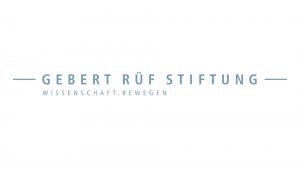
A Graphene-based Gas Analyzer
The emission of harmful gases, either deliberate or by accident, can cost both money and human lives. To mitigate the impact of such events, it is necessary for the emergency responders (e.g. firefighters, police, military) to have a prompt analysis of the situation, in particular knowing which gases are present and in what concentrations. It is therefore crucial to develop gas sensors that are: highly sensitive (capable of detecting tiny concentration changes) and selective (capable of discerning between different gases), fast and portable (real-time information all-around the event’s site).
Graphene (a carbon monolayer) is a novel material that in late-years has received a lot of attention for its exciting possibilities in many disciplines. In particular, it holds a great potential for gas sensing applications as both its mechanical and electrical properties change significantly when gas molecules are adsorbed to its surface. Combining electrical and mechanical measurements of a graphene-based sensor together with a gas micro-column (a long micro-channel that slows down some gases more than others) will allow the precise identification of the gases in any complex mixture. GraphGAS’ main objective is to develop a prototype of such a graphene-based gas sensor, so that its market potential can be evaluated at the end of the project. In addition, basic knowledge on the fundamental properties of the interactions between gases and graphene will be unveiled along the project, which could lead to new multi-functional systems and applications.
The concept
The basic concept of operation is illustrated in the figure below, and it consists on the combination of a gas µ-column together with one or several graphene NEMS resonators. Both of these stages will be optimized separately. Once optimized, they will be integrated into one whole (and compact) system where the graphene device(s) will receive the partially separated gases from the micro-column while several (e.g. 3) parameters are monitored in parallel. These parameters depend on the amount and type of gas adsorbed on the graphene, but with different ratios, giving information on different characteristics of each molecule. We expect that this will allow a full determination of the concentration and types of gases within the mixture. As an example, 3 parameters that can be monitored are: the resonance frequency of each resonator; the current along the graphene structure; and the low frequency noise of such current.
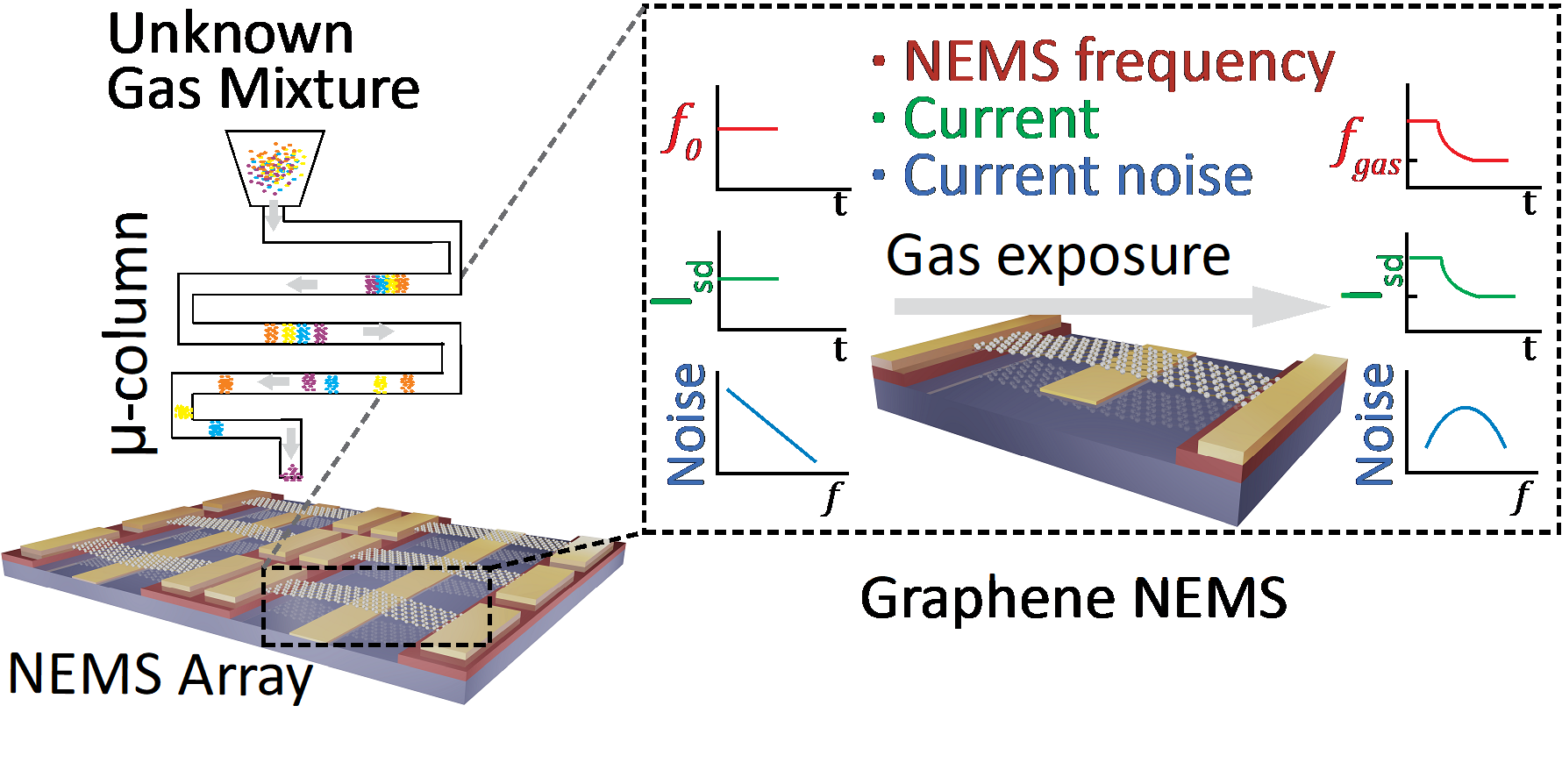
The microcolumn
Gas chromatography systems using microcapillaries have been used since the 1970s. Soon after, with the evolution of microfabrication techniques, the idea of miniaturizing these capillaries into silicon microchannels was laid out and has been the target of research and development for a couple of decades.
Our objective in this part of the project was to design, fabricate and characterize gas microcolumns to be integrated later in the final sensor. To do this, as announced in the project proposal, we collaborated very closely with a local company that has several years of experience in the topic.
The fabrication of the improved microcolumns was performed following the process flow detailed in the figure below, which is an improvement compared to the original columns from Microsens SA because we included the presence of a nozzle at the end of the column. With this, the output is brought much closer to the sensing chip. This was done because the simulations confirmed that the response is better (measured as proportional to the flow that reaches the sensor relative to the total flow) when the distance between the outlet and the sensor is smaller.
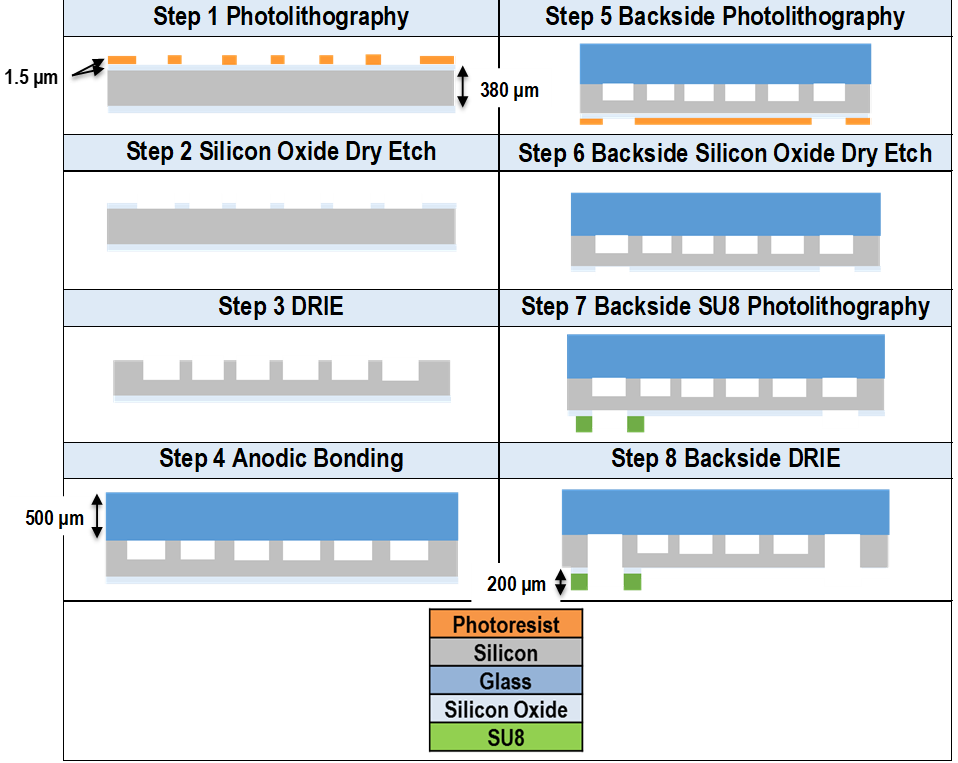
The fabrication of the microcolumns was completed successfully. Thanks to the collaboration with the company, no optimization was required during the critical steps and, in general, very clean and well-defined structures were fabricated (see figure below.a). In some cases, some punctual mistakes were found along the microcolumns (see figure below.b) which is rather normal considering that each column was 2 meters long (everything fitting in a 2cm*2cm area). A full picture of a chip can be seen in figure below.d and details of three different outlet geometries are included in figure below.c.
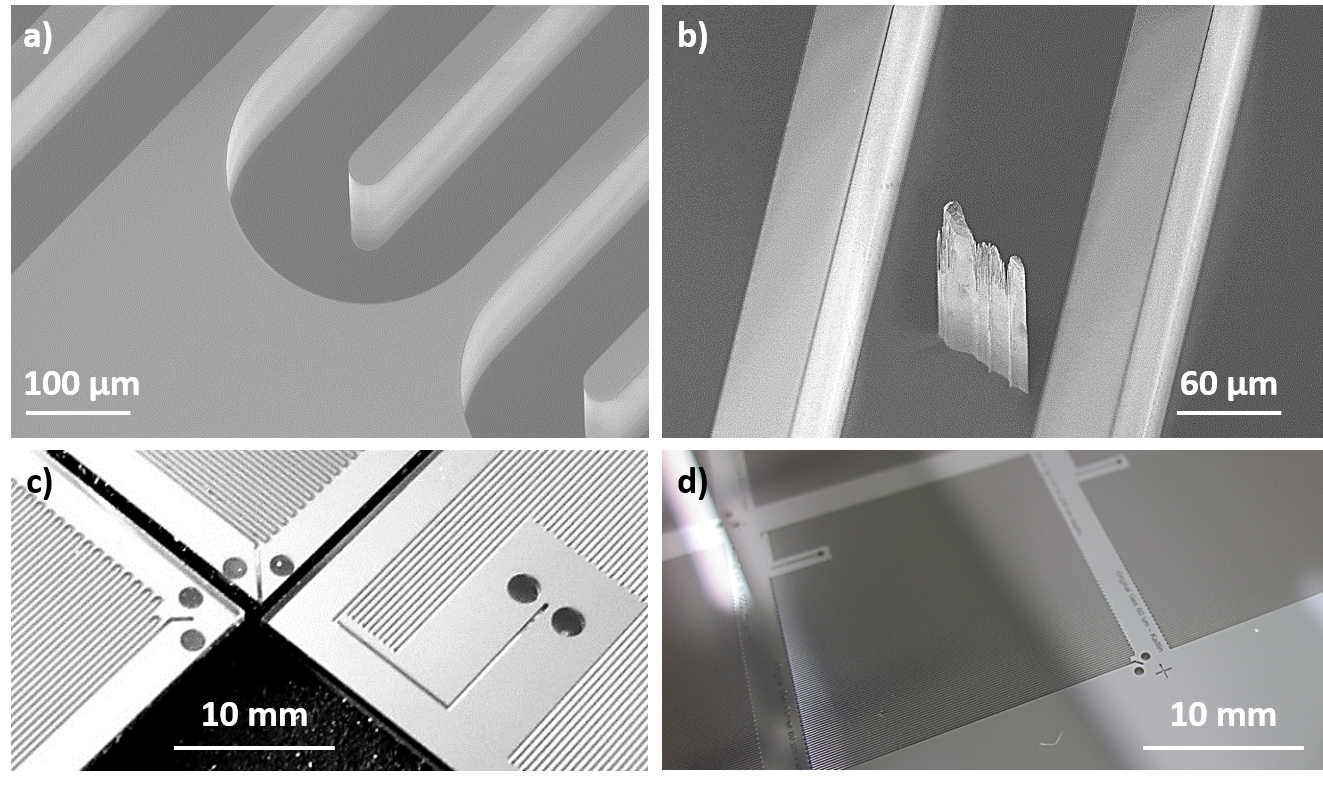
The Graphene Resonators
2D material-based mechanical resonators are typically released through the removal of a sacrificial layer after the 2D material transfer. An alternative approach is to transfer the 2D material directly onto structures with pre-defined cavities, whereby post-transfer processing is minimized. We successfully use this strategy to fabricate circular graphene membranes ranging in diameter from 1.2 μm to 26.5 μm. The fabrication process is illustrated in the figure below. Graphene is first grown via chemical vapor deposition in copper foil. A layer of poly(methyl methacrylate) (PMMA) is spin-coated on top to provide mechanical protection. Graphene on the backside of the foil is etched in an oxygen plasma. Patterned polydimethylsiloxane (PDMS) is mounted on top of the PMMA before etching the copper foil in 5% HCl with a small amount of H2O2 added. The graphene-polymer structure is rinsed thoroughly in filtered DI water and dried in air before transferred onto a silicon chip with holes defined by reactive ion etching, using photoresist as etch mask. The PDMS is peeled off and the PMMA is burned away at 400°C in a hydrogen and argon atmosphere. We used graphene but anticipate that other 2D materials could be used with little or no modification of the process.
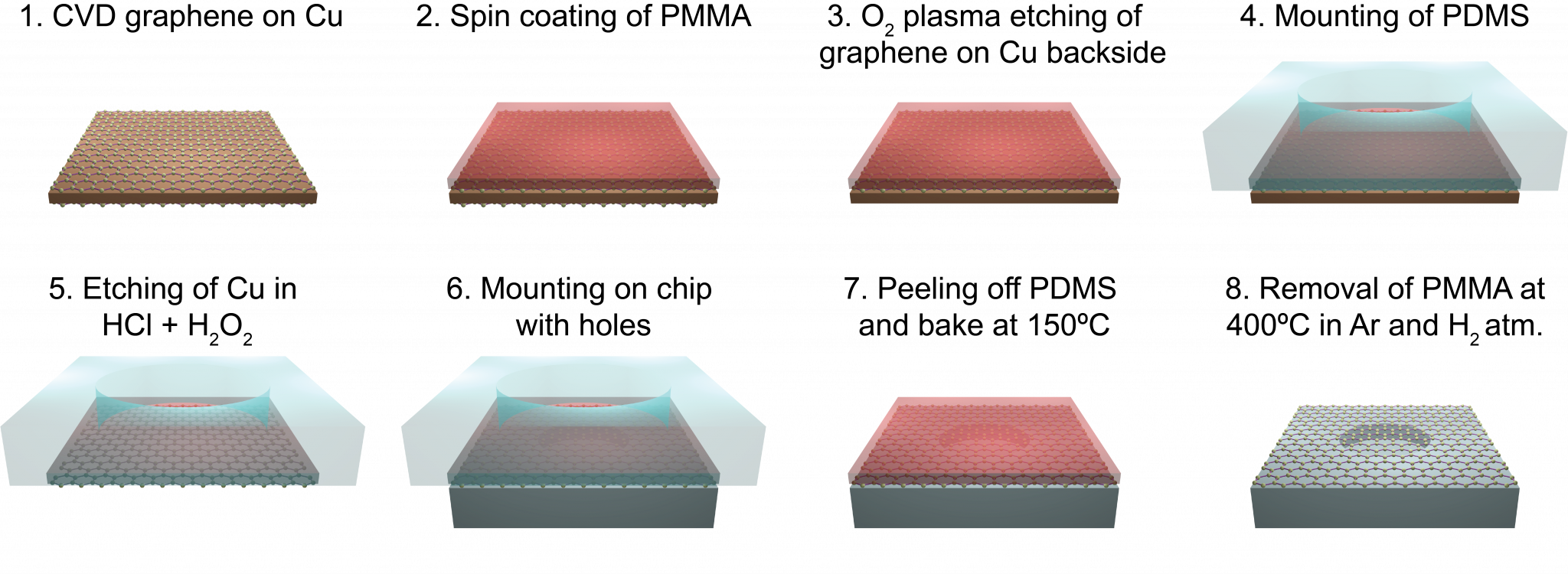
The figure below shows circular graphene membranes with diameters ranging from 1.2 μm to 26.5 μm. A comparison of an intact and broken membrane can be seen. Residues from the PMMA are typical for this kind of transfer and are also visible in all the 5 SEM pictures in the figure below. The use of low molecular weight PMMA is known to have a positive effect on this problem [4] and we are currently testing this approach.
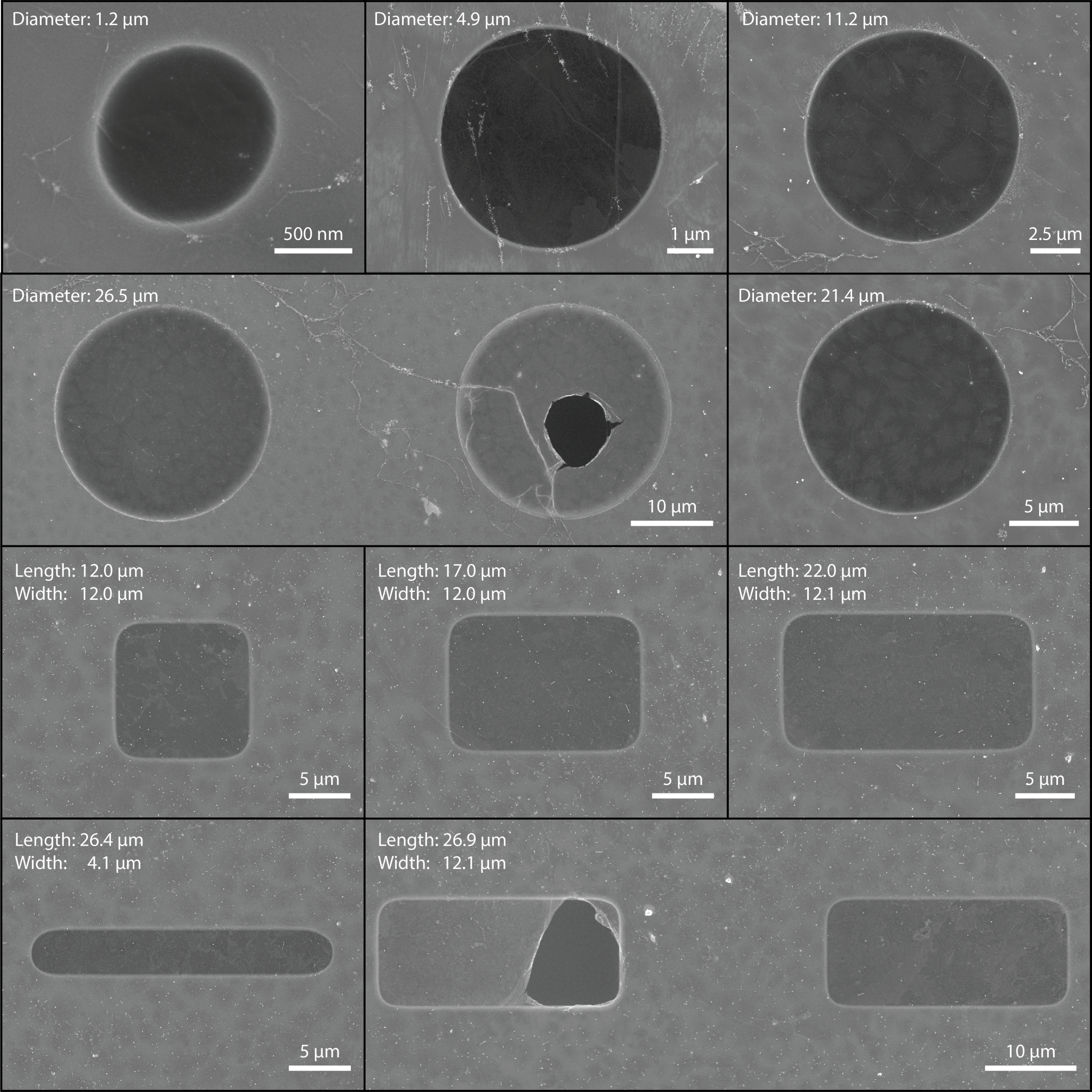
The resonant frequencies of the circular resonators as a function of the resonator radius can be seen below. From these measurements we can extract an intrinsic stress within the graphene of 1.2 GPa.
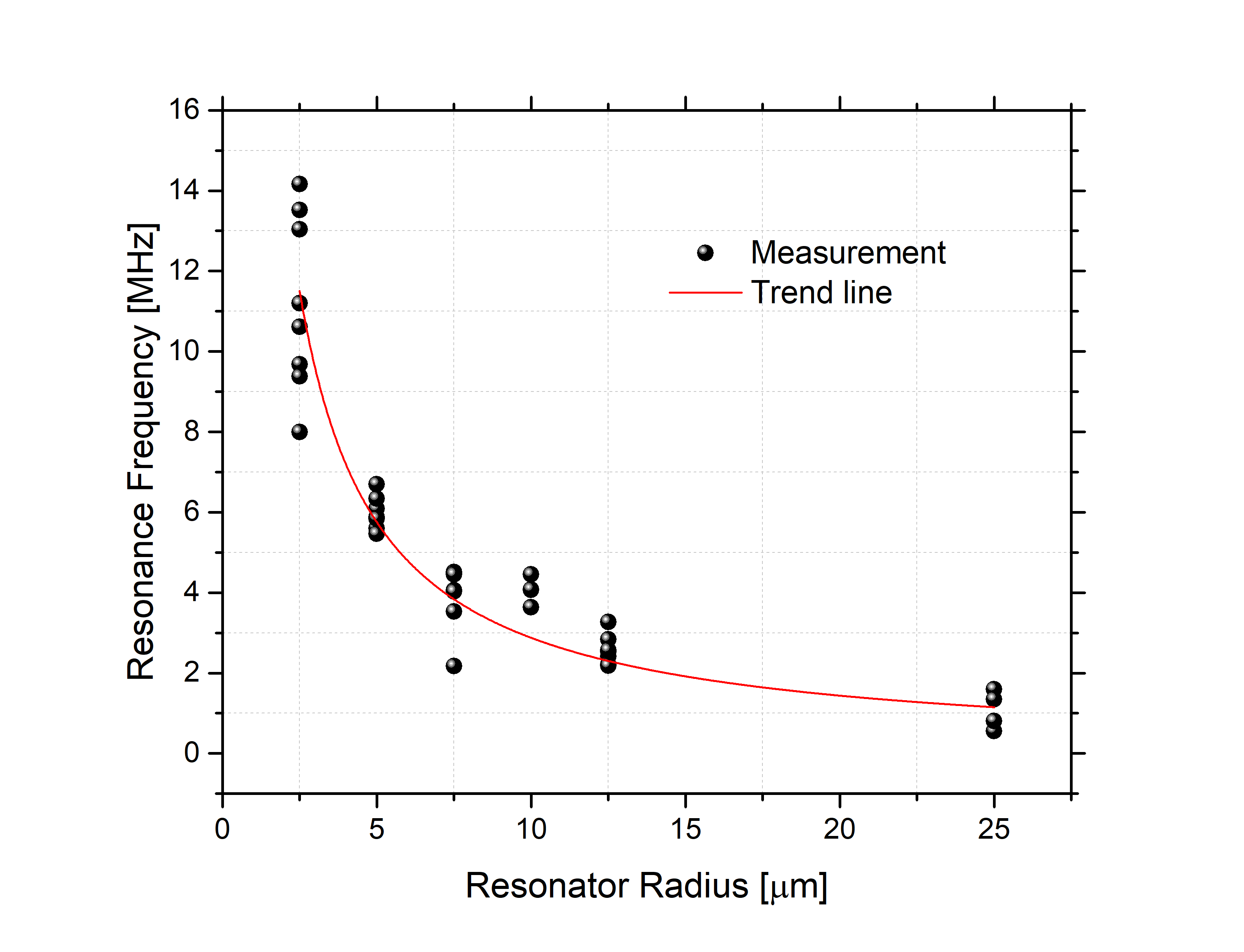
Gas detection
We have designed a gas chamber to couple with our PCB (printed circuit board) hosting the sensors. This chamber allows us to flow gas around the devices. It also allows us to perform vacuum so that we can study the behaviour of the system not only as different gases pass by, but also with the absence of gases.
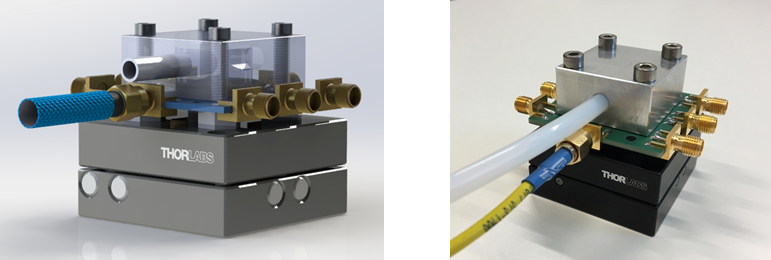
In particular, a very interesting result can be seen below when the resistance of a given device was being monitored as a function of pressure in the chamber. The response was very stable until about 10-15 microbar, where the device started changing rather abruptly. This is due to the evaporation of water molecules that were otherwise on the graphene surface. This result evidences that our devices are rather sensitive to gases.
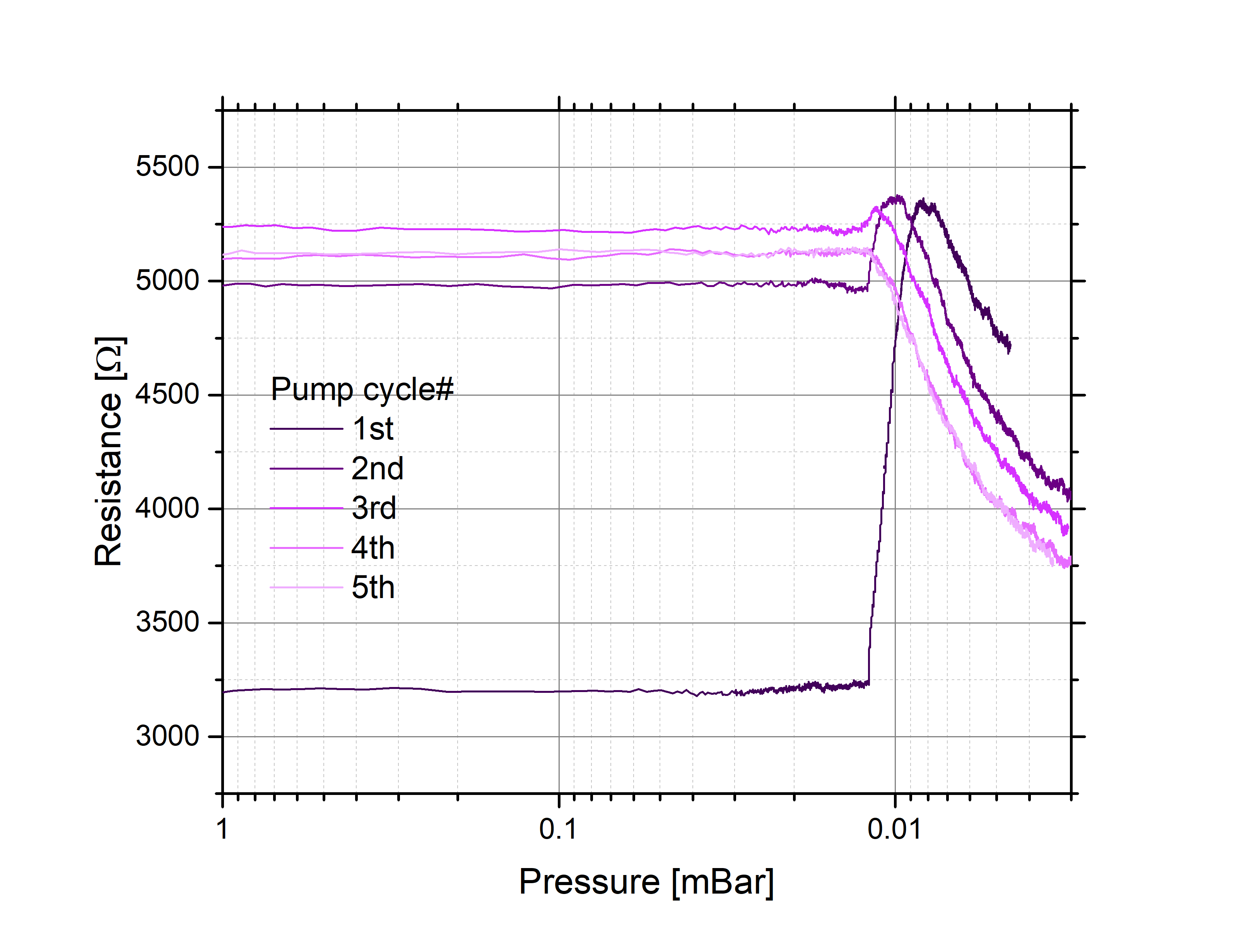