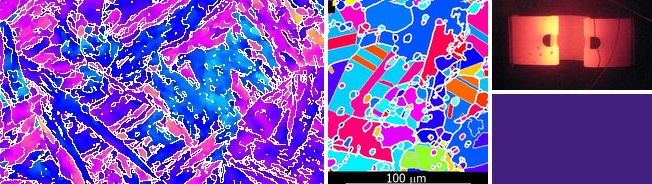
Research field
Research activities are focused on the control and design of microstructures in metals and alloys through a combination of thermal and mechanical treatments. Different microstructure phenomena are experimentally quantified, and analytically or numerically modelled at different scales. Phenomena of interest include recrystallization, grain growth, twinning, texture evolutions, precipitation, and phase transformations, under variable temperature conditions, and with the possibility of concurrent plastic deformation. Beyond the investigation of mechanisms underlying microstructure evolutions, and their modelling, a systematic link is made between the microstructures and the corresponding structural or functional properties of the material. Applications concern bulk/sheet forming, powder metallurgy and additive manufacturing.
Tools
Facilities at LMTM include optical and electronic microscopy (SEM-EBSD), heat treatment furnaces, a prototype selective laser melting system for metal powders, a Shock Peening laser, and a Gleeble 3800 machine.
The Gleeble machine allows reproducing experimentally, and in laboratory conditions, the temperature history and strain path undergone by a material through thermo-mechanical processing, which is essential for the understanding and optimization of forming operations. Reversely, on a more fundamental point of view, complex mechanical and thermal paths may be designed in order to induce microstructures with unusual features and properties, which can then lead to new processing routes.
The Selective Laser Melting (SLM) platform is used with a number of metallic alloys, including precious metals, stainless steel, bronze and metallic glasses. The SLM process is also combined with Laser Shock Peening (LSP) treatments such as to better control residual stresses and microstructures in 3D.