2024 – 2028
Martyn Wakeman, Jean-Baptiste Desbrest, Véronique Michaud
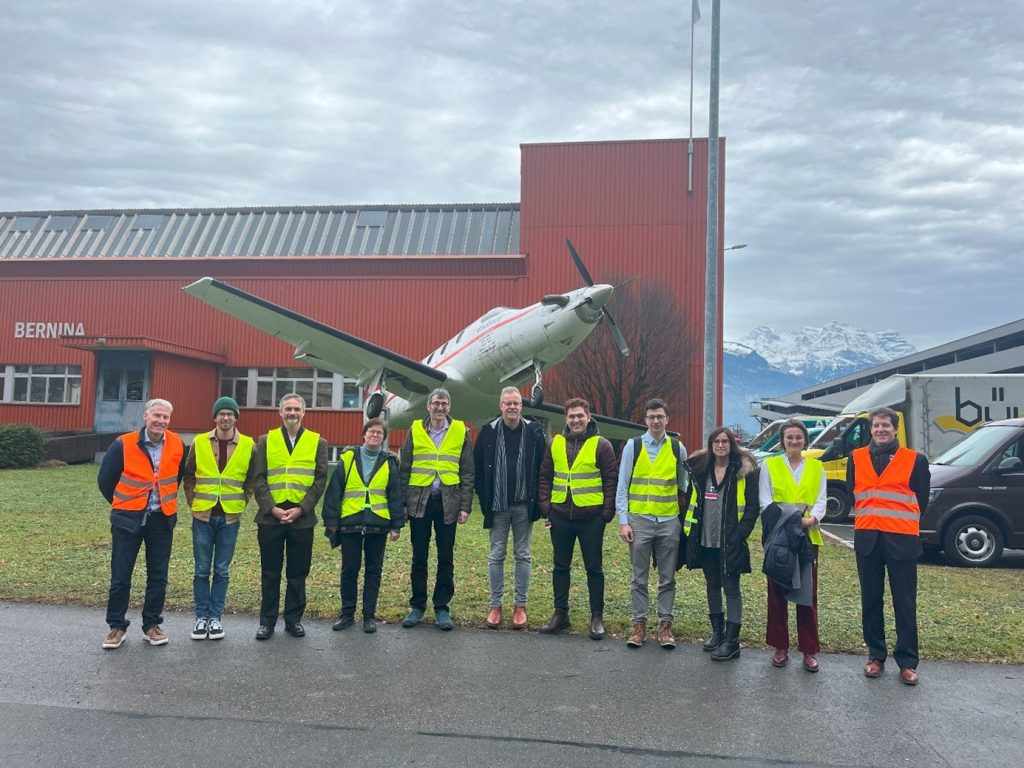
This Innosuisse FLAGSHIP project aims at reducing the environmental impact of plastics in the industry in the context of the NetZero 2050 objectives. LPAC is involved in a subproject that will examine and develop best carbon footprint materials, using innovative approaches to materials, processes, and recycling to minimize the impact of composite materials in various industries.
The focus will also be on the eco-design of parts, anticipating end-of-life scenarios to shift from a linear to a re-wired circular economy model. Additionally, the project will seek to reorganize how materials are sourced and distributed to create a more sustainable industry, involving collaboration with multiple industrial partners.
Funding
- Innosuisse – Flagship project
Partners
- Huntsman Advanced Materials
- Pilatus Aircraft Ltd.
- OST – Eastern Switzerland University of Applied Sciences
- Composite Recycling SA
- Composites Busch SA
Fields
- Mobility (light weighting and cost effectiveness in automotive, rail, aeronautics and space)
- Sustainable materials (best carbon foot print materials, bio-based, renewable energy, recycling)
- NetZero transition strategy modelling (LCA, MFA, finance), circular economy
2022 – 2024
Valentin Rougier, Véronique Michaud
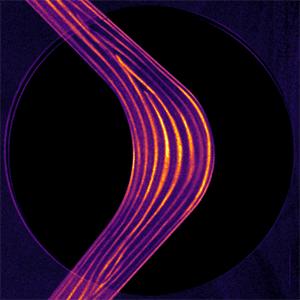
X-Ray phase-contrast imaging is one of the various X-Ray analysis methods that have emerged in recent years, which is of particular interest for composites. It has several advantages: it is non-destructive, can analyze relatively thin or light samples, reveals information about the orientation of anisotropic microstructures, and it can yield a better contrast between light materials than absorption X-Ray imaging.
Through the Dynaflow project in 2021, LPAC acquired a prototype for X-Ray phase-contrast imaging developed at CSEM with a wide field-of-view (7×7 cm²) and relatively rapid acquisition time (~10 s), enabling in-operando imaging. This project aims at assessing the usefulness of this machine for various samples and applications, thus enabling its use in synergy with the existing PIXE platform for X-Ray imaging. Other developments include data treatment routines, in-operando imaging trials and fabrication of testing rigs.
Funding
- EPFL Platform Technical Advancement Seed Fund
Partners
- EPFL PIXE
Resources
- Varanges, Y. Lebaupin, R. Amacher, V. Rougier, V. Schnyder, J. Aubry, T. Richard, V. Michaud, “Enhancing the mechanical performance of composite corners through microstructural optimization and geometrical design”, 2024 (under review).
- Garrabos, “Mechanical and Optical Characterization of Healable Composites,” Semester project, EPFL, 2023
- Teixidó, G. Broggi, B. Caglar, V. Michaud, Measurement and modelling of dynamic fluid saturation in carbon reinforcements, Composites: Part A 169 (2023)
- Teixidó Pedarros, “Visualization and modelling of dynamic flow in fibrous preforms for liquid composite molding,” PhD thesis, EPFL, 2023.
- Teixidó, B. Caglar, V. Revol, and V. Michaud, “In-operando dynamic visualization of flow through porous preforms based on X-ray phase contrast imaging,” Composites Part A: Applied Science and Manufacturing, vol. 149, p. 106560, 2021.
Fields
- Biomedical and electronic devices (encapsulation materials, flexible electronics)
- Health and comfort (biocompatible composites, prostheses)
- Energy generation and storage (integration of solar panels)
Alper Balkan, Yves Leterrier
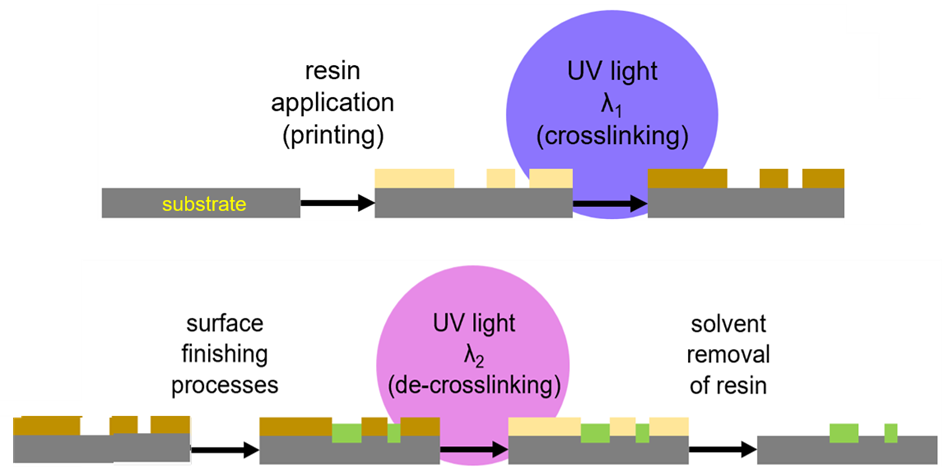
Thematics
- Fundamentals of polymers and composite materials processing (multiphase fluid flow, capillary effects, process kinetics, UV and thermal curing)
- Surfaces and interfaces (bioinspired surfaces, multilayers, adhesion and bonding)
- Integration of functions (smart and piezoelectric composites, self-healing ability, damping, non-linearity, biocompatibility).
Fields
- Sustainable materials (biobased, renewable energy, recycling
DiPrintProtect aims to develop and process photo-curable composite resins and form robust but temporary coatings on metal substrates that can withstand severe finishing operations and be removed easily. These advanced coatings are to be realized by state-of-the-art digital printing methods for replacing certain manufacturing steps and achieving a more capable and automated watch production procedure. Major challenges are the dispersion of reinforcing particles within the photo-curable resin while maintaining reasonable resin processability as well as optical transparency, the light-assisted de-crosslinking of the composite coating material in a practical time frame using commercially available solvents or other dissolution/delamination methods, the quantitative monitoring of the de-crosslinking process, and the optimization of this coating removal method until “traceless removal” is achieved.
Funding
- Strategic Focus Area – Advanced Manufacturing of the Swiss ETH Board
Project Partners
- Laboratory for Thin Films and Photovoltaics (EMPA)
- Laboratory for Functional Polymers (EMPA)
- Macromolecular Engineering Laboratory (ETHZ)
Industry Partners
- Association Suisse pour la Recherche Horlogère
- The Swatch Group Research and Development Ltd
- Optomec GmbH
- Ciposa S.A.
Webpage
Vincent Varanges, Pierre-Etienne Bourban, Dominique Pioletti
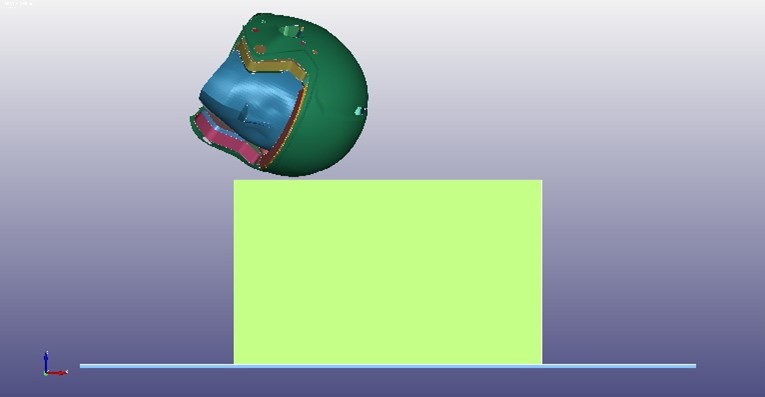
During the 1990s, ski accidents involving head injuries mostly led to skull fractures. The introduction of helmets among skiers shifted the pattern towards traumatic brain injuries (TBI). TBIs can result in severe concussion, vegetative states, or death. Modern ski helmets, developed in the late 1980s, consist of an external shell for impact distribution and an internal liner for energy absorption. However, these helmets are designed for impacts at speeds lower than those typically experienced in ski accidents, leading to critical brain shearing.
The project proposes to use numerical brain injury prediction tools to develop new liners with high dissipative properties to decrease TBI risk. These liners will be evaluated against existing helmets in real ski accident conditions.
Partners
- Laboratory of Biomechanical Orthopedics (EPFL)
- Valais Hospital
Publications
- Varanges V., Eghbali P., Nasrollahzadeh N., Fournier J-Y., Bourban P-E., Pioletti D. AI-Driven Optimization of Helmet Material Design: Mitigating Traumatic Axonal Injuries through Innovative Constitutive Law Enhancement, https://doi.org/10.21203/rs.3.rs-3791451/v1
Thematics
- Biomechanics of the head and the brain
- Dissipative materials
- Bioinspired metamaterials
Fields
- High-speed Sports (Ski, mountaineering, cycling)
- Health
2022 – 2026
Maurane Gaelle Fokam Fokam, Christian Fokam Bopda, Anatole Chengoue Mbouyap, Bienvenu Kenmeugne (Université de Yaoundé), Valentin Rougier, Véronique Michaud
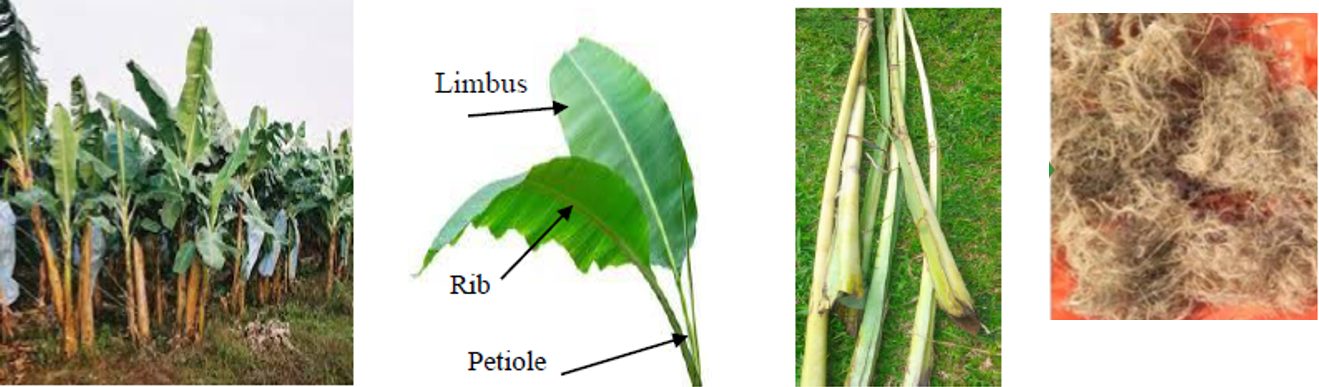
This study, carried out with ENSPY in Cameroon, focuses on the exploitation of agricultural waste and untapped local resources, more specifically the fibers from the main vein of the banana leaf and bio-based resins to produce composite materials. We prioritize organic resins extracted from plant bark (tannin), with the aim of producing a 100% natural and biodegradable material. The work consists in carrying out, first, the extraction and the overall characterization of the constituents which are the fibers and the resin. The properties of the extracted fibers are promising, with tensile modulus around 16 GPa and strength from 350 to 450 MPa, depending on the treatment procedures, which should allow to produce composites from these waste products.
Funding
- EXAF 100 PhDs for Africa Program
Partners
- Ecole Nationale Supérieure Polytechnique de Yaoundé (Cameroon)
2020 – 2024
Jialiang Fan, Veronique Michaud, Anastasios Vassilopoulos (CCLab)
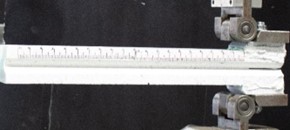
This project is a collaborative project between EPFL (LPAC and CC Lab) and two universities in Belgium (UGhent and VUB). This project proposes a new combined numerical and experimental approach for the materials development, testing and analysis of thick adhesive joints for large scale civil engineering structures, with the case study of wind turbine blades. To achieve these objectives, (i) numerical modelling is used to analyze the local loading conditions of the adhesive under the global loading conditions of the blade, so as to establish a detailed sub-model of this critical part; (ii) experimental characterization of model thick adhesive layers are carried out in static and fatigue complex loading conditions so as to mimic realistic loading cases; (iii) a commercial state of the art adhesive was characterized as a basis for further material development and inclusion of second phases to improve damage tolerance of the adhesive in these specific conditions and provide “healing mechanisms” to prevent crack propagation. At LPAC, we adapted a grooved geometry to test thick adhesive joints in double cantilever beam testing, to achieve cohesive failure under both quasi-static and fatigue loadings. New formulation adhesives with self-healing capabilities are developed to prolong the lifetime of the thick adhesive joints. The new formulation adhesives also fulfill the requirements proposed from manufacturing process, design, and usage phases, such as sufficient rheological yield stress, adequate mechanical properties.
Funding
-
Swiss National Science Foundation (SNF)
-
Research Foundation – Flanders (FWO Vlaanderen)
Project partners
- Composite Construction Laboratory (CCLAB-EPFL)
- Universiteit Gent (BE)
- Vrije Universiteit Brussel (BE)
- Sika Technology AG (CH)
Publications
- Fan, A.P. Vassilopoulos, V. Michaud, Mode I fracture of thick adhesively bonded GFRP composite joints for wind turbine rotor blades, Composite Structures 327 (2024) 117705. https://doi.org/10.1016/j.compstruct.2023.117705.
Fields
- Sustainable materials (biobased, renewable energy, recycling)
2021 – 2024
Valentin Rougier, Jean-Baptiste Desbrest, Evelin Boros, Véronique Michaud
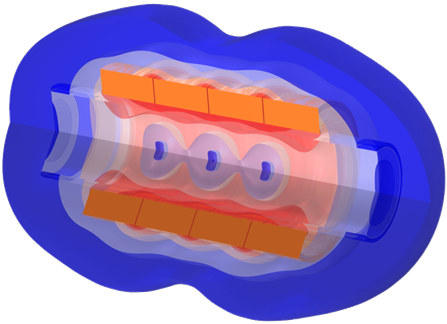
This project is a collaboration between two EPFL laboratories, namely LPAC and LQM, working with the startup company KOMP-ACT SA. The main objective is to develop a new design of magnetic linear actuators, using multiple pathways to improve its performance and cost efficiency compared to what is currently available on the market. This is achieved through the formulation of efficient magnetic composites developed at LPAC, which are fine-tuned using clever magnetic patterns thanks to LQM’s expertise. This research also explores modifications on the overall design of the motor, which encompasses optimizing the geometry of parts, changing coil winding techniques and simplifying the overall assembly. Beyond cost benefits, other perspectives include reducing electrical losses, improving energy efficiency by reducing part weight, and limiting the consumption of rare-earth elements.
Funding
- Innosuisse (Swiss Innovation Agency)
Project partners
- EPFL LQM (Laboratory for Quantum Magnetism)
- KOMP-ACT SA (https://komp-act.com/)
Fields
- Biomedical and electronic devices (encapsulation materials, flexible electronics and devices)
2023 – 2024
Jeroen Staal, Véronique Michaud
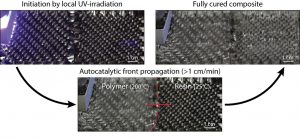
Conventional composite manufacturing methods are often slow and highly energy-intensive. Frontal polymerisation has been proposed as a promising alternative to bring significant reductions in the processing time, from hours to minutes, and energy demand, but its use is complicated by the inability to sustain the process in the presence of high fibre contents. LPAC is actively developing novel strategies that can overcome these limitations and to bring the promise of frontal polymerisation to the composites industry. This has materialised in the development of self-catalysed frontal polymerisation: the first method that successfully cure high fibre content (>55%) composites without requiring a continuous energy input, reducing the energy demand by >99.5%. The current project focusses at the optimisation and scaling-up of this method while simultaneously evaluating its cost and environmental impact.
Funding source
- Air Force Office of Scientific Research (award number FA8655-23-1-7035).
Publications
- Staal, Jeroen; Smit, Edgar; Caglar, Baris; Michaud, Véronique. Thermal management in radical induced cationic frontal polymerisation for optimised processing of fibre reinforced polymers. In Composite Science and Technology, 237(May), 110009. https://doi.org/10.1016/j.compscitech.2023.110009
Fields
- Mobility (light weighting and cost effectiveness in automotive, rail, aeronautics and space)
2019 – 2024
Alexandre Looten, Raphaël Charvet, Véronique Michaud
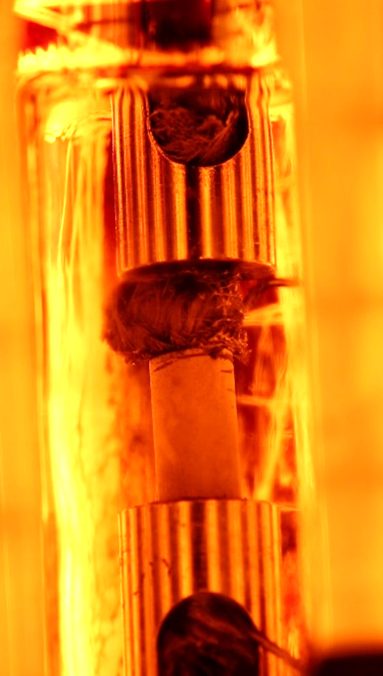
With the current rate of space launches, space debris surviving re-entry are an increasing threat in the air and on the ground. To fight such concern, our projec,t following the Design-for-Demise approach, aims to replace the current critical spacecraft materials such as carbon–epoxy composites, which tend to survive the heat and atmosphere experience during re-entry, with novel demisable composite systems. The goal is to provide systems, i.e. a combination of adequate materials for the panels, as well as fasteners, to provide an early break-up of the structure, then degradation of the panels and the inside of the object, such as reservoirs. Such substitution steps require complex and extensive material testing and evaluation to prove their demise improvement while maintaining equivalent mission-relevant properties. As a result, promising flax-carbon fibers hybrid reinforcement and reactive metallic matrix filler, in addition to optimized short carbon fiber/PEEK bolt fasteners have been identified. This multi-collaborative project supported by ESA aims to take a step forward towards a safe and sustainable space environment.
Funding
-
European Space Agency ESA – Network Partnering Initiative (NPI)
Project partners
- ESA – Clean Space Office
- Beyond Gravity
- ClearSpace SA
- IRS – Stuttgart Universität
- icotec ag
- Bcomp Ltd.
- Belstead Research Ltd.
Website
- ESA Clean Space www.esa.int/Space_Safety/Clean_Space
Fields
-
Mobility (high specific properties, space technologies)
-
Sustainable materials (demisability, safe space, sustainable space)
Selected past projects
2022 – 2023
Nour Halawani, Véronique Michaud

Glass Fiber Reinforced Plastic (GFRP) is an incredibly versatile material, commonly found in boats, planes, trains, and wind turbine blades. The majority of GFRP waste ends up in landfills, while the rest is either being incinerated or worse, abandoned in the environment. Decades of attempts to recycle GFRP have been unsuccessful, as the economic incentives were not sufficient and the materials not prone to easy recycling. In this project, we have used standard pyrolysis technology which heats up the GFRP in a static oxygen free environment. This removes the plastic from the fibers leaving the fibers slightly damaged during this process, and in a difficult-to-handle form. A lab-scale protocol was thus developed to produce and test a Fiberglass mat from reclaimed fibers. This includes the development of a dispersion method, surface treatment, sizing application, and adhesion promotor, as well as preliminary protocol for mat production, up to composite testing and environmental impact analysis, to identify the main hurdles towards successful implementation.
Funding
- Gebert Rüf Stiftung Innobooster GRS-025/22
Fields
- Sustainable materials (recycling)
Emylou Jacquier, Marina Martinez Fernandez, Adrien Demongeot, Amaël Cohades, Yves Leterrier, Veronique Michaud
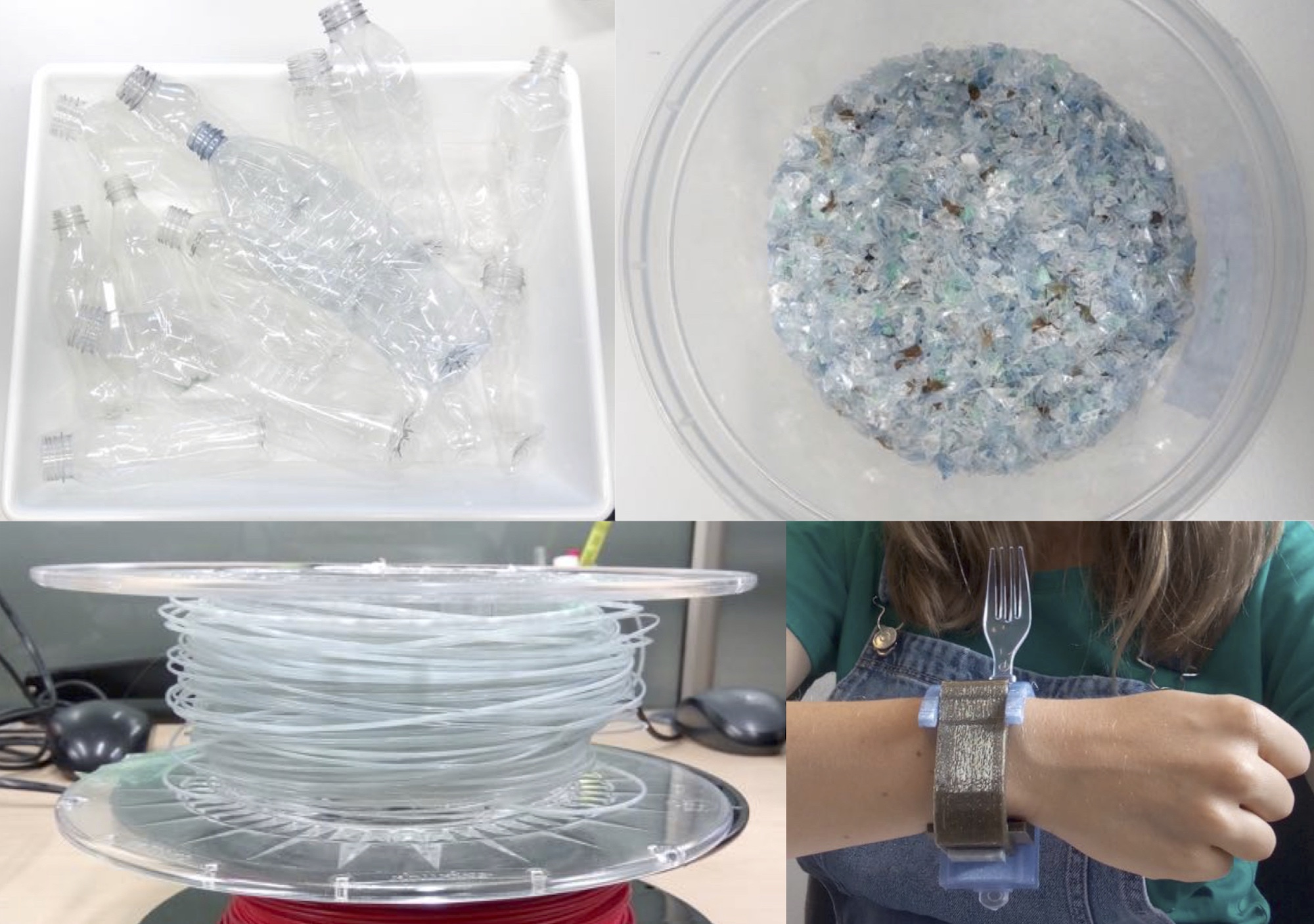
3D4PEACE is part of a strategic engagement between Omnis Institute, UNIANDES, EPFL-LPAC and a social leader in Colombia active in the Human Inclusion sector. It aims to promote social, technical and scientific solutions for the manufacturing of assistive devices with a sustainable 3D printing process for people with disabilities in Colombia. The project has created an innovative and tailor-made process including plastics waste recycling, assistive devices design, low cost 3D printing and local implementation to assist people with disabilities, who will become active actors of the sustainable development.
Funding
- EPFL Codev Seed fund, Tech4Dev
Project partners
- Omnis Institute and Universidad de Los Andes (Bogota, Colombia)
Resource
Yann Lebaupin, Véronique Michaud, Robin Amacher
A large proportion of 3-plane corner fittings used in the aerospace industry to attach fuselage parts are manufactured in aluminum or titanium in locations subjected to corrosion. The goal of this work is to propose carbon composite alternatives for this type of brackets, by having the same mechanical requirements at a similar cost, leading to a lower weight yet durable solution. A main contribution is to define the optimal combination of material, processing route and design to reach repeatable quality at a competitive cost.
Funding
- Innosuisse
Project partners
- Busch Composites
- HEIGVD-Yverdon
Alexandre Mordasini, Mayeul Van den Broek, Joel Cugnoni, Véronique Michaud
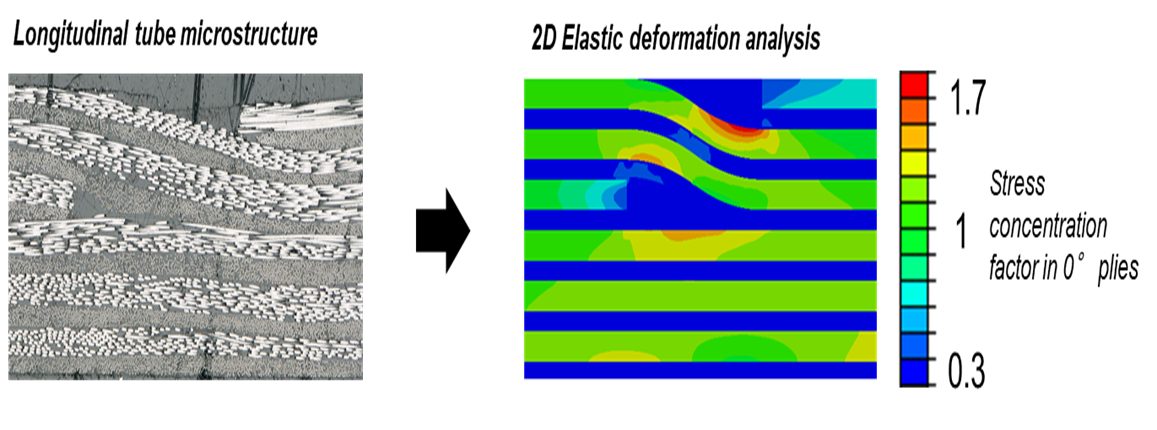
This project investigates new methods to produce composite tubes, in collaboration with NTPT. NTPT’s novel composite tube manufacturing process, using discontinuous tapes, sees its first commercial application in the golf industry, but has the potential to reach other applications, such as marine and aerospace. However, to reach the full structural potential of the tubes, in particular the needed strength in tension and compression, the complex interplay between resin and fiber selection, geometrical factors such as tape length and orientation, and manufacturing conditions need to be understood. This project aims to develop an experimental base and numerical tools enabling this manufacturing concept to produce composite tubes for applications requiring high strength to weight ratio, complex geometries and high reproducibility. A windsurf racing mast is selected as a first application case, where design flexibility and performance are the key requirements, in addition to costs compatible with the desired market range.
Funding
- Innosuisse
Partners
- EPFL LMAF
- North Thin Ply Technology (NTPT)
2018 – 2023
Helena Teixidó, Jeroen Staal, Baris Caglar, Véronique Michaud
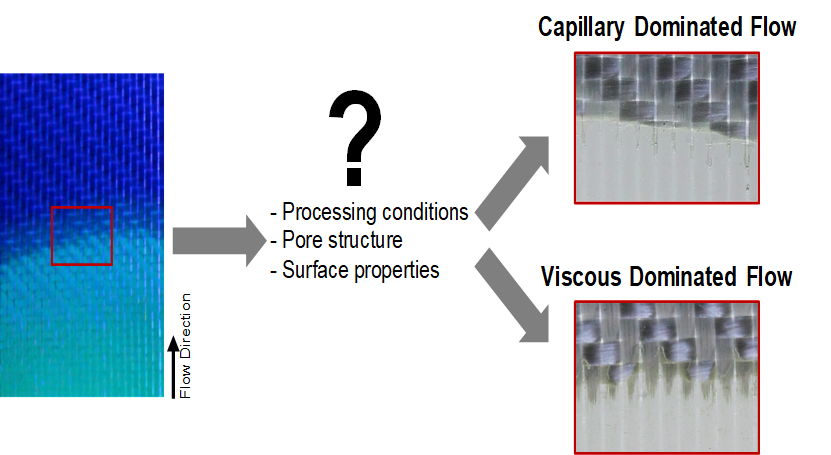
The Dynaflow project aims to probe the dynamics of flow in fibrous porous media, as used in advanced composite materials, by addressing several main points. i) One aim is to further develop the in-situ experimental methods to analyze multiphase flow processing, using advanced and novel techniques available at CSEM to enable the macro-scale observation of dynamic resin flow patterns. ii) Results of macro-scale observations will be coupled with local observation of frozen microstructures using microtomography. iii) The multiscale in-situ experimental data will feed process models that account for multiphase fluid flow effects, extended to velocity-dependent capillary forces and hierarchical pore structures.
Funding
Project partner
- CSEM – Centre Suisse d’Electronique et de Microtechnique SA
Project webpage
Publications
-
Yuksel, Onur; Caglar, Baris; Broggi, Guillaume; Michaud, Véronique; Akkerman, Remko; Baran, IsmetSaturated transverse permeability of unidirectional rovings for pultrusion: The effect of microstructural evolution through compaction. In Polymer Composites, 1–18. https://doi.org/10.1002/pc.28171
-
Staal, Jeroen; Smit, Edgar; Caglar, Baris; Michaud, VéroniqueThermal management in radical induced cationic frontal polymerisation for optimised processing of fibre reinforced polymers. In Composite Science and Technology, 237(May), 110009. https://doi.org/10.1016/j.compscitech.2023.110009
-
Teixidó, Helena; Broggi, Guillaume; Caglar, Baris; Michaud, VéroniqueMeasurement and modelling of dynamic fluid saturation in carbon reinforcements. In Composites part A, 169, 107520. https://doi.org/10.1016/j.compositesa.2023.107520
-
Caglar, B.; Broggi, G.; Ali, M.A.; Orgéas, L.; Michaud, V.Deep learning accelerated prediction of the permeability of fibrous microstructures. In Composites Part A: Applied Science and Manufacturing, 158, 106973. https://doi.org/10.1016/j.compositesa.2022.106973
-
Teixidó, H.; Staal, J.; Caglar, B.; Michaud, V.Capillary Effects in Fiber Reinforced Polymer Composite Processing: A Review. In Frontiers in Materials, 9, 809226. https://doi.org/10.3389/fmats.2022.809226
-
Caglar, Baris; Esposito, William; Nguyen‐Dang, Tung; Laperrousaz, Stella; Michaud, Véronique; Sorin, FabienFunctionalized Fiber Reinforced Composites via Thermally Drawn Multifunctional Fiber Sensors. In Advanced Materials Technologies, 6(3), 2000957–2000957. https://doi.org/10.1002/admt.202000957
-
Staal, Jeroen; Caglar, Baris; Hank, Travis; Wardle, Brian L.; Gorbatikh, Larissa; Lomov, Stepan V.; Michaud, VéroniqueIn-series sample methodology for permeability characterization demonstrated on carbon nanotube-grafted alumina textiles. In Composites Part A: Applied Science and Manufacturing, 150, 106631–106631. https://doi.org/10.1016/j.compositesa.2021.106631
-
Teixidó, Helena; Caglar, Baris; Revol, Vincent; Michaud, VéroniqueIn-operando dynamic visualization of flow through porous preforms based on X-ray phase contrast imaging. In Composites Part A: Applied Science and Manufacturing, 149, 106560–106560. https://doi.org/10.1016/j.compositesa.2021.106560
-
Daelemans, Lode; Tomme, Brecht; Caglar, Baris; Michaud, Véronique; Van Stappen, Jeroen; Cnudde, Veerle; Boone, Matthieu; Van Paepegem, WimKinematic and mechanical response of dry woven fabrics in through-thickness compression: Virtual fiber modeling with mesh overlay technique and experimental validation. In Composites Science and Technology, 207, 108706–108706. https://doi.org/10.1016/j.compscitech.2021.108706
- Caglar B, Tekin C, Karasu F, Michaud V. Assessment of capillary phenomena in liquid composite molding, Composites Part A: Applied Science and Manufacturing, 120, 73-83, 2019. https://doi.org/10.1016/j.compositesa.2019.02.018
For other outputs (conferences, data, communications), visit the project webpage
2018 – 2022
Guillaume Broggi, Alexios Argyropoulos, Joël Cugnoni, Véronique Michaud

The HyfiSyn project gathers 8 universities, 5 industrial partners and 2 professional training organizations and aims to train early stage researchers in the field of hybrid composites, in particular to explore various materials combinations to alleviate some of their main limitations, as for example their intrinsically limited toughness.One key challenge of this project, that is under investigation at EPFL, is to evaluate the effects brought by fiber hybridization in thin ply composites, which due to the limited size of each fiber layer (typically below 100µm) are generally more efficient in terms of in-plane mechanical properties, but loose in toughness. We plan to correlate mechanical performance to the hybrid microstructure configuration, through experiments and modelling, and to help design adapted manufacturing routes to produce and consolidate these hybrid composites.
Funding
- Marie Sklodowska-Curie programme (EU Horizon 2020), Duration mid 2018-mid 2022
Partners
- North Thin Ply Technology (CH)
- BMW Group (D)
- ELG carbon Fibers (UK)
- SIOEN Industries (B)
- University of Bristol (GB)
- KU Leuven (BE)
- Budapest University of Technology and Economics (HU)
- University of Nottingham (UK)
- Imperial College London (UK)
- Technical University of Denmark (DK)
- University of Vienna (A)
- 4 Real Sim
- Fiberline Composites
Website
Resources
Adrien Demongeot, Véronique Michaud

With the continuous growth of railway traffic and population in Switzerland, railway noise has become a severe environmental problem. At typical railway speeds, the most relevant source of noise is “rolling noise” emitted from the wheel and from the rail. One approach to reducing rolling noise without the cost-intensive addition of novel components to the railway track is to improve the rail pad, which forms part of the rail fastening system and typically consists of a simple rubber cushion inserted between the rails and sleepers. The aim of this project is to develop a novel rail pad system that is optimized with respect to both railway noise reduction and protection of the railway superstructure against transient loads and vibrations. The role of LPAC is centered on the determination of the optimal material microstructure to reach the desired damping properties.
Funding
- Federal Office for the Environment (4 years)
Partners
- EPFL LMOM
- EPFL LMAF
- EPFL LTS2
- EPFL TRACE
- EMPA
- HEIG-VD
- SBB-CFF-FFS
Links and resources
Damiano Salvatori, Robin Trigueira, Baris Caglar, Véronique Michaud
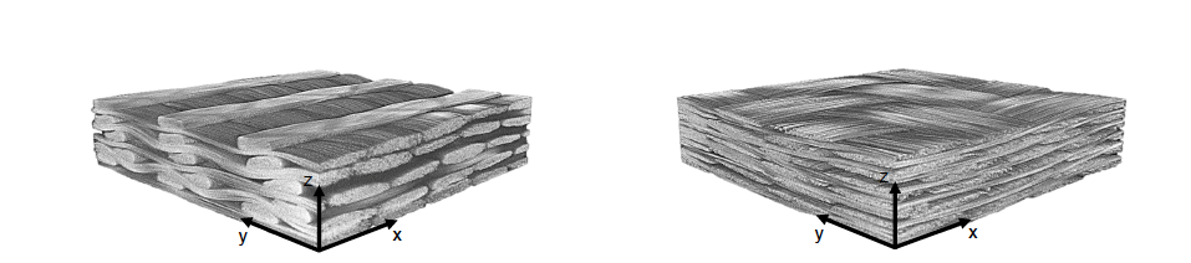
The Swiss Competence Center for Energy Research – Efficient Technologies and Systems for Mobility (SCCER Mobility) aims at developing the knowledge and technologies essential for the transition from the current fossil fuel based transportation system to a sustainable one, featuring minimal CO2 output, primary energy demand as well as virtually zero-pollutant emissions.LPAC is part of the Capacity Area A3, which investigates technologies and strategies to minimize non-propulsive energy demand of vehicles for improved efficiency. This includes the reduction of vehicle mass by replacing conventional materials such as aluminum or steel with lighter ones. To achieve this, new processing routes for high volume production of lightweight thermoplastic and bioinspired composites with outstanding mechanical properties are developed.We focus on a novel process for thermoplastic composite manufacturing for the automotive industry, exploiting the concept of Resin Transfer Molding (RTM), a common process for thermoset composites, for production of thermoplastic composites by melt processing of a low viscosity thermoplastic matrix.
Funding
- Innosuisse (Swiss Competence Center for Energy Research-Mobility)
Partners
- Solvay – Research Center of Lyon (France)
Website
Publications
- D. Salvatori, B. Caglar, H. Teixido, V. Michaud, Permeability and Capillary Effects in a Channel-wise Non-Crimp Fabric, Composites part A, 108, 2018, 41–52. https://doi.org/10.1016/j.compositesa.2018.02.015D
- Salvatori, B. Caglar, V. Michaud, 3D Spacers Enhance Flow Kinetics in Resin Transfer Molding with Woven Fabrics, Composites part A, 119, 2019, 206-216. https://doi.org/10.1016/j.compositesa.2019.01.023B
- Caglar, D. Salvatori, E. Murat Sozer, V. Michaud, In-plane permeability distribution mapping using resin flow front detection, Composites Part A, 113, 2018, 275-286. https://doi.org/10.1016/j.compositesa.2018.07.036
Kyungjin Kim, Julien Carron, Yves Leterrier
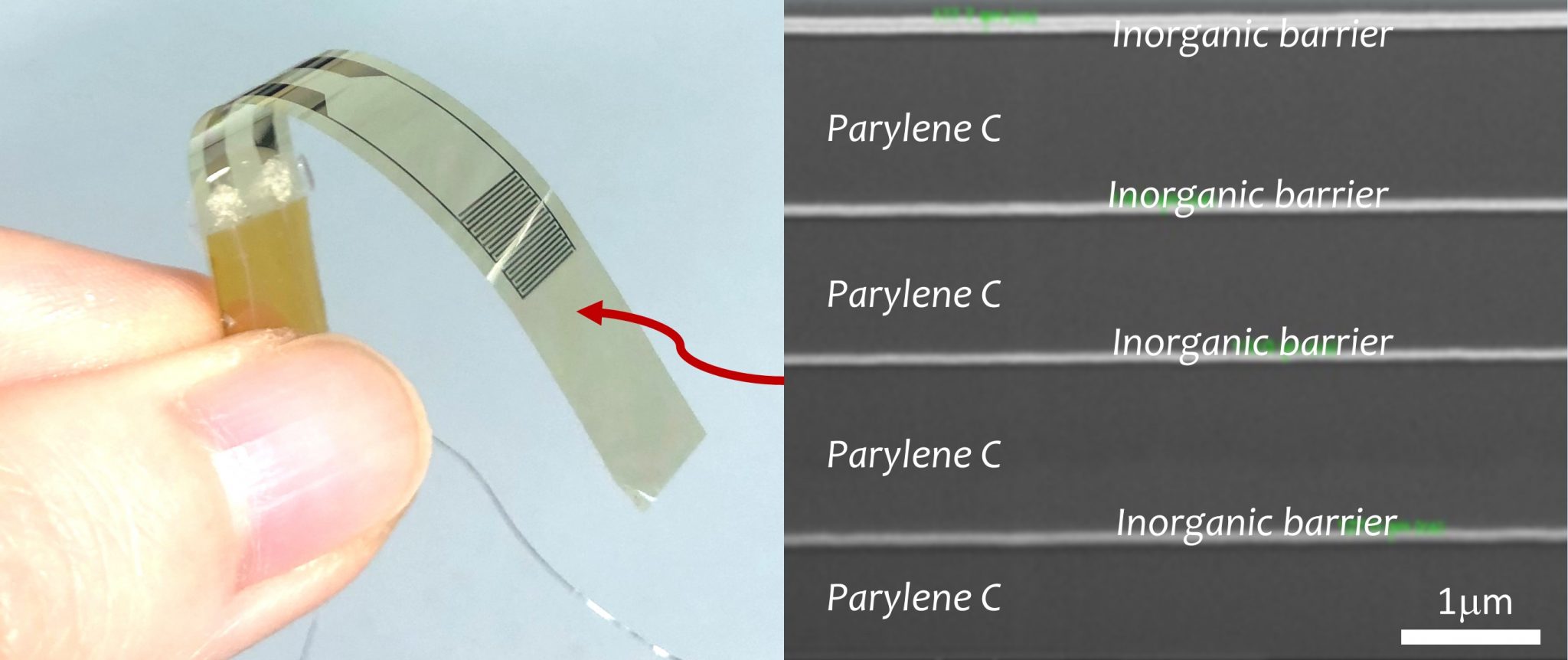
XInoCaps is a Comelec SA-LSBI-LPAC collaboration to develop organic/inorganic barrier coatings for implantable medical devices. The multilayer coatings combine Parylene C and inorganic ALD/PECVD films. These coatings are produced in a new kind of hybrid equipment developed by Comelec, allowing alternative depositions in a single deposition chamber. Specifically, LPAC designs and characterizes the multilayer structure to improve both flexibility and barrier performance in terms of crack onset strain, oxygen/water vapor permeability, and lifetime of barrier coated electrodes. Our ultimate goal is to standardize such design and procedure to coat any fabricated flexible devices at low temperature and demonstrate a new generation of soft biomedical implants with improved lifetime reliability.
Funding
Innosuisse
Partner
- Comelec SA (http://www.comelec.ch)
- Laboratory for Soft Bioelectronic Interfaces (LSBI-EPFL)