Miniaturized Bistable SMA Gripper
Innosuisse (formerly CTI) project in collaboration with a Swiss industrial partner
Project description
The current market has brought about an addiction to miniaturization, creating a need for smaller and still more performant devices. This has sponsored the perfect atmosphere for novel materials that can perform the same amount of work but with even less. The popularity of drones, surgical tools and industrial robots has created a need for a gripper that is light-weight, compact and offering high work outputs. Shape Memory Alloys, an alloy created from Nickel and Titanium, places itself in the perfect position for this application due to its remarkable work density. In this category, this novel material can outperform all other smart materials.
This collaborative research between the Swiss company, Mikron SA, and the Integrated Actuators Laboratory strives to create a novel type of Smart Gripper harnessing the exotic behavior of Shape Memory Alloys. The project aims to develop an innovative type of light-weight gripper that can deliver strong gripping forces while being completely clean-room compliant. Most traditional grippers are powered using pneumatic grippers which are incompatible with clean-rooms due to their reliance on compressed air. The Smart Gripper will be able to provide the required specifications while remaining clean-room compliant and drastically reducing the noise.
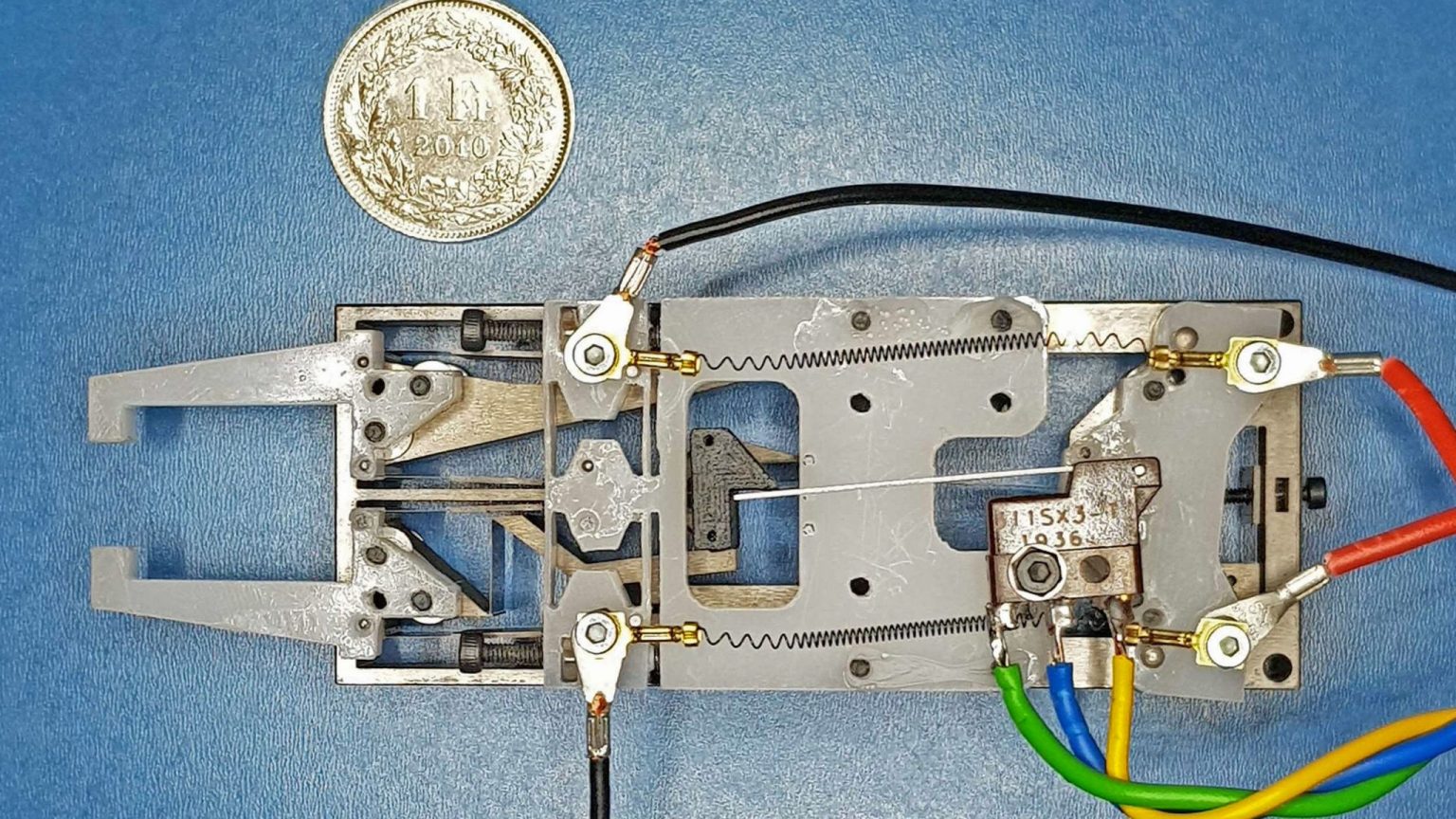
Smart Gripper made of SMA
SMAs, being biocompatible are primarily used in medical devices such as cardiac stent. But its mechanical properties and its ability to machine the metal in complex geometries, allows for elegant solutions to be designed.
Currently, the strategy has been been to combine compliant mechanisms, that can provide complex behaviors such as bistability and dynamic responses, and the Shape Memory Effect. This allows the resulting solution to provide high work output while still remaining highly dynamic. The compliant mechanisms also provides a way to create light-weight solutions for complex movements without increasing the complexity of the fabrication process.
> Functional prototype – Video #1 < |
> Functional prototype – Video #2 < |
Publications
Please note that the publication lists from Infoscience integrated into the EPFL website, lab or people pages are frozen following the launch of the new version of platform. The owners of these pages are invited to recreate their publication list from Infoscience. For any assistance, please consult the Infoscience help or contact support.