B058——————————————————————————
Receding horizon optimization and disturbance estimation of a Redox flow battery
In the development of efficient smart grid technologies, fast and reliable storage of electrical excess energy provided by the grid is key to ensure efficiency.
This project is in collaboration with the Laboratory of Physical and Analytical Electrochemistry of Prof. Hubert Girault and the electricity distributor Sinergy in Martigny. It is proposed to investigate the potential of dual-circuit redox flow batteries as a storage mean for electrical excess energy. The project includes:
- Development of a basic dynamic model of a redox-flow battery;
- Formulation of a dynamic optimization problem to minimize the losses for varying load profiles;
- Numerical solution to the optimization problem;
- Verification on a real system available at Martigny
Requirements : Suitable candidates should have a good background in control and optimization. Basic knowledge of thermodynamic and electrochemistry would be a plus. This project is intended to start as soon as possible.
Professor: Dominique Bonvin
Type of project: Master
Student: Moritz Mittelvief Hous
Contacts: Timm Faulwasser (Optimization), Julien Billeter (Modeling)
B057——————————————————————————–
Working frequency influence of piezoelectric ultrasonic devices for dental application
During a first training period, we developed new transducer based on the actual geometry (λ/2 transducer), working at frequency between 18 kHz to 50 kHz. Due to the dimension of the stack, we can’t be able to go higher to 50 kHz with this kind of transducer. We designed also λ transducers with working frequency included in the range [40 kHz – 60 kHz]. A second step of this first period is to consider a specific mechanical bench to characterize the behavior of these transducers and to integrate them to make comparisons with the actual gold standard. The first goal of the project is to make a laboratory driving system based on Labview software to drive the previous transducers. In fact, we need to develop a new structure to drive the transducers at these frequencies and to better control the initial frequency tracking and the regulation during functioning. After this step, we need to estimate the mechanical amplitude at the end of the tip and their motions in function of the frequency used. We must be able to characterize the low amplitude and high speed motions of the tip and to analyze the results obtain in function of vibration modes of the instrument and the excitation of the transducer. Analytic and FEM analyzes will be engaged to better understand the vibration characteristics and we probably need to modify the geometry of the tip to adapt the vibration to the new frequencies. We will consider the requirements of the application for different clinical cases and try to evaluate the improvement on each case.
In this project, we will consider chemical production plants with high electrical heating/cooling demand, and develop methods to assess and exploit their demand response potential by shifting the power consumption profile of a batch production. In particular, we will explore the effect of demand response on the optimal operation of the chemical plant and investigate the economic feasibility.
Requirements: Due to the pluridisciplinarity of the project, electrical and mechanical skills will be strongly appreciated. The student must be curious, takes initiatives and appreciates experimental works.
Professor: Dominique Bonvin
Type of project: Master
Student: Maxime Valdemarin
Contact: Philippe Mullhaupt
K052——————————————————————————-
Robust controllers for blending processes with large time delays
Blending of raw materials to achieve a desired product quality continuously or for a batch (e.g. container, silo, pile) is important in many industrial domains such as food, beverage, mining, chemical, energy, and cement. If the raw material compositions vary significantly, a fixed recipe for the raw material feeder proportions cannot be applied anymore. Instead, the raw material proportions are typically adjusted automatically based on the composition of the blended product measured on-line or at-line. Typically, raw materials with low quality variability (e.g., high grades, correctives) are used to correct quality changes of bulk raw materials with large variability (e.g., low grades, from quarries or mines).
In this project, the applications in the cement industry is studied using a MIMO controller: (i) in raw mills of the cement industry, the manipulated variables are the feeder flowrates of the raw materials (e.g. limestone, clay, sand, iron ore), the controlled variables are nonlinear functions of the product oxides, and the measurement device is an at-line XRF spectrometer with significant transport and measurement delay.
Recently, a new robust controller design using frequency-domain data has been proposed in the Automatic Control Laboratory of EPFL. This method is based on loop-shaping in the Nyquist diagram under infinity norm constraints on closed-loop MIMO transfer functions (Galdos et al. 2010). Various types of robust MIMO controllers for the case of varying input material compositions and large time delays have been designed using convex optimization techniques (de Oliviera 2011; Oliveira, Amrhein et al. 2011; Dreyfus 2017).
The aim of this project is to apply this method to the design of blending controllers for plants with large, possibly varying time delays as well as low-frequency averaged measurements. A novel multi-rate robust controller and a robust Smith-Predictor controller will be compared in terms of stability and performance for the two MIMO applications. Simulations will be done off-line in Matlab/Simulink using a simplified model and in real-time using a link to Siemens Simatic WinAC using a nonlinear model implemented in O_Blend.
MER: Alireza Karimi
Type of project: Semester
Student: Paul Dreyfus
Contact: Dr. Michael Amrhein
MC001——————————————————————————–
Control of a triple arm inverted pendulum
The LA recently upgraded its single arm inverted pendulum into a triple arm inverted pendulum. The mechanical part as well as the measurements part are now completed. The fun part can begging. The challenge of this project is to control the triple inverted pendulum. Control scenarios will first be simulated using mathematica and/or matlab The implemented and validated using LabVIEW.
This project requires the following courses: Control Systems or Automatic and Commande Multivariable or equivalent. Nonlinear control will be a plus.
Teacher: Philippe Mullhaupt and Christoph Salzmann
Type of project: Semester
Students: Philippe Schuchert, Fredric Nguyen, Alic Kaufmann
Contact: Christoph Salzmann and Ehsan Sarshari
B061——————————————————————————–
Real-time optimization of a fuel cell stack via machine learning
Fuel cells are devices that provide clean energy at high efficiencies and have a wide spectrum of small to large-scale applications. Due to their complexity, operating at high efficiency while tracking the demanded electric power is not an easy task. Moreover, SOFC stacks must be operated at certain conditions in order to increase their lifetime and durability.
Video of the SOFC’s working principle:www.youtube.com/watch
The main objective of this project is to combine a real-time optimization (RTO) scheme with machine learning. More specifically, the objectives of this project are the following:
- Study the RTO approaches that are applied to SOFC systems.
- Learn how to use the machine-learning toolbox from Matlab.
- Couple an RTO scheme with machine learning.
- Implement the proposed RTO scheme using an appropriate formulation.
- Simulate the proposed RTO scheme applied to an SOFC stack.
Candidates should have a good background in Matlab programming, control and optimization. Some knowledge of fuels cells would be a plus.
Professor: Dominique Bonvin, Jan van Herle
Type of project: Semester
Student: Vinzenz Minnig
Contact: Tafarel de Avila Ferreira, Alejandro Marchetti, Harsh Ambarishkumar Shukla
J048——————————————————————————-
Optimal control for battery management systems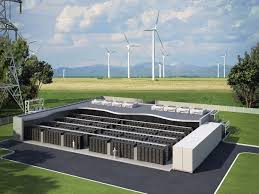
The sustainable prospect of the modern Power Grid relies heavily on efficient, reliable and smart energy storage solutions. To this end, high capacity chemical batteries are increasingly being used for advanced control tasks such as supporting the power grid for frequency and voltage control. Laboratoire d’Automatique is on the leading edge of research on developing methods for the optimal operation of energy storage systems for the provision of Ancillary Services to the Power Grid.
In energy storage research, the models used do not include the auxiliary equipment of a utility scale installation. In industrial practice a utility storage system includes power electronics, multiple battery cells and cooling systems operated by a Battery Management System (BMS). The BMS is a crucial component, responsible for the healthy operation of the battery and the coordination of the installation equipment by taking into account phenomena such as internal heat generation and the ageing of the battery.
The project goal is to model a utility scale battery installation with a cooling system and develop optimal control methods that allow the BMS to provide frequency regulation services to the Power Grid with minimum battery damage.
Prior Knowledge : Optimization, Control, Modeling of thermal and electric systems, Matlab
Professor: Colin Jones
Type of project: Semester
Students: Danjiao Ma, Alberto Bonelli
Contact: Ioannis Lymperopoulos
K039——————————————————————————–
Control of an air-Hockey robot
Over the previous semesters we have designed and built a basic framework for a robot that is able to play air-hockey. A good control scheme has been developed and implemented, but there is still need for improvement.
The aim of this project will be to refine and optimize the existing controller in order to provide good path-following. Additional tasks involve the implementation of a static friction compensator and backlash correction. The controller will be implemented in Labview.
The student should be familiar with advanced control techniques, Matlab and Labview.
MER: Alireza Karimi
Type of project: Semester
Student: Thomas Zilliox
Contact: Christoph Kammer
J041——————————————————————————–
Identification and control for riderless motorcycles
Controlling a riderless motorcycle is a challenging task as the dynamics are highly nonlinear and non-minimum phase. Moreover, suspension or chain pull effect make the dynamics more complicated to model accurately.
In the first phase of this project, we will focus on hardware and software design for the autonomous control of a real Thunder Tiger motorcycle.
After that, based on simulations and literature, we will investigate the proper modelling of a motorcycle. The next task will be to perform system identification experiments. In the last phase, we will design and compare different controllers that will be implemented on the Thunder Tiger motorcycle.
Skills: Matlab, Control systems, System Identification and enthusiasm !
Professor: Colin Jones
Type of project: Semester
Students: Pascal Dillier, Simon Dedry
Contact: Luca Fabietti and Shukla Harsh Ambarishkumar
J046——————————————————————————-
Modeling and control of airborne wind energy systems
Wind resources tend to be significantly stronger and more consistent with increasing altitude. Furthermore conventional wind turbines quickly reach their limit in accessing these higher winds due to structural limitations. This creates a potential for improved power generation with Airborne Wind Energy systems. A frequent design for such systems includes a flying airfoil tethered to a ground station. The station is equipped with a power generator and the aerodynamic force generated by the flying wing is used to drive this generator as the tether reels out under the aerodynamic force. Once the tether reaches its maximum length the wing enters a low force generating gliding trajectory and the tether is reeled back in with low power consumption, thus generating a net positive power generation cycle.
The execution of such motion however requires overcoming critical control challenges and perform control and optimization for improved power generation in presence of system and environmental (wind) uncertainties. The proposed project will provide opportunities to students to work on different aspects of the system and has several subprojects as listed below:
- System modeling and nonlinear control:Will explore methods for modeling the system for better control and will explore the tools of robust and adaptive nonlinear control theory to implement controllers for the existing experimental platforms.
- Path following model predictive control: Will implement and test model predictive control (MPC) schemes for tracking of power optimal trajectories in the experimental system.
- Data based modeling and control of experimental systems: We will explore the use of Gaussian Process Machine Learning tools to model the dynamics and performance characteristics of the system to find the optimal control inputs for the system. The learning based models further provide an improved prediction performance crucial for the model based control methods explored above.
Realistic high fidelity simulators and working experimental platforms are ready and will be available to bench test the controllers and learning algorithms on the real system.
Professor: Colin Jones
Type of project: Semester
Students: Florian Reinhard, Yingzhao Lian
Contact: Sanket Diwale, Petr Listov and Ioannis Lymperopoulos
J037——————————————————————————–
Fast Toy Lab – Control of a micro scale truck for automatic racing using MPC
The Fast Toy Lab is developing a high-speed, micro-scale autonomous course for small-scale RC cars. We are aiming at producing extremely fast and tiny cars and controllers capable of racing against all comers!
This project will design a autonomous car for racing task based on a new 1:27 scale Min-Z car. The student will integrate an IMU board for communication and control onto the Min-Z car and identify the model of the modified car.
Followings are the possible steps for the project:
- Survey literatures for race car design.
- Integrate IMU board (for communication and control) and encoders to the car.
- Identify the model for the new 4-wheel driven car and develop simulation platform.
- Investigate control strategies, if time permits.
Requirements: Knowledge of Control Theory and Electronics and Matlab
Professor: Colin Jones
Type of project: Semester
Student: Christopher Boux de Casson
Contact: Shukla Harsh Ambarishkumar
K027—————————————————————————-
Quadropter demonstrator design and programming
The goal of this project is to modify and program a quadcopter such that it can be used as a demonstrator in future control systems courses. This includes modifying the hardware to include an additional range sensor, designing a basic controller and programming a bluetooth interface such that the quadcopter can be steered from a PC or smartphone.
MER: Alireza Karimi
Type of project: Semester
Student: Mathieu Valceschini
Contact: Christoph Kammer , Predrag Milosavljevic
K043——————————————————————————-
Multivariable robust control of centrifugal compressors
Centrifugal compressors play a very important role in the oil and gas industry and as such increasing the availability of these machines is a major goal for their operators. The safe operating envelope of centrifugal compressors is defined by the constraints due to surge and choke phenomena as well as the minimum and maximum rotational speed limits. This fact, coupled with the limitations on pressure rise per stage and with economic considerations, leads to process designs utilizing compressors in series and parallel configurations or in various combinations of both to meet the operability requirements in a flexible way.
These complex arrangements pose significant challenges from a control engineering point of view. The interactions between anti-surge and throughput or process control loops that are already present in a single compressor become more difficult to handle when multiple compressors are to be considered. Poor control designs can lead to anything from undesirable oscillations in process operating conditions to cascaded surge events and complete plant shut-downs.
In this project we consider parallel and series configuration of compressor plants to design robust multivariable controllers using a frequency domain approach. The results are compared with the model predictive control (MPC) solutions
MER: Alireza Karimi
Type of project: Semester
Student: Ludovic La Placa
![]() |
This project is carried out in collaboration with ABB Corporate Research in Switzerland. |
B064——————————————————————————–
Optimization of gas compressors station
The aim of the project is to explore a few very recent algorithms in distributed optimization and utilize them for solving compressor load sharing optimization problem. Load sharing optimization solves the problem of distributing the load among several compressors while at the same time satisfying operational constraints, user constraints and minimizing the consumption of the station. In a typical gas pipeline application several compressor units are interconnected and operated together to meet station set point requirements. The structure of the problem is special and can therefore be exploited by formulating and solving the problem using methods for distributed optimization. The student is expected to understand the theoretical content of the methods.
We consider parallel and series configuration of compressor plants to implement distributed algorithm to handle the interactions among compressors with the different variables and the operational constraints. The project work should include the consideration of hierarchical arrangement possibilities between real time optimization (RTO) layer and low-level controllers. The overview of the project should be based on the following points:
- Implementation of the algorithm for distributed optimization on a model of a system with interconnected units.
- Scheduling the gas compressor plant into different structures of interconnected units/compressors.
- Testing the algorithm for distributed optimization on the gas compressor plant.
The project will be done in simulations, but on the model of practical relevance for the industry.
Requirements: Background in MATLAB programming, control theory and optimization.
Professor: Dominique Bonvin
Type of project: Semester
Students: Oussama Zouaghia, Alberto Rigamonti
Contact: Predrag Milosavljevic
B065——————————————————————————–
Application of Real-Time Optimization to the path following problem
The objective of path following is to follow a reference geometric shape (for e.g., a circle) in minimum time. Many industrial robot tasks, such as welding, glueing, laser cutting, and milling can be casted as path-following problems. Often, an optimization problem is solved to find the minimum time while satisfying constraints and system dynamics. The challenge in defining minimum time trajectories arises due to uncertainty in system dynamics. Traditionally, this challenge is overcome by using state feedback to update the system dynamics and remove uncertainty.
Real-time optimization (RTO) attempts to remove the uncertainty by adapting the optimization problem instead of updating the system dynamics. The goal of the project is modeling and optimization of a 3 DoF robotic arm and comparing RTO approach with traditional path following approach. A good background in Matlab programming, control and optimization is desired.
Professor: Dominique Bonvin
Type of project: Semester
Student: Peter Lichard
Contact: Ehsan Sarshari and Martand Singhal
B063—————————————————————————–
Optimal operation of an industrial batch distillation column
Batch distillation is a separation process widely used in the specialty chemistry because of its flexibility for separating components of different relative volatility. In the case of multi-product plants, the operating conditions can vary significantly from products to products. Hence, the operation of a batch distillation column needs to be adapted to the characteristics of the products being separated. This project aims at developing a generic operational strategy that is capable of optimizing the separation of the various mixtures while enforcing safety and quality constraints.
Based on an existing dynamic model, the student will first implement and test in simulation various strategies to control the pressure and the temperature at the top of the column and the gas flow through the column. Optimal operation will then be achieved by generating optimal controller setpoints on the basis of measurements.
This project is carried out in collaboration with the Firmenich Company in Geneva, but most of the work will be done in the Laboratoire d’Automatique of EPFL by simulation using Matlab.
Professor: Dominique Bonvin
Type of project: Master
Contact: Dr. Michael Amrhein
![]() |
Most of the work will be done at the Laboratoire d’automatique of EPFL, with occasional visits to Firmenich in Geneva. |