The fibre mat production is performed in several institutes. The scintillating fibres are first delivered by the firm Kuraray in Japan to CERN where they are qualified and processed. The four production centres located in Lausanne, Aachen, Dortmund and Moscow then produce the mats and perform quality assurance tests. The finalised are finally sent to one of the module centres in Amsterdam or Heidelberg where they are assembled together with the SiPMs and the cooling system. The LPHE is strongly involved in the production and produced approximately one third of the mats needed for the finalisation of the SciFi project.
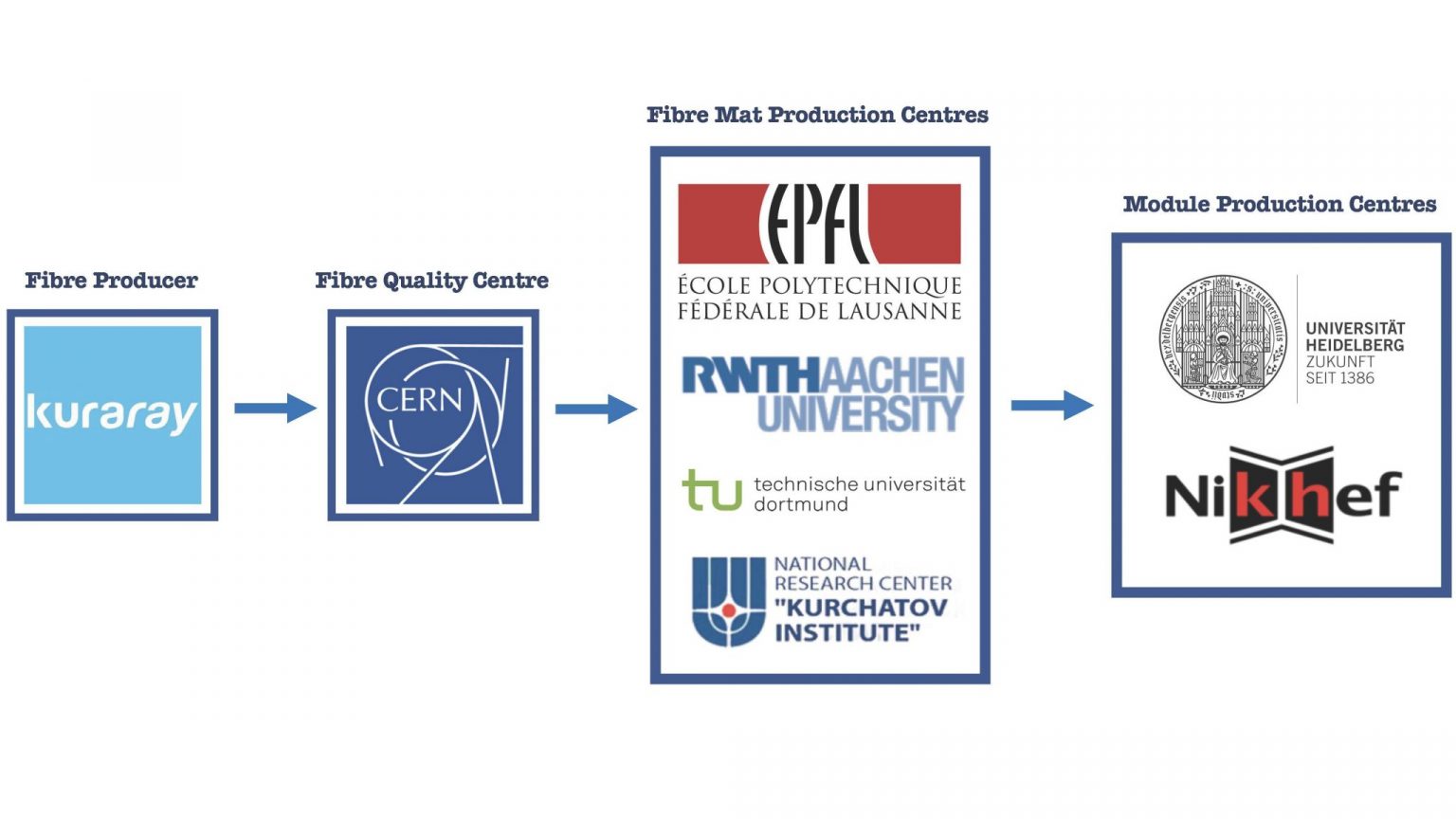
The SciFi Mat Production
The fibres are delivered to Lausanne in the form of fibre spools. A partially automated Winding Machine is then exploited to arrange and glue six layers of fibres onto a threaded wheel. The latter has 11 pin holes. Hence, by filling the holes with glue, the resulting mat has 11 pins which are crucial for positioning inside the SciFi modules. After the winding process, a first lamination is performed and consists in gluing a kapton foil onto the side of the mat without pins. The mat is then cured during 20h in a room with controlled temperature and humidity. The fibre mat is freed from its wheel during the unforming process. Any transversal bending can be removed thanks to a tempering stage where the mat is heated during 2h at 40C. A second lamination is then be performed onto the side of the mat with pins. Polycarbonate endpieces are glued at both ends of the mat to provide a reliable coupling to the SiPMs and to fix the mat inside the module. Optical cuts are then made with a diamond milling tool to both ends of the mat. Using a high-resolution scanner, an optical scan is performed on both ends of the mat. It permits a control of the geometry, the quality of the optical cuts, and the optical transparency of the fibres. A mirror foil is then glued to the non-readout end of the mat to increase the number of photons detected by the SiPMs by 60 to 80%. Light Yield (LY) scans are performed before and after the mirror gluing. These measurements quantify the mat response to ionising particles by using β particles from a Strontium 90 source. Finally, during a Quality Assurance (QA) stage, each mat is carefully evaluated before being shipped to a module production centre.