2023 – 2025
Ilse Cardenas, Véronique Michaud
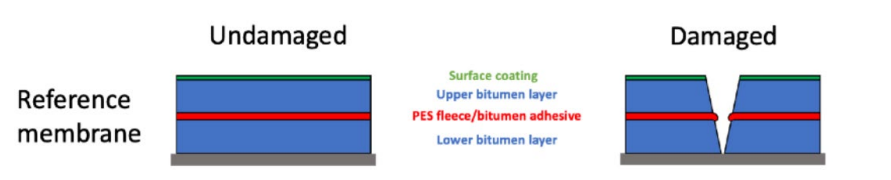
Flat-roofed buildings are generally waterproofed with polymer bitumen membranes that are installed during construction. However, these are often damaged during or after building operations. Intervention of skilled workers is therefore essential to detect and repair the resulting leaks and maintain the static properties of the buildings. This is costly and disruptive.
This project aims to develop a novel self-healing bituminous membrane for the building industry according to an original concept whereby autonomous water-induced repair of damage prevents further penetration of water and improves health and sustainability.
Funding
- Innosuisse
Fields
- Sustainable materials (biobased, renewable energy, recycling)
2022 – 2024
Valentin Rougier, Véronique Michaud
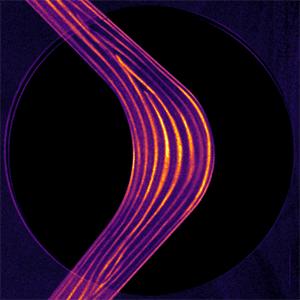
X-Ray phase-contrast imaging is one of the various X-Ray analysis methods that have emerged in recent years, which is of particular interest for composites. It has several advantages: it is non-destructive, can analyze relatively thin or light samples, reveals information about the orientation of anisotropic microstructures, and it can yield a better contrast between light materials than absorption X-Ray imaging.
Through the Dynaflow project in 2021, LPAC acquired a prototype for X-Ray phase-contrast imaging developed at CSEM with a wide field-of-view (7×7 cm²) and relatively rapid acquisition time (~10 s), enabling in-operando imaging. This project aims at assessing the usefulness of this machine for various samples and applications, thus enabling its use in synergy with the existing PIXE platform for X-Ray imaging. Other developments include data treatment routines, in-operando imaging trials and fabrication of testing rigs.
Funding
- EPFL Platform Technical Advancement Seed Fund
Partners
- EPFL PIXE
Resources
- Varanges, Y. Lebaupin, R. Amacher, V. Rougier, V. Schnyder, J. Aubry, T. Richard, V. Michaud, “Enhancing the mechanical performance of composite corners through microstructural optimization and geometrical design”, 2024 (under review).
- Garrabos, “Mechanical and Optical Characterization of Healable Composites,” Semester project, EPFL, 2023
- Teixidó, G. Broggi, B. Caglar, V. Michaud, Measurement and modelling of dynamic fluid saturation in carbon reinforcements, Composites: Part A 169 (2023)
- Teixidó Pedarros, “Visualization and modelling of dynamic flow in fibrous preforms for liquid composite molding,” PhD thesis, EPFL, 2023.
- Teixidó, B. Caglar, V. Revol, and V. Michaud, “In-operando dynamic visualization of flow through porous preforms based on X-ray phase contrast imaging,” Composites Part A: Applied Science and Manufacturing, vol. 149, p. 106560, 2021.
Fields
- Biomedical and electronic devices (encapsulation materials, flexible electronics)
- Health and comfort (biocompatible composites, prostheses)
- Energy generation and storage (integration of solar panels)
Vincent Varanges, Pierre-Etienne Bourban, Dominique Pioletti
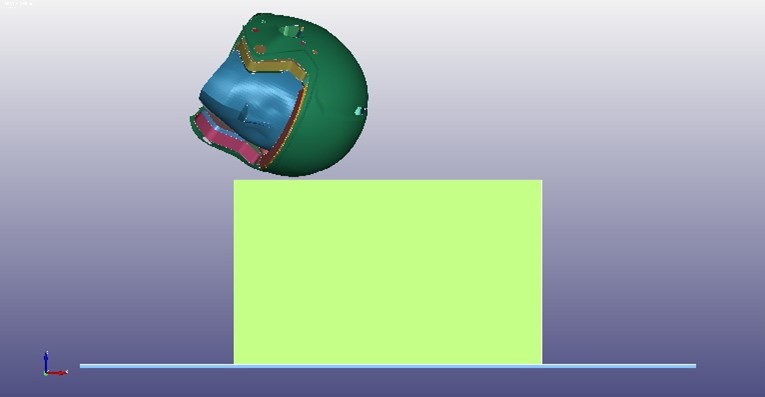
During the 1990s, ski accidents involving head injuries mostly led to skull fractures. The introduction of helmets among skiers shifted the pattern towards traumatic brain injuries (TBI). TBIs can result in severe concussion, vegetative states, or death. Modern ski helmets, developed in the late 1980s, consist of an external shell for impact distribution and an internal liner for energy absorption. However, these helmets are designed for impacts at speeds lower than those typically experienced in ski accidents, leading to critical brain shearing.
The project proposes to use numerical brain injury prediction tools to develop new liners with high dissipative properties to decrease TBI risk. These liners will be evaluated against existing helmets in real ski accident conditions.
Partners
- Laboratory of Biomechanical Orthopedics (EPFL)
- Valais Hospital
Publications
- Varanges V., Eghbali P., Nasrollahzadeh N., Fournier J-Y., Bourban P-E., Pioletti D. AI-Driven Optimization of Helmet Material Design: Mitigating Traumatic Axonal Injuries through Innovative Constitutive Law Enhancement, https://doi.org/10.21203/rs.3.rs-3791451/v1
Thematics
- Biomechanics of the head and the brain
- Dissipative materials
- Bioinspired metamaterials
Fields
- High-speed Sports (Ski, mountaineering, cycling)
- Health
2019 – 2024
Alexandre Looten, Raphaël Charvet, Véronique Michaud
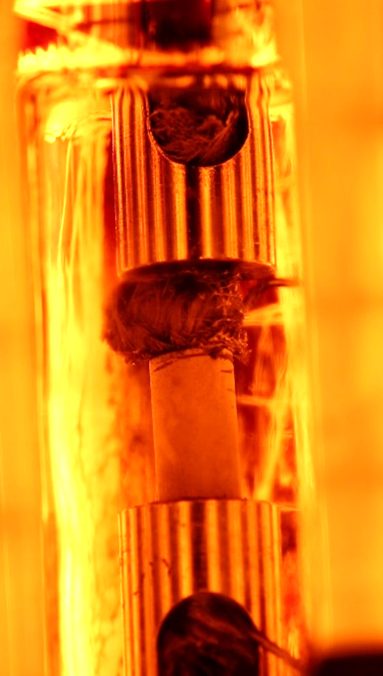
With the current rate of space launches, space debris surviving re-entry are an increasing threat in the air and on the ground. To fight such concern, our projec,t following the Design-for-Demise approach, aims to replace the current critical spacecraft materials such as carbon–epoxy composites, which tend to survive the heat and atmosphere experience during re-entry, with novel demisable composite systems. The goal is to provide systems, i.e. a combination of adequate materials for the panels, as well as fasteners, to provide an early break-up of the structure, then degradation of the panels and the inside of the object, such as reservoirs. Such substitution steps require complex and extensive material testing and evaluation to prove their demise improvement while maintaining equivalent mission-relevant properties. As a result, promising flax-carbon fibers hybrid reinforcement and reactive metallic matrix filler, in addition to optimized short carbon fiber/PEEK bolt fasteners have been identified. This multi-collaborative project supported by ESA aims to take a step forward towards a safe and sustainable space environment.
Funding
-
European Space Agency ESA – Network Partnering Initiative (NPI)
Project partners
- ESA – Clean Space Office
- Beyond Gravity
- ClearSpace SA
- IRS – Stuttgart Universität
- icotec ag
- Bcomp Ltd.
- Belstead Research Ltd.
Website
- ESA Clean Space www.esa.int/Space_Safety/Clean_Space
Fields
-
Mobility (high specific properties, space technologies)
-
Sustainable materials (demisability, safe space, sustainable space)
2021 – 2024
Valentin Rougier, Jean-Baptiste Desbrest, Evelin Boros, Véronique Michaud
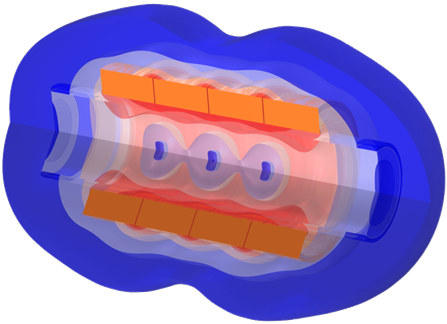
This project is a collaboration between two EPFL laboratories, namely LPAC and LQM, working with the startup company KOMP-ACT SA. The main objective is to develop a new design of magnetic linear actuators, using multiple pathways to improve its performance and cost efficiency compared to what is currently available on the market. This is achieved through the formulation of efficient magnetic composites developed at LPAC, which are fine-tuned using clever magnetic patterns thanks to LQM’s expertise. This research also explores modifications on the overall design of the motor, which encompasses optimizing the geometry of parts, changing coil winding techniques and simplifying the overall assembly. Beyond cost benefits, other perspectives include reducing electrical losses, improving energy efficiency by reducing part weight, and limiting the consumption of rare-earth elements.
Funding
- Innosuisse (Swiss Innovation Agency)
Project partners
- EPFL LQM (Laboratory for Quantum Magnetism)
- KOMP-ACT SA (https://komp-act.com/)
Fields
- Biomedical and electronic devices (encapsulation materials, flexible electronics and devices)
2020 – 2024
Jialiang Fan, Veronique Michaud, Anastasios Vassilopoulos (CCLab)
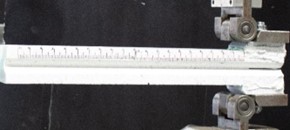
This project is a collaborative project between EPFL (LPAC and CC Lab) and two universities in Belgium (UGhent and VUB). This project proposes a new combined numerical and experimental approach for the materials development, testing and analysis of thick adhesive joints for large scale civil engineering structures, with the case study of wind turbine blades. To achieve these objectives, (i) numerical modelling is used to analyze the local loading conditions of the adhesive under the global loading conditions of the blade, so as to establish a detailed sub-model of this critical part; (ii) experimental characterization of model thick adhesive layers are carried out in static and fatigue complex loading conditions so as to mimic realistic loading cases; (iii) a commercial state of the art adhesive was characterized as a basis for further material development and inclusion of second phases to improve damage tolerance of the adhesive in these specific conditions and provide “healing mechanisms” to prevent crack propagation. At LPAC, we adapted a grooved geometry to test thick adhesive joints in double cantilever beam testing, to achieve cohesive failure under both quasi-static and fatigue loadings. New formulation adhesives with self-healing capabilities are developed to prolong the lifetime of the thick adhesive joints. The new formulation adhesives also fulfill the requirements proposed from manufacturing process, design, and usage phases, such as sufficient rheological yield stress, adequate mechanical properties.
Funding
-
Swiss National Science Foundation (SNF)
-
Research Foundation – Flanders (FWO Vlaanderen)
Project partners
- Composite Construction Laboratory (CCLAB-EPFL)
- Universiteit Gent (BE)
- Vrije Universiteit Brussel (BE)
- Sika Technology AG (CH)
Publications
- Fan, A.P. Vassilopoulos, V. Michaud, Mode I fracture of thick adhesively bonded GFRP composite joints for wind turbine rotor blades, Composite Structures 327 (2024) 117705. https://doi.org/10.1016/j.compstruct.2023.117705.
Fields
- Sustainable materials (biobased, renewable energy, recycling)
Selected past projects
Rajasundar Chandran, Gregory Huot, Véronique Michaud
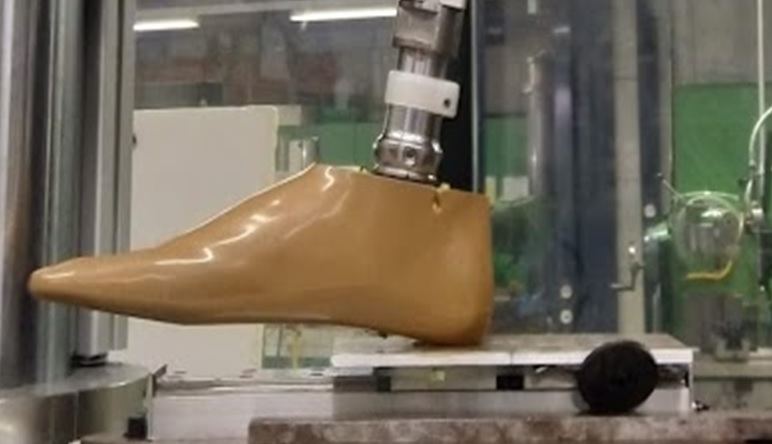
The goal of the Agilis collaboration is to develop a prosthetic foot designed for use by amputees with high mobility needs, in the hopes of improving their capacity for socio-economic integration. Much of the technology currently available in developed countries is often out of reach in South countries due to cost. Moreover, these technologies are generally not adapted for use in these countries (durability, aesthetic aspect, etc.). The project aims to meet this growing worldwide need through a combination of composite materials and foams, which fulfills the aesthetic, biomechanical and materials requirements. As the prosthesis is designed for humanitarian needs, limiting manufacturing costs is key for promoting the widest possible access to the new product; as a result, minimizing the use of costly carbon-epoxy laminates while preserving the energy restitution is one of this project’s challenges. LPAC’s contribution to this collaborative project is to develop a “cost modeling” approach to identify and test potential materials and processes that fit the technical and economical target. The resulting prototypes led to innovative materials combinations, which nonetheless passed the requirements in fatigue life and mechanical resistance.
Funding
- Innosuisse
Partners
- CODEV’s EssentialTech program
- EPFL-LMAM
- EPFL-LMAF
- International Committee of the Red Cross (ICRC)
- CR Equipements SA
Website and resources
Amaël Cohades; Robin Trigueira; Cecilia Scazzoli ; Véronique Michaud
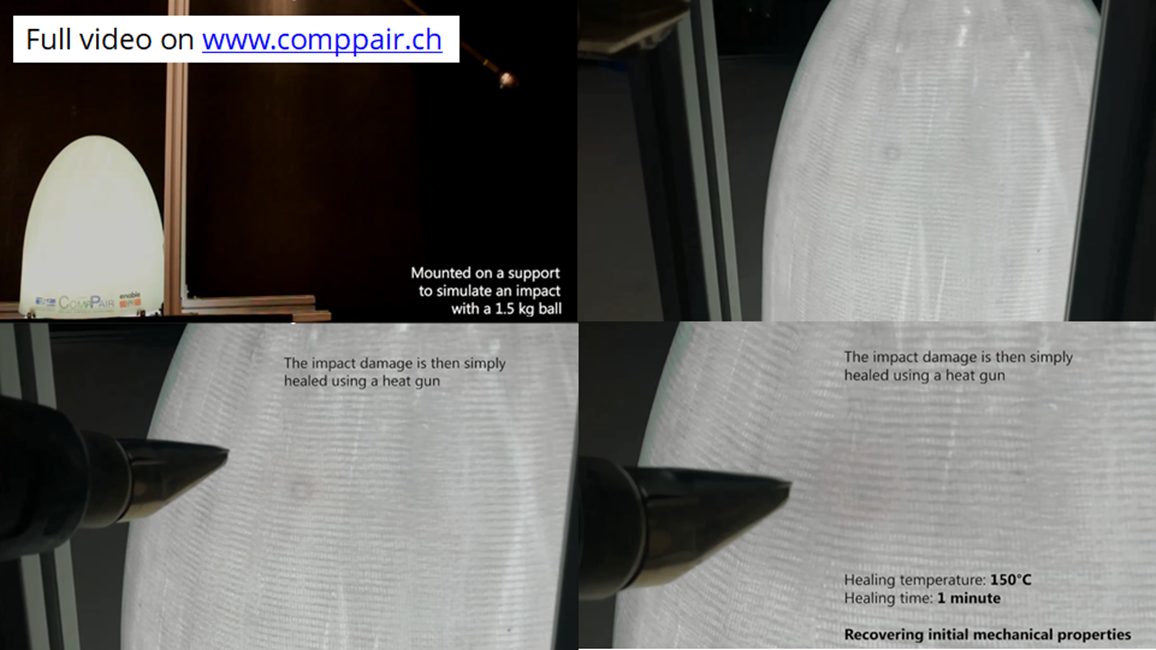
CompPair is the result of many years of research at LPAC in the field of self-healing structural composites. We are now able to deliver an efficient, smart and bio-inspired solution for extending the life-time of composite structures. With the incubating company CompPair, we are currently developing smart prepregs (preimpregnated textiles) integrating our healable matrix that are compatible with existing composite manufacturing processes. These new materials enable repeated damage healing, usage as resistant and lightweight materials, and easier recycling at the end-of-life. These new materials aim to reduce maintenance costs, increase products lifetime and improve global sustainability while keeping the needed industrial specifications.
Funding
- EPFL Enable Program
- EPFL Innogrants
- Gebert Rüf Stifftung InnoBooster program
Partners
- FHNW (The University of Applied Sciences and Arts Northwestern Switzerland)
- KATZ (Plastic Training and Technology Centre)
- Tissa Glasweberei
- Decision SA
Webpage
Publications
- N. Hostettler, A. Cohades, V. Michaud. Healable composites and their performance through mechanical and durability testing. JEC Magazine. May 2019
Arif Poothanari, Yves Leterrier, Véronique Michaud
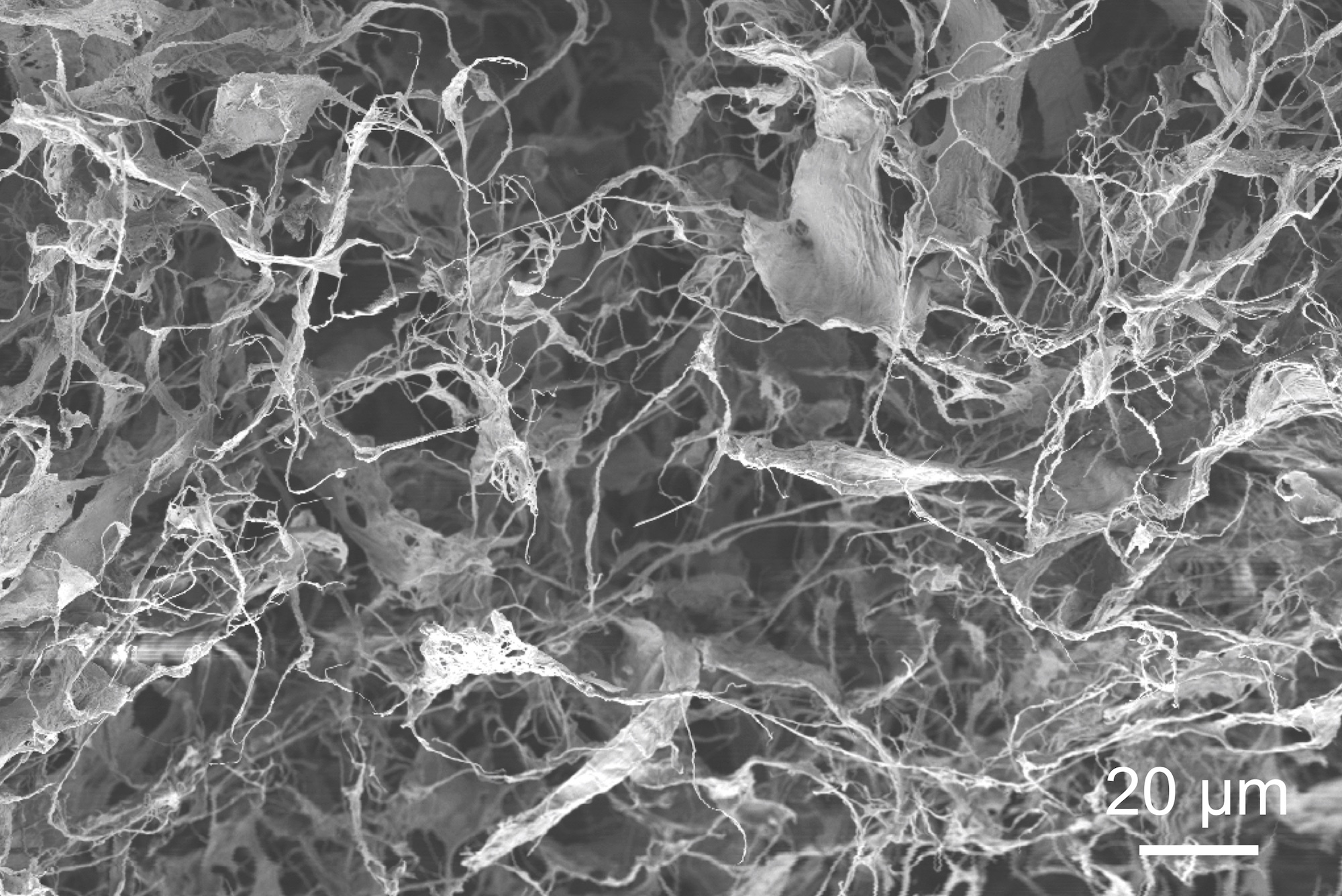
Hybrid piezoelectric nanocomposites based on surface modified graphene/microfibrillated cellulose (MFC) and poly(vinylidene fluoride) (PVDF) are developed for energy harvesting applications. The role of the fillers is first to promote the crystallization of PVDF into its polar beta-phase, and second to achieve exceptional thermomechanical stability. Fluorinated and amine-induced H-bonded interfaces are produced for both graphene and MFC and their influence on the crystalline state, mechanical and electrical properties of composites is systematically explored within a broad compositional space. Pristine and fluorinated fillers hinder beta-phase, in contrast to aminated fillers, which lead to the best property combination.
Funding
- Swiss Government Excellence Scholarships
Partners
- Prof. Damjanovic, EPFL
2018 – 2022
Guillaume Broggi, Alexios Argyropoulos, Joël Cugnoni, Véronique Michaud

The HyfiSyn project gathers 8 universities, 5 industrial partners and 2 professional training organizations and aims to train early stage researchers in the field of hybrid composites, in particular to explore various materials combinations to alleviate some of their main limitations, as for example their intrinsically limited toughness.One key challenge of this project, that is under investigation at EPFL, is to evaluate the effects brought by fiber hybridization in thin ply composites, which due to the limited size of each fiber layer (typically below 100µm) are generally more efficient in terms of in-plane mechanical properties, but loose in toughness. We plan to correlate mechanical performance to the hybrid microstructure configuration, through experiments and modelling, and to help design adapted manufacturing routes to produce and consolidate these hybrid composites.
Funding
- Marie Sklodowska-Curie programme (EU Horizon 2020), Duration mid 2018-mid 2022
Partners
- North Thin Ply Technology (CH)
- BMW Group (D)
- ELG carbon Fibers (UK)
- SIOEN Industries (B)
- University of Bristol (GB)
- KU Leuven (BE)
- Budapest University of Technology and Economics (HU)
- University of Nottingham (UK)
- Imperial College London (UK)
- Technical University of Denmark (DK)
- University of Vienna (A)
- 4 Real Sim
- Fiberline Composites
Website
Resources
Adrien Demongeot, Véronique Michaud

With the continuous growth of railway traffic and population in Switzerland, railway noise has become a severe environmental problem. At typical railway speeds, the most relevant source of noise is “rolling noise” emitted from the wheel and from the rail. One approach to reducing rolling noise without the cost-intensive addition of novel components to the railway track is to improve the rail pad, which forms part of the rail fastening system and typically consists of a simple rubber cushion inserted between the rails and sleepers. The aim of this project is to develop a novel rail pad system that is optimized with respect to both railway noise reduction and protection of the railway superstructure against transient loads and vibrations. The role of LPAC is centered on the determination of the optimal material microstructure to reach the desired damping properties.
Funding
- Federal Office for the Environment (4 years)
Partners
- EPFL LMOM
- EPFL LMAF
- EPFL LTS2
- EPFL TRACE
- EMPA
- HEIG-VD
- SBB-CFF-FFS