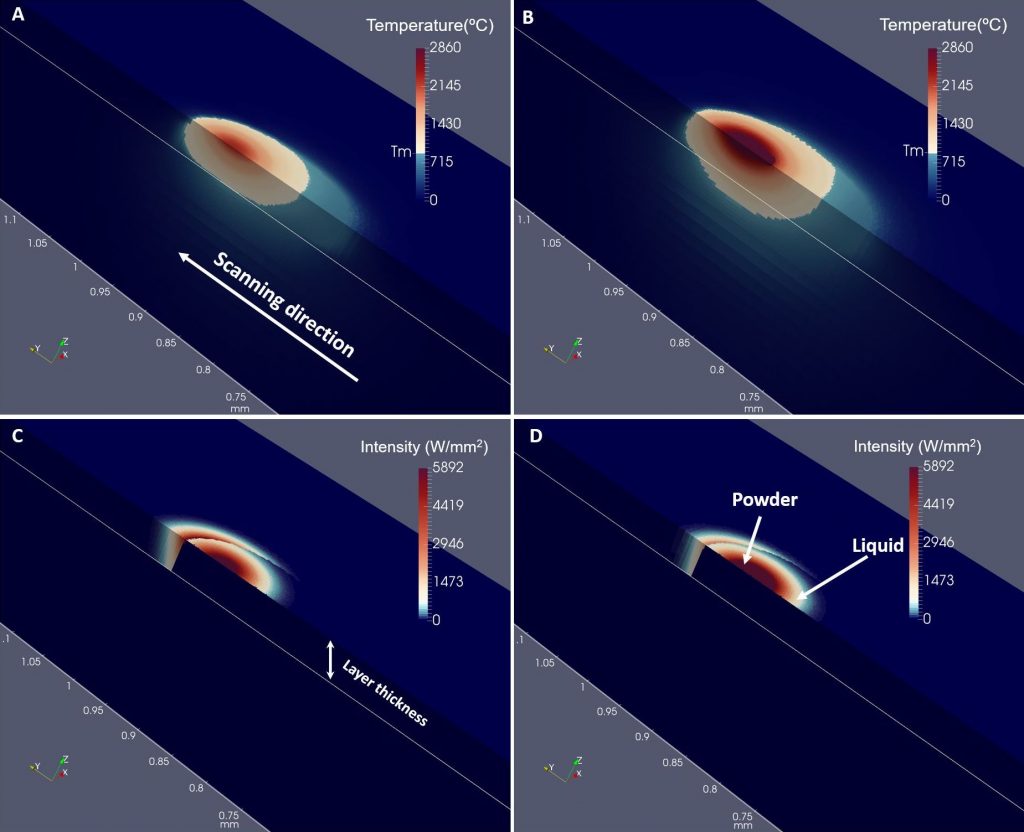
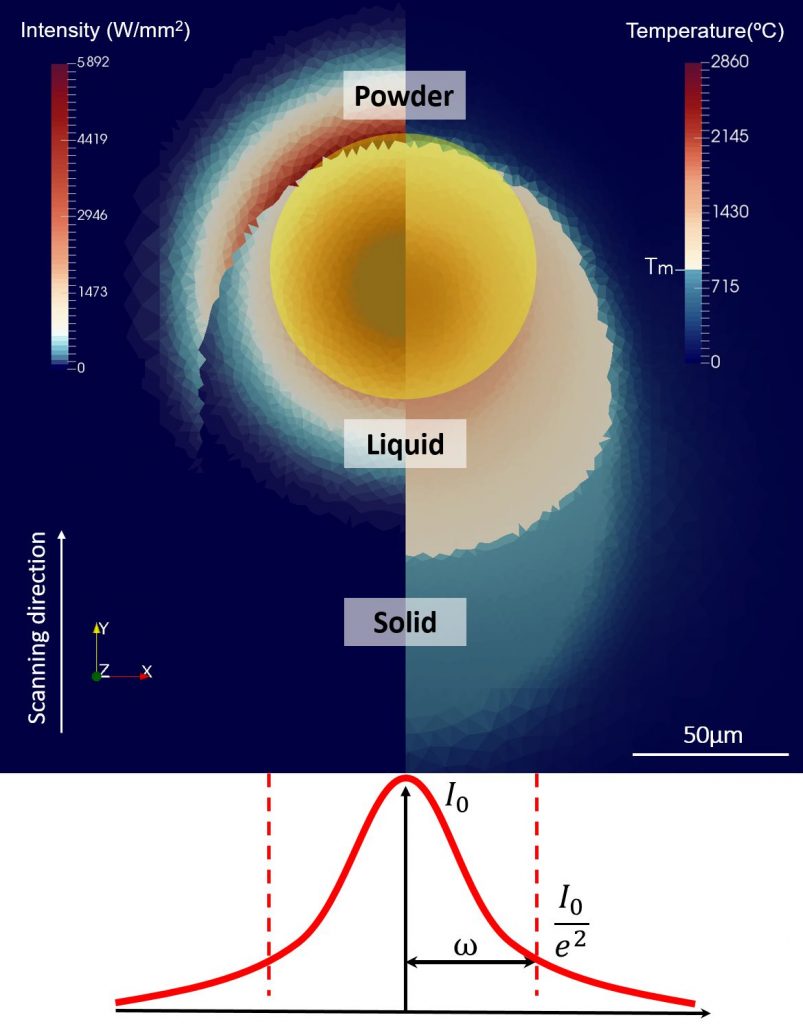
Related publications
B. Meylan, A. Masserey, E. Boillat, I. Calderon, K. Wasmer. Thermal Modelling and Experimental Validation in the Perspective of Tool Steel Laser Polishing. Applied Science, 2022, 12, 8409. https://doi.org/10.3390/app12178409.
H. Ghasemi-Tabasi, C. de Formanoir, S. Van Petegem, J. Jhabvala, S. Hocine, E. Boillat, N. Sohrabi, F. Marone, D. Grolimund, H. Van Swygenhoven, R. E. Logé, Direct observation of crack formation mechanisms with operando Laser Powder Bed Fusion X-ray imaging, Additive Manufacturing, Volume 51, 2022, 102619, ISSN 2214-8604, https://doi.org/10.1016/j.addma.2022.102619.
N. Sohrabi, J. Jhabvala, G. Ku., M. Stoica, A. Parrilli, S. Berns, E. Polatidis, S. Van Petegem, S. Hugon, A. Neels, J. F. Löffler, R. E. Logé, Characterization, mechanical properties and dimensional accuracy of a Zr-based bulk metallic glass manufactured via laser powder-bed fusion, Materials & Design, Volume 199, 2021, 109400, ISSN 0264-1275, https://doi.org/10.1016/j.matdes.2020.109400.
H. Ghasemi-Tabasi, J. Jhabvala, E. Boillat, T. Ivas, R. Drissi-Daoudi, R. E. Logé, An effective rule for translating optimal selective laser melting processing parameters from one material to another, Additive Manufacturing, Volume 36, 2020, 101496, ISSN 2214-8604, https://doi.org/10.1016/j.addma.2020.101496.
T. Polivnikova, E. Boillat, R. Glardon, Study and Modelling of the Melt Pool Dynamics during Selective Laser Sintering and Melting, EPFL PhD thesis, 2015. https://infoscience.epfl.ch/record/213654.
S. Kolossov, E. Boillat, R. Glardon, Non-linear model and finite element simulation of the selective laser sintering process, EPFL PhD thesis, 2005. https://infoscience.epfl.ch/record/33647.
S. Kolossov, E. Boillat, R. Glardon, P. Fischer, M. Locher, 3D FE simulation for temperature evolution in the selective laser sintering process, International Journal of Machine Tools and Manufacture, Volume 44, Issues 2–3, 2004, Pages 117-123, ISSN 0890-6955. https://doi.org/10.1016/j.ijmachtools.2003.10.019.
E. Boillat, Finite element methods on non-conforming grids by penalizing the matching constraint, ESAIM M2AN. 37 (2003) 357–372. https://doi.org/10.1051/m2an:2003031.