The wind tunnel test section designed for turbulent boundary layer flows measures 28 meters in length, 2.5 meters in width and 2 meters in height. The closed-loop wind tunnel is powered by a 130 kW fan which enables a maximum wind speed of 25 m/s. A natural boundary layer develops over the surface of the test section, which resembles the boundary layer found in real atmosphere under neutral stratification. A thermal control system capable of heating/cooling the test section floor and 16 individual layers of air at the inlet of the test section facilitates study of thermally stratified turbulent boundary layers.
With a focus on wind energy, the wind tunnel is actively utilized to study the interaction of wind turbines and their wakes with turbulent boundary layers under different thermal stabilities. The long test section can be used to investigate flow development in large wind farms. Active topics under experimental investigation include wind turbine wakes in yaw control, vertical axis wind turbine (VAWT) wakes, flow in complex terrain and its interaction with wind turbine wakes, and flow development in wind farms. Results from these studies provide useful insights into the complex nature of flow physics of wind turbine wakes and are used for validation of numerical and theoretical models.
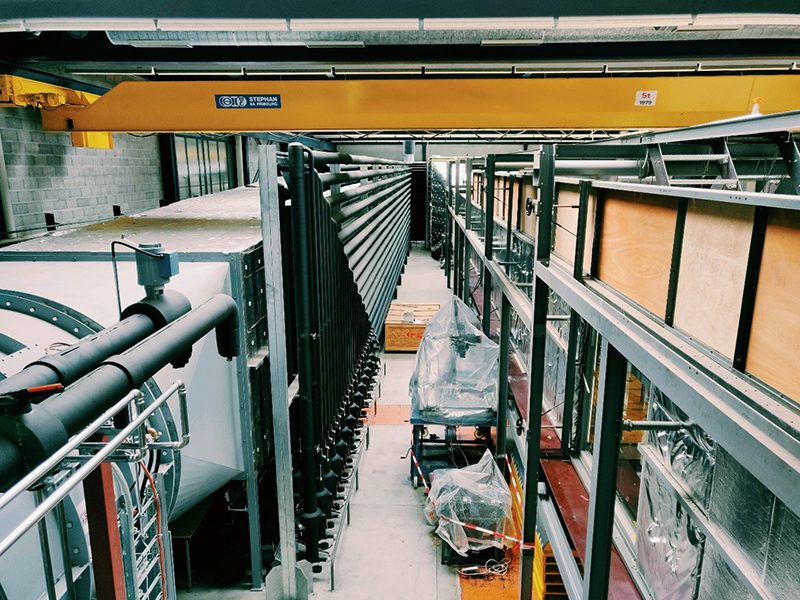
Flow Measurement Techniques
The laboratory is equipped with a wide range of state-of-the-art flow measurement techniques. These include:
- Particle-image velocimetry
- Laser doppler velocimetry
- Hot- and cold-wire anemometer
- Cobra probe
- Pitot tube
Particle-image velocimetry (PIV)
A PIV system developed by LaVision is extensively used for spatially resolved flow fields. The PIV system consists of a 435 mJ dual-head Nd:YAG laser, 16-bit sCMOS cameras, 29 MP CCD cameras and Helium filled soap bubble generator. The system can be used for planar, stereoscopic and tomographic PIV measurements.
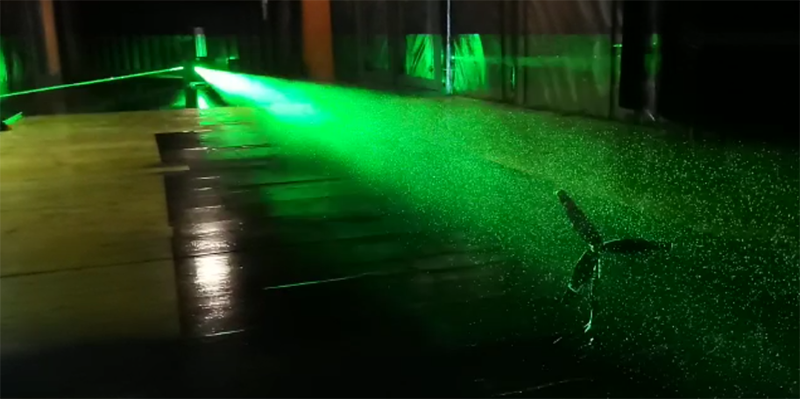
Laser Doppler Velocimetry (LDV)
A three-component LDV system developed by TSI is used for highly accurate, temporally resolved point measurements of the velocity vector. The system shoots three pairs of monochromatic laser beams at distinct wavelengths, which coincide at the desired measurement location. Its non-intrusive nature and high temporal resolution makes it useful for studying turbulence spectra, higher order moments and dynamic characteristics of turbulent flows
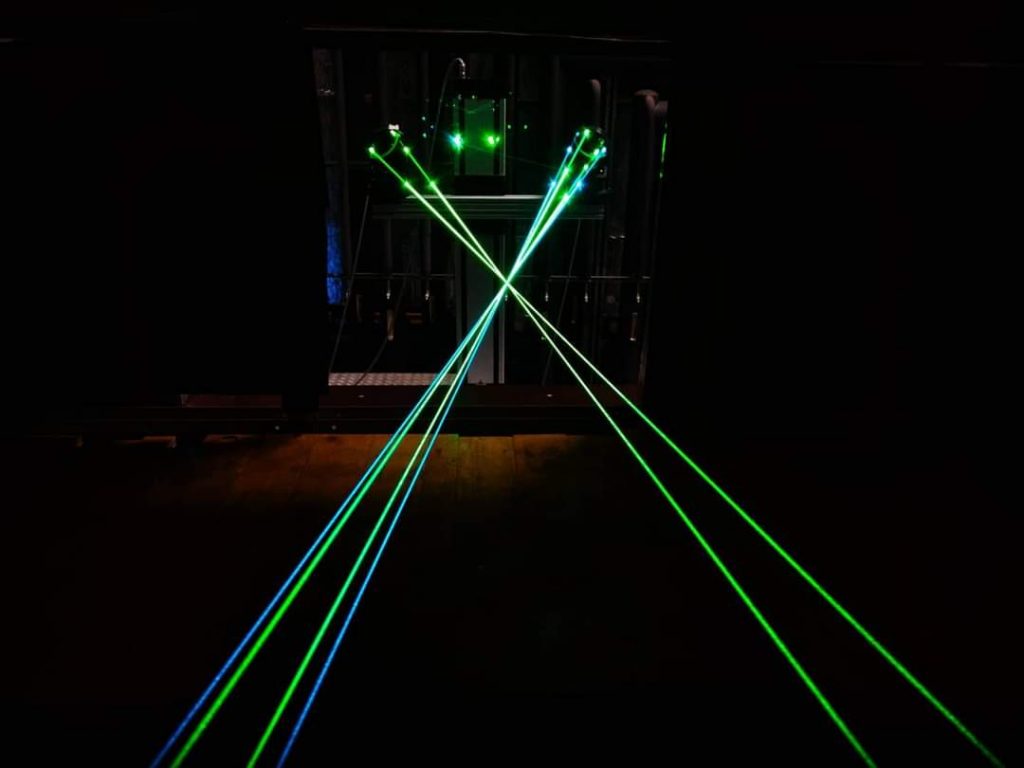
Hot- and Cold-Wire Anemometer
Hot-wire is one of the most traditional velocity measurement devices in experimental fluid mechanics. At WiRE, we possess single wire (1 velocity component), double (cross) wire (2 velocity components) hot wire anemometers, as well as, a combination of x-type hot-wire and single cold-wire for simultaneous measurements of velocity and temperature. These anemometers provide high temporal resolution point measurements; however, they are intrusive in nature and need constant calibration.
Cobra Probe
Cobra probes are pre-calibrated point measurement devices, which provide three-components of velocity at a sampling rate of several hundred Hz. They are suitable for measurement of turbulence characteristics, however, cannot measure reverse flows.
Pitot Tube
A pitot tube is available for measuring flow velocity. It is commonly used to estimate mean velocity at a point to provide a reference velocity for e.g., power and force coefficient measurements of the wind turbine models.
Wind Turbine Models
At WiRE, we develop miniature wind turbine models which are designed for experiments on a laboratory scale. Special attention is given to the power and thrust coefficient similarity between the full-scale commercial wind turbines and our experimental models.
Horizontal Axis Wind Turbine – WiRE 01
A three-bladed horizontal axis wind turbine (HAWT) model with a rotor diameter of 15 cm and hub height of 12.5 cm is used for studying HAWT wakes. The rotor is paired with a direct current machine, which acts as the nacelle of the turbine, to perform power measurements. At optimum conditions, the miniature turbine can achieve a power coefficient of 0.4 and a thrust coefficient of 0.8.
Vertical Axis Wind Turbine
Laboratory scale vertical axis wind turbines (VAWT) often suffer from extremely low power coefficients. To overcome this limitation, a variably-pitched VAWT is designed to improve the power performance. The blades of the turbine are connected to bearings which follow a prescribed track built into the structure below the rotor. This optimizes the angle of attack of the blades as they rotate, thus providing higher power extraction from the incoming wind.
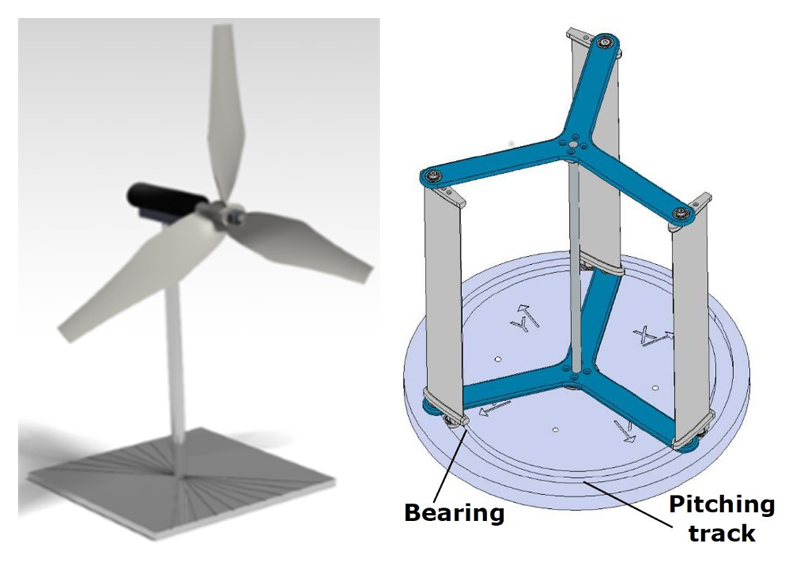